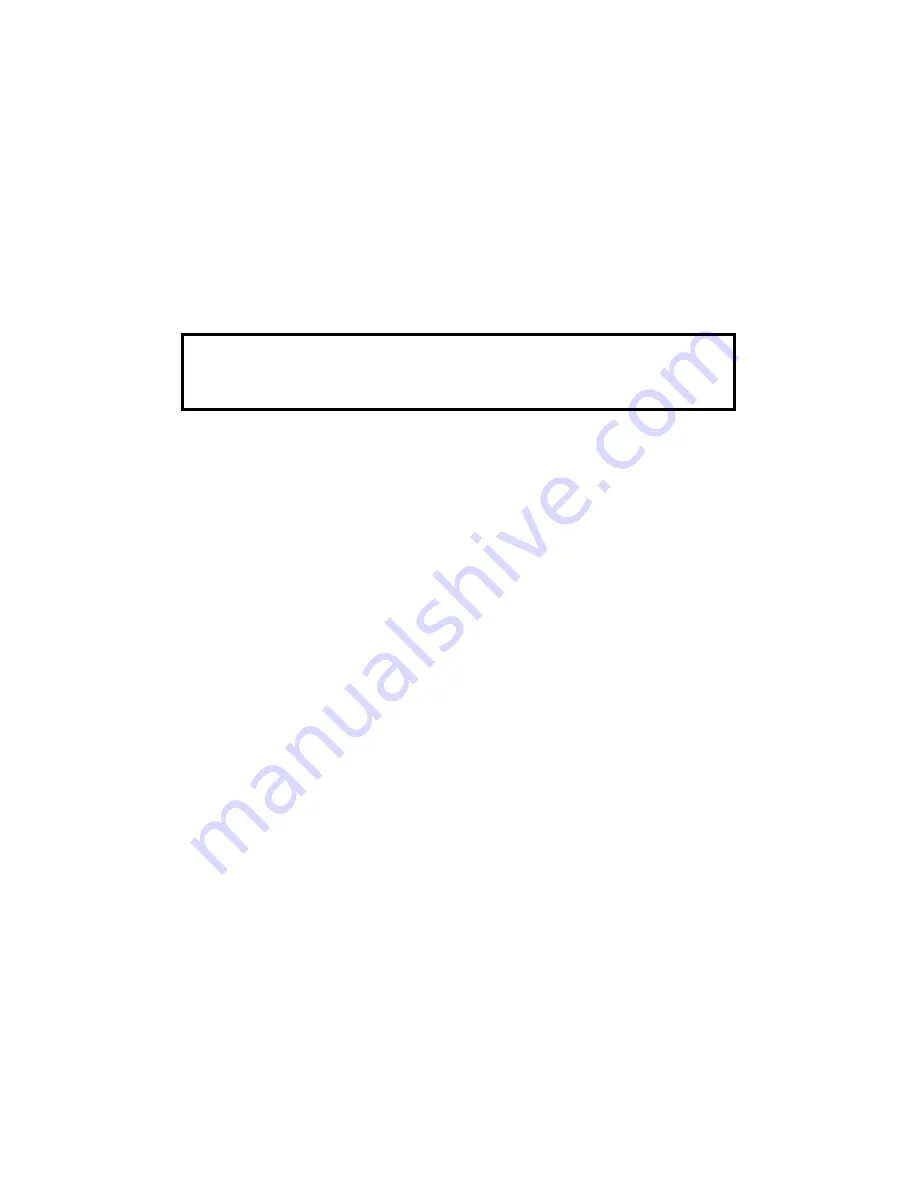
13
9. Maintenance and cleaning
The operator has to make sure that safety-relating and machine-technical installations are inspected by an expert
after every four years in the course of an acceptance test.
The operator has to make sure that safety-relating and machine-technical installations are inspected by a skilled
person once a year.
The following points have to be considered during the inspection:
1) All screws used for installing the devices or parts of the device have to be tighly connected and must not be
corroded.
2) There must not be any deformations on housings, fixations and installation spots (ceiling, suspension, trussing).
3) Mechanically moved parts like axles, eyes and others must not show any traces of wearing (e.g. material
abrading or damages) and must not rotate with unbalances.
4) The electric power supply cables must not show any damages, material fatigue (e.g. porous cables) or sediments.
Further instructions depending on the installation spot and usage have to be adhered by a skilled installer and
any safety problems have to be removed.
DANGER TO LIFE!
Disconnect from mains before starting maintenance operation!
It is absolutely essential that the fixture is kept clean and that dust, dirt and smoke-fluid residues must not build
up on or within the fixture. Otherwise, the fixture‘s light-output will be significantly reduced. Regular cleaning will
not only ensure the maximum light-output, but will also allow the fixture to function reliably throughout its life.
Please use a moist, lint-free cloth. Never use alcohol or solvents!
The front mirror objective lens will require weekly cleaning as smoke-fluid tends to building up residues, reducing
the light-output very quickly. The cooling-fans should be cleaned monthly.
The gobos may be cleaned with a soft brush. The interior of the fixture should be cleaned at least annually using
a vacuum-cleaner or an air-jet.
The dichroic colour-filters and the internal lenses should be cleaned monthly.
There are no serviceable parts inside the device except for the lamp and the fuse. Maintenance and service
operations are only to be carried out by authorized dealers.
Please refer to the instructions under „Fitting/Exchanging the lamp“.
Replacing the fuse
If the lamp burns out, the fine-wire fuse of the device might fuse, too. Only replace the fuse by a fuse of the same
type and rating .
Before replacing the fuse, unplug mains lead.
Procedure:
Step 1: Unscrew the fuse holder on the front panel with a fitting screwdriver from the housing (anti-clockwise).
Step 2: Remove the old fuse from the fuseholder.
Step 3: Install the new fuse in the fuseholder.
Step 4: Replace the fuseholder in the housing and fix it.
Should you need any spare parts, please use genuine parts.
If the power supply cable of this device becomes damaged, it has to be replaced by authorized dealers only in
order to avoid hazards.
Should you have further questions, please contact your dealer.
Version 1.1
Summary of Contents for DJ SCAN 150 XT
Page 1: ......