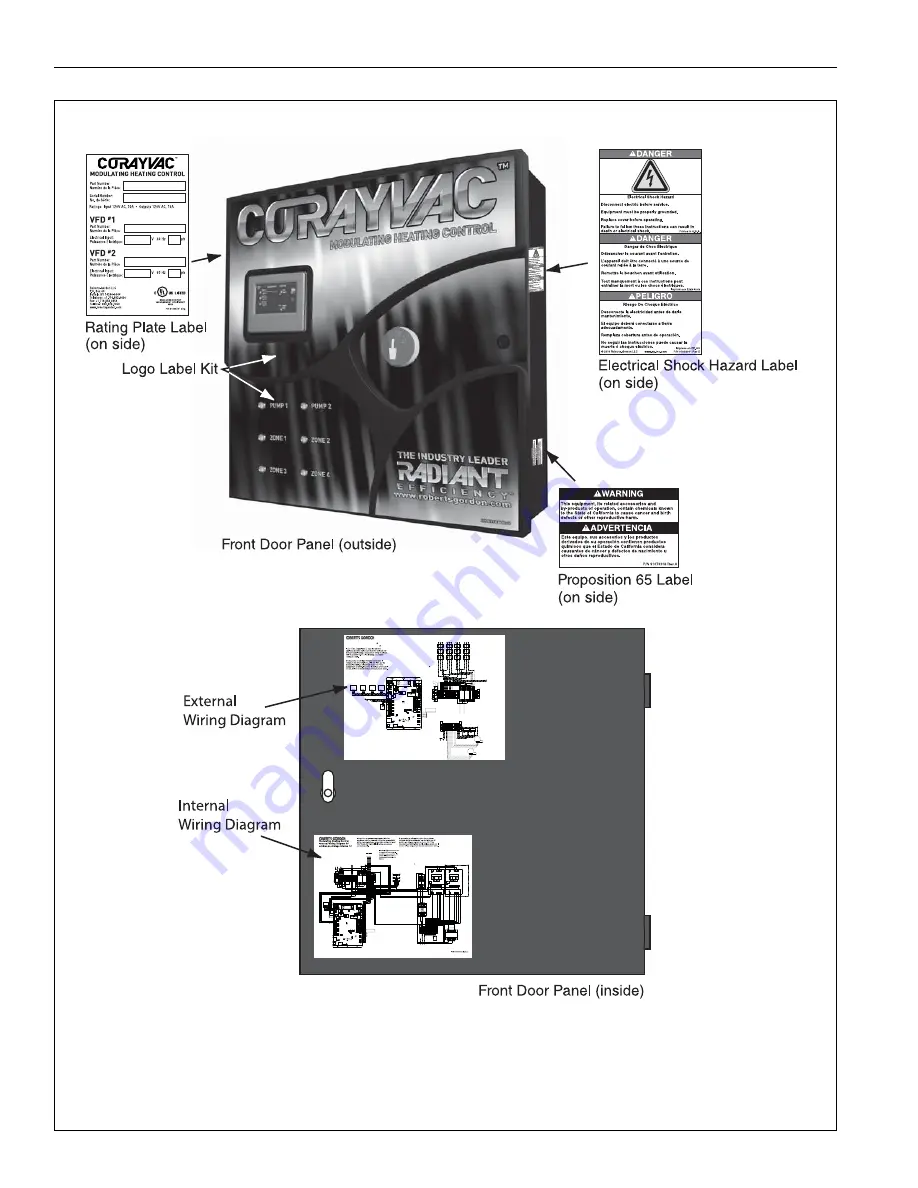
ROBERTS GORDON
®
CORAYVAC
®
M
ODULATING
H
EATING
C
ONTROL
C
ONTROLLER
I
NSTALLATION
M
ANUAL
4
FIGURE 2: CORAYVAC
®
Modulating Heating Control Label Placement
P/N 91006104 Orig.
Modulating Heating Control
External Wiring Diagram 1
schéma de câblage externe 1
PUMP 1
PUMP 2
U
ZONE 1
SENSOR
+12V
Rn
e
t-
R
n
et+
Gnd
ZONE 2
SENSOR
+12V
Rn
e
t-
R
n
et+
Gnd
ZONE 3
SENSOR
+12V
Rn
e
t-
R
n
et+
Gnd
ZONE 4
SENSOR
+12V
Rn
e
t-
R
n
et+
Gnd
L2
U1 V1 W1
U2 V2 W2
G
G
G
L1
L3
24V
ac
24V
ac
N1
L
Outside Air
Blower 1
Outside Air
Blower 2
V W G
U V W G
N M
L N M
T1 T2 T3
T1 T2 T3
N G
G
N
L L L L
N N N N
G
N1
24V
ac
N1
24V
ac
RELA
Y 3
RELA
Y 2
RELA
Y 1
RELA
Y 5
RELA
Y 6
RELA
Y 4
24V
ac
24V
ac
N1
Zone 1
Burners
Zone 2
Burners
Zone 3
Burners
Zone 4
Burners
Pump Operated Zones
G
N
L
G
N
L
G
N
L
G
N
L
Modulation signals
to Unitary heaters
Zone 1 Unitary
Zone 2 Unitary
Zone 3 Unitary
Zone 4 Unitary
VFD PWR IN
OUTDOOR
SENSOR
Relay
5
Relay
6
OA
BLWR 1
OA
BLWR 2
88F0
E143900
TYPE: 002003
Power
Off On
Power
Gnd
24Vac
Port 1
485
ARC-
Shield
Net -
Net +
156
Port 2a
Rnet
Gnd
Rnet +
Rnet -
+12V
Xnet +
Xnet -
Gnd
Xnet Expansion
Local
Rnet+
Gnd
Sense
+12V
Rnet-
Access
EIA-485
EIA-232
Thermistor/
dry-contact/
Mode Select
Universal Input
mA
RTD
Volts
10V Max, 20mA Max
Inputs: All
UI-4
UI-3
UI-2
UI-1
Gnd
+
Gnd
Gnd
+
+
Gnd
+
8
7
6
5
4
3
2
1
UI-8
Gnd
UI-6
UI-7
UI-5
Gnd
+
+
Gnd
+
Gnd
+
UI-12
UI-11
UI-10
UI-9
+
Gnd
+
Gnd
Gnd
+
Gnd
+
24 Vdc
24 Vdc
200mA maximum
Auto Off On
0-20mA
0-10Vdc
Relay
Controller
Address
1's
10's
Archive Valid
Port 2a Rx
Port 2a Tx
Port 1 Rx
Port 1 Tx
Battery low
Ext. Batt.
Int. Batt.
External
Battery
Gnd
+3V
Status
Module
3V Lithium Battery
CR-123A
0 = Download required
3 = Comm setup error
1 = Control Program Error
4 = System error
8 = Formatting
2 = RAM full
Chase = OK
Status Codes
Class 2
ONLY Use Copper
24Vac, 50VA
Without Keypad:
26Vdc, 23W, 0.9A
Outputs
24Vdc Max, 50mA Max
Format
Pot
2-wire
4-wire
2 wire 4 wire
Rx -
Net-
Net+
n/c
Tx -
Tx +
Rx +
n/c
EIA-232
DCD
Rx
Tx
DTR
Signal Ground
®
BACnet
Over ARCNET156 KBaud
Made in USA
Port 2a BT485
Port 1
Port 1 BT485
Conductors
2A, 50-60 Hz
Blinking Dot = 'Run'
On
Off
Enhanced
8
7
6
5
4
3
2
1
8
7
6
5
4
3
2
1
IP Addr
Assigned Default
10/100 BaseT
Ethernet Port E1
100
LAN
LINK
®
8
7
6
5
See BAS Table Below
Protocols 6
MS/TP m
MS/TP s
Off
N2
On
Lon SLTA
Off
BAUD 4
5
9600 Off
Off
19.2 K Off
On
38.4 K On Off
76.8 K On
On
On
Modbus
8
Off
Off
On
On
Off
4
BACnet
3
7
Off
On
Off
Off
Off
PTP
Off
Off
On
Access Port 2a
Lon OptionOff
On
On
2
1
UO-1
UO-2
UO-3
UO-4
UO-8
UO-7
UO-6
UO-5
On
Off
2
1
BAS Port
BAS Port Settings
Set Pot Full CW
24Vac
DO NOT APPLY 24Vac TO
UNIVERSAL OUTPUTS
External 24Vdc relay coil only
Brownout
3
UO-2
UO-1
2
1
UO-4
UO-3
6
5
4
7
8
6
UO-7
UO-6
UO-5
3
1
2
4
5
UO-8
7
8
+
Gnd
+
Gnd
+
Gnd
+
Gnd
+
Gnd
+
Gnd
+
Gnd
+
Gnd
Aux Power Out
Port 2b
Port 2a
IOPro812u
07/10/12
Rev 6
Open Energy
Management Equipment
26Vdc
I/O Pro 812u
CONTROLLER
+ -
BLOWERS OPTIONAL
TERMINAL BL
OCK 2
CONNECTIONS INDICATED BY
CB2
20A
11
14
12
COM
NO
NC
11
14
12
COM
NO
NC
(A1)
(A2)
TERMINAL BL
OCK 1
11
14
12
COM
NO
NC
(A1)
(A2)
11
14
12
COM
NO
NC
(A1)
(A2)
11
14
12
COM
NO
NC
(A1)
(A2)
11
14
12
COM
NO
NC
(A1)
(A2)
11
14
12
COM
NO
NC
11
14
12
COM
NO
NC
11
14
12
COM
NO
NC
11
14
12
COM
NO
NC
(A1)
(A2)
11
14
12
COM
NO
NC
11
14
12
COM
NO
NC
115V/230V 1
L1/L
L2/N
GND
120V 60HZ
1 20A
L
N
GND
FROM
PS2
FROM
PS1
CONTROL PWR IN
TO PS 1
TO PS 2
120VAC
60HZ 15A
120VAC
60HZ 15A
BLK
WHT
GRN
BLK
WHT
GRN
N G
G
N
L L L L
N N N N
L1/L
POWER INPUT
POWER OUTPUT
POWER INPUT
POWER OUTPUT
G
CB1
VFD1
VFD2
Disconnect, 30A
L2
U1 V1 W1
U2 V2 W2
G
G
G
L3
CB1
24Vac
N1/Gnd
TOUCH
SCREEN
+24V
MS/TP
+
Gnd
SENSOR
A B C D
S2
S1
MS/TP
-
N1
24V
ac
N1
24V
ac
P1
P2
Z1
Z2
Z3
Z4
TRANSFORMER
24V
ac
24V
ac
N1
L2/N L3
L1/L L2/N L3
RELA
Y 3
RELA
Y 2
RELA
Y 1
RELA
Y 5
RELA
Y 6
RELA
Y 4
24V
ac
24V
ac
N1
120V 60HZ
1 20A
L1/L
115V/230V 1
L2/N GND
L
N
GND
FROM
PS2
FROM
PS1
88F0
E143900
TYPE: 002003
Power
Off On
Power
Gnd
24Vac
485
ARC-
Shield
Net -
Net +
156
Port 2a
Rnet
Gnd
Rnet +
Rnet -
+12V
Xnet +
Xnet -
Gnd
Xnet Expansion
Local
Rnet+
Gnd
Sense
+12V
Rnet-
Access
EIA-485
EIA-232
Thermistor/
dry-contact/
Mode Select
Universal Input
mA
RTD
Volts
10V Max, 20mA Max
Inputs: All
UI-4
UI-3
UI-2
UI-1
Gnd
+
Gnd
Gnd
+
+
Gnd
+
8
7
6
5
4
3
2
1
UI-8
Gnd
UI-6
UI-7
UI-5
Gnd
+
+
Gnd
+
Gnd
+
UI-12
UI-11
UI-10
UI-9
+
Gnd
+
Gnd
Gnd
+
Gnd
+
24 Vdc
24 Vdc
200mA maximum
Auto Off On
0-20mA
0-10Vdc
Relay
Controller
Address
1's
10's
Archive Valid
Port 2a Rx
Port 2a Tx
Port 1 Rx
Port 1 Tx
Battery low
Ext. Batt.
Int. Batt.
External
Battery
Gnd
+3V
Status
Module
3V Lithium Battery
CR-123A
0 = Download required
3 = Comm setup error
1 = Control Program Error
4 = System error
8 = Formatting
2 = RAM full
Chase = OK
Status Codes
Class 2
ONLY Use Copper
24Vac, 50VA
Without Keypad:
26Vdc, 23W, 0.9A
Outputs
24Vdc Max, 50mA Max
Format
Pot
2-wire
4-wire
2 wire4 wire
Rx -
Net-
Net+
n/c
Tx -
Tx +
Rx +
n/c
EIA-232
DCD
Rx
Tx
DTR
Signal Ground
®
BACnet
Over ARCNET156 KBaud
Made in USA
Port 2a BT485
Port 1
Port 1 BT485
Conductors
2A, 50-60 Hz
Blinking Dot = 'Run'
On
Off
Enhanced
8
7
6
5
4
3
2
1
8
7
6
5
4
3
2
1
IP Addr
Assigned Default
10/100 BaseT
Ethernet Port E1
100
LAN
LINK
®
8
7
6
5
See BAS Table Below
Protocols 6
MS/TP m
MS/TP s
Off
N2
On
Lon SLTA
Off
BAUD 4
5
9600 Off
Off
19.2 K Off
On
38.4 K On Off
76.8 K On
On
On
Modbus
8
Off
Off
On
On
Off
4
BACnet
3
7
Off
On
Off
Off
Off
PTP
Off
Off
On
Access Port 2a
Lon OptionOff
On
On
2
1
UO-1
UO-2
UO-3
UO-4
UO-8
UO-7
UO-6
UO-5
On
Off
2
1
BAS Port
BAS Port Settings
Set Pot Full CW
24Vac
DO NOT APPLY 24Vac TO
UNIVERSAL OUTPUTS
External 24Vdc relay coil only
Brownout
3
UO-2
UO-1
2
1
UO-4
UO-3
6
5
4
7
8
6
UO-7
UO-6
UO-5
3
1
2
4
5
UO-8
7
8
+
Gnd
+
Gnd
+
Gnd
+
Gnd
+
Gnd
+
Gnd
+
Gnd
+
Gnd
Aux Power Out
Port 2b
Port 2a
IOPro812u
07/10/12
Rev 6
Open Energy
Management Equipment
26Vdc
I/O Pro 812u
CONTROLLER
CB2
20A
3
10
U
OK
OK
11
14
12
COM
NO
NC
11
14
12
COM
NO
NC
(A1)
(A2)
VFD1
OUT
VFD2
OUT
TERMINAL BL
OCK 1
VFD2
OPTIONAL
Single pole circuit
breaker for 115V
O
A
Blo
w
er 1
O
A
Blo
w
er 2
O
A
Blo
w
ers
CONNECTIONS INDICATED BY
4 5 6 7 8 9
2
1
11
3
10
4 5 6 7 8 9
2
1
11
V W
U V W
11
14
12
COM
NO
NC
(A1)
(A2)
11
14
12
COM
NO
NC
(A1)
(A2)
11
14
12
COM
NO
NC
(A1)
(A2)
11
14
12
COM
NO
NC
(A1)
(A2)
11
14
12
COM
NO
NC
11
14
12
COM
NO
NC
11
14
12
COM
NO
NC
11
14
12
COM
NO
NC
(A1)
(A2)
11
14
12
COM
NO
NC
11
14
12
COM
NO
NC
Modulation signals
to Unitary heaters
Zone 1 Unitary
Zone 2 Unitary
Zone 3 Unitary
Zone 4 Unitary
CONTROL PWR IN
VFD PWR IN
TO ZONE
SENSORS
TO RELAY 6
OUT AIR TEMP
L1
RS485
TERMINAL BL
OCK 2
Indicator Lights
(Optional)
(Optional)
Zo
n
e
4
Zo
n
e
3
Zo
n
e
2
Zo
n
e
1
Pump
operated
zones
UI-1
UI-2
TO RELAY 5
TO PS 1
TO PS 2
BLK
WHT
GRN
BLK
WHT
GRN
Summary of Contents for CORAYVAC
Page 2: ......
Page 4: ......
Page 69: ...SECTION 8 PROGRAMMING AND TROUBLESHOOTING THE SYSTEM 65 THIS PAGE LEFT INTENTIONALLY BLANK ...
Page 71: ...SECTION 9 TROUBLESHOOTING 67 FIGURE 26 Vacuum pump does not turn on ...
Page 75: ...SECTION 9 TROUBLESHOOTING 71 FIGURE 31 Burner troubleshooting in manual mode ...
Page 77: ...SECTION 9 TROUBLESHOOTING 73 After 45 second prepurge burners do not light continued ...
Page 81: ...SECTION 9 TROUBLESHOOTING 77 FIGURE 36 Air Pressure Switch alarm ...
Page 83: ...SECTION 9 TROUBLESHOOTING 79 FIGURE 38 Repeater troubleshooting ...
Page 85: ...SECTION 9 TROUBLESHOOTING 81 BACnet MS TP troubleshooting continued ...
Page 109: ...SECTION 13 TOUCHSCREEN TREE 105 Touchscreen Tree Overview continued ...
Page 111: ...SECTION 13 TOUCHSCREEN TREE 107 FIGURE 47 Maintenance Unit FIGURE 48 Alarms ...
Page 113: ...SECTION 13 TOUCHSCREEN TREE 109 FIGURE 51 Configuration Zones FIGURE 52 Configuration Unit ...
Page 115: ...SECTION 13 TOUCHSCREEN TREE 111 FIGURE 55 Touchscreen System FIGURE 56 Touchscreen Setup ...
Page 118: ...ROBERTS GORDON CORAYVAC MODULATING HEATING CONTROL CONTROLLER INSTALLATION MANUAL 114 ...