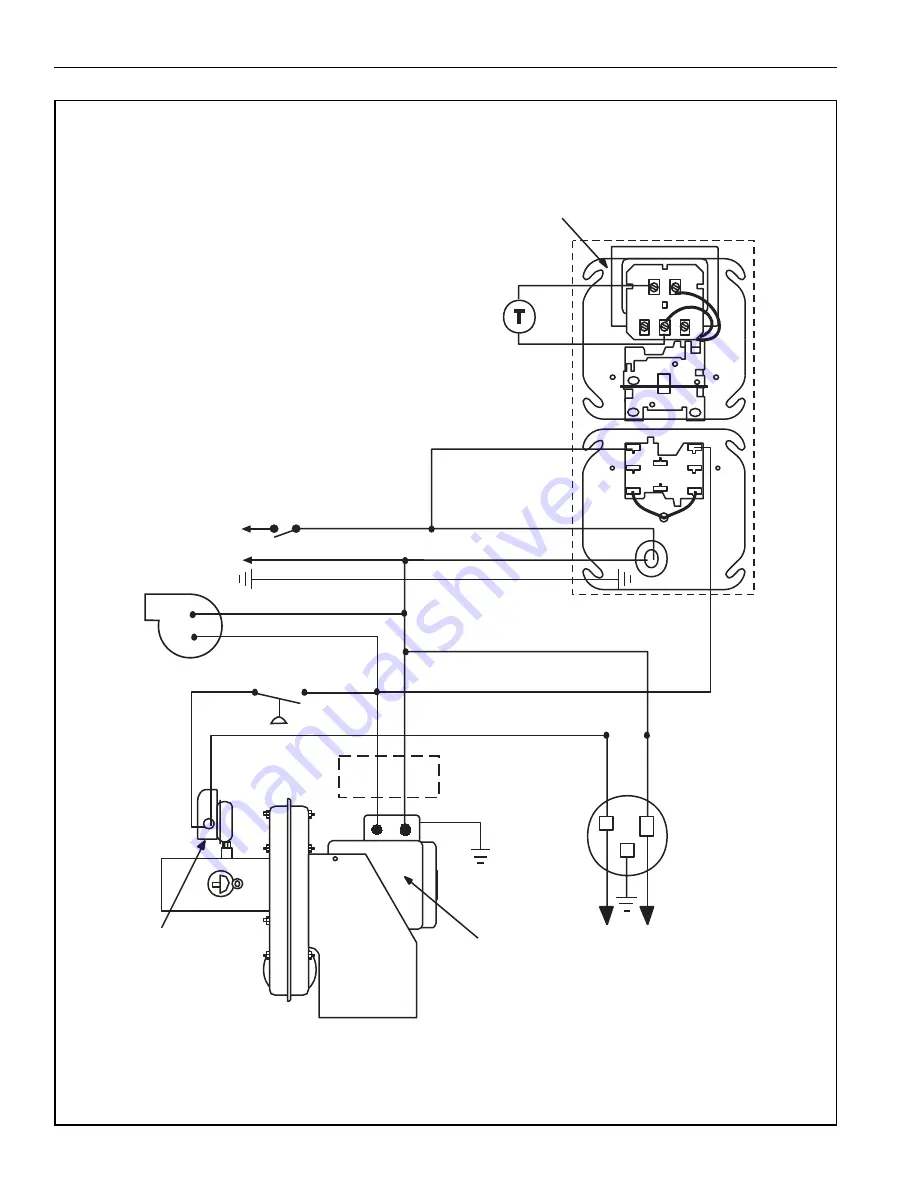
CRV-S
ERIES
I
NSTALLATION
, O
PERATION
AND
S
ERVICE
M
ANUAL
44
FIGURE 27: One Zone Operation (with Outside Air Blower) without Control Panel
1
2
3
4
5
6
COIL
COIL
R C
W G
Y
Thermostat
Pump
Motor
Pressure
Switch
(Pump)
SPST (12 A)
Transformer
Relay
Zone 1
Burners
N
L
L
N
Nine Burners Maximum
Black
White
Red
Black
L
120 V
1 Ø
60 Hz
N
Ground
Pressure Switch
(Outside Air Blower)
N
L
Outside Air
Blower