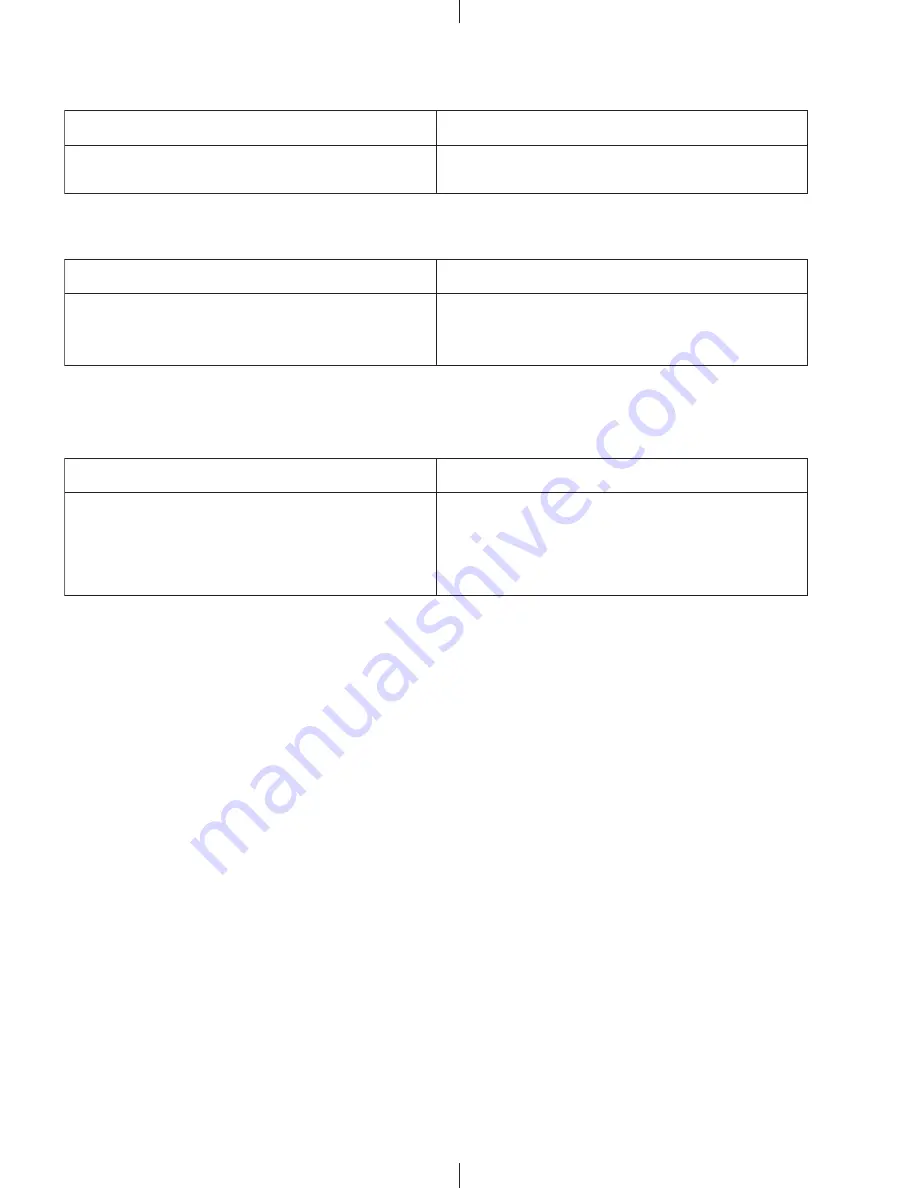
- 82 -
17-5 INSPECTION AND MAINTENANCE EVERY 300 HOURS
17-6 INSPECTION AND MAINTENANCE EVERY 500 TO 600 HOURS (EVERY 6 MONTHS)
17-7 MAINTENANCE EVERY 1,000 HOURS (ANNUAL MAINTENANCE)
17-8 ENGINE STORAGE
(1) Carry out the maintenance jobs described in step 16-1 above.
(2) Drain fuel from the fuel tank and carburetor float chamber.
(3) To prevent rust in the cylinder bore, inject oil through the spark plug hole, pull the recoil starter knob
gently 2 or 3 times and then put back the spark plug.
(4) Pull the recoil starter knob until the resistance is heavy. Leave it in that position.
(5) Clean the exterior of the engine with an oiled cloth. Place a plastic cover or similar over the engine, and
store the engine in a dry place.
MAINTENACE ITEMS
REASON / REMARKS
(1) Overhaul the engine. Clean and correct the
engine parts, replacing if necessary.
(2) Replace the piston rings.
(3) Replace the fuel hose.
(1) Dirty, misaligned or worn parts can cause low
power output and engine malfunction.
(2) Faulty piston rings can cause low output power
and engine malfunction.
(3) To prevent fuel leakage and attendant dangers.
MAINTENACE ITEMS
REASON / REMARKS
(1) Remove the cylinder head and remove any carbon.
(2) Disassemble and clean the carburetor.
(1) Carbon deposits can cause engine malfunction.
(2) A faulty carburetor can cause engine malfunction.
MAINTENACE ITEMS
REASON / REMARKS
(1) Inspect the intake and exhaust valve clearance.
Adjust if necessary.
(1) Incorrect clearance can cause low power output
and engine malfunction.
Summary of Contents for EX13
Page 1: ...SERVICE MANUAL EX13 17 21 27 SP170 SP210 ENGINES Models PUB ES1934 Rev 06 09 ...
Page 3: ......
Page 87: ......
Page 88: ...PRINTED IN THE USA ...