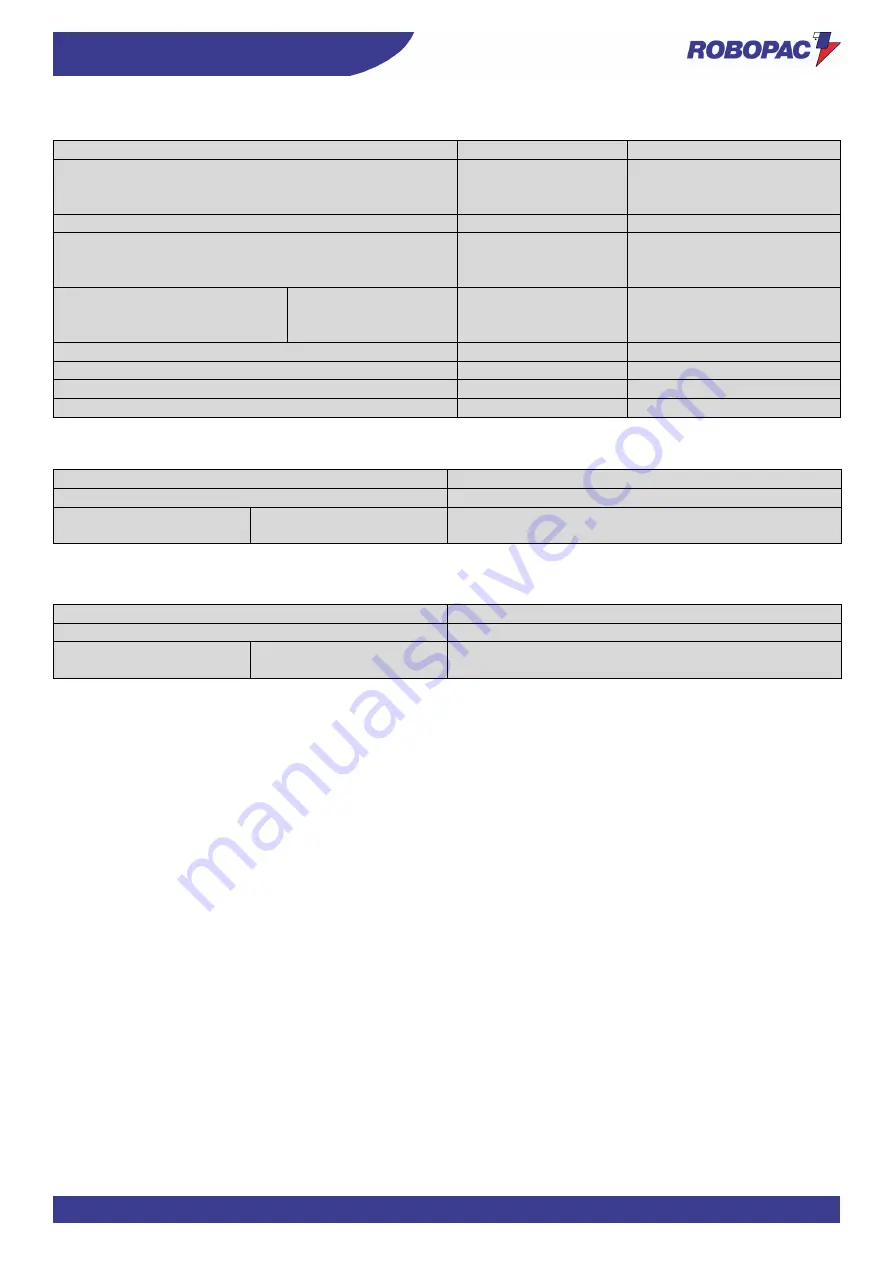
ENG
TECHNICAL INFORMATION
40
3.7.2. MACHINE TECHNICAL FEATURES
Description
Unit of measurement
EU
Supply voltage
V
220÷240 1Ph
220÷240 3Ph
380÷415 3Ph+N
Power supply frequency
Hz
50/60
Power
installed
kW
1.5 (Rotoplat 108 - 308)
1.9 (Rotoplat 508)
2.4 (Rotoplat 708)
Table
rotation speed
C=1650
C=1800
C=2200-2400
rpm
5-12
5-11
5-8
Carriage upstroke / downstroke speed
m/min.
1.5-5.5
Maximum capacity
kg
2000
Overall weight
kg
395÷455
Ambient operating temperature
°C
0÷40
3.7.3. PRESSER TECHNICAL FEATURES
Description
Value
Working pressure
6 (±1) bar (0.6±0.1 MPa)
Pneumatic cylinder with
rod
H=2200/2400
2800/3100
Air consumption
11 Nl/min
3.7.4. PNEUMATIC CREASING HEAD TECHNICAL FEATURES
Description
Value
Working pressure
6 (±1) bar
Pneumatic
cylinder
without rod
H=450
Air consumption
2 Nl/min