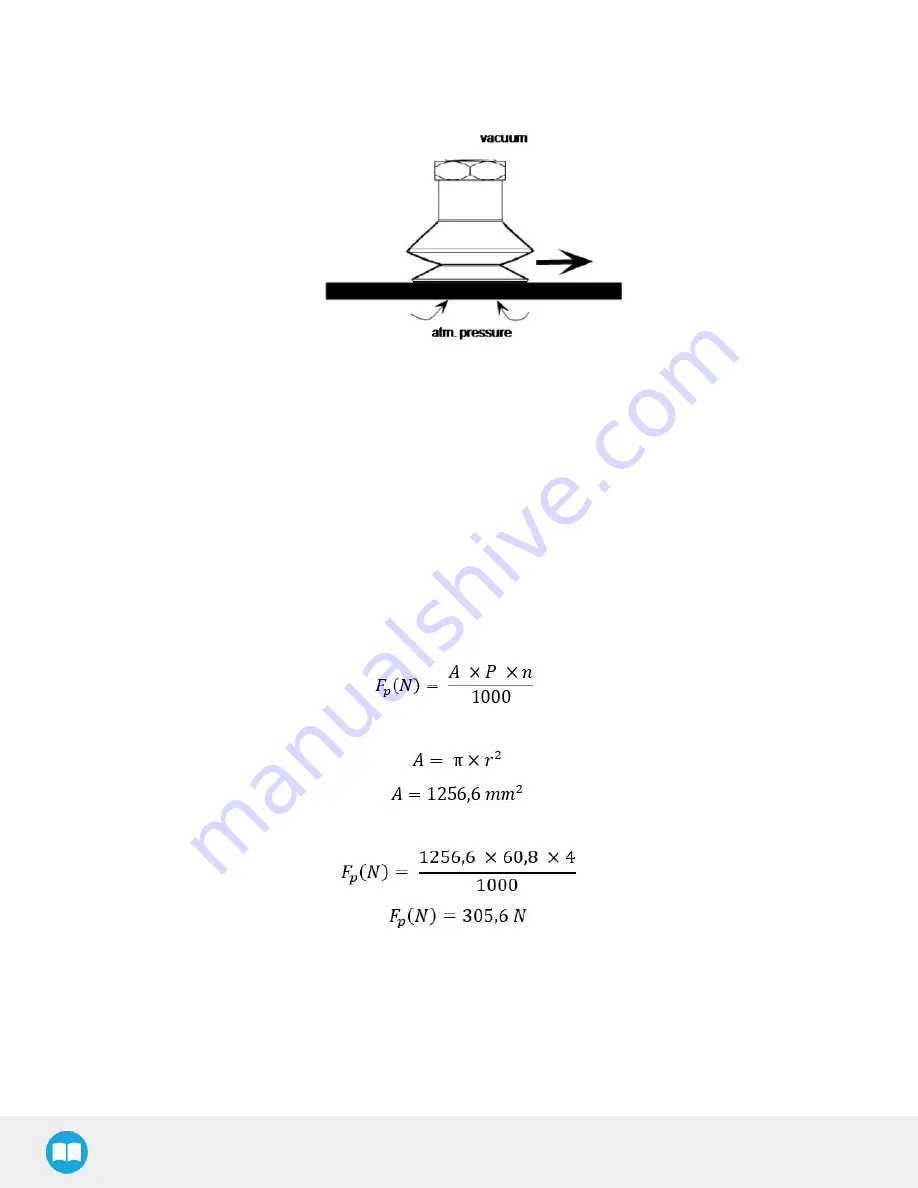
Example 1: Non-porous material
Fig. 6-10: Non-porous material
Initial data:
l
Material type: non-porous
l
Application type: Case #2
l
Suction cup diameter (d): 40 mm (r=20 mm)
l
Percentage of vacuum: 60% (which is equivalent to 60.8 kPa, according to the conversion table above)
l
Mass: 2 kg
l
Acceleration: 1.2 m/s
2
l
n = 4
Case #2
l
m = 2 kg
l
g = 9.81 m/s
2
l
a = 1.2 m/s
2
84
Summary of Contents for AirPick
Page 25: ...Fig 3 7 Mounting air nodes suction cups air bolts air nuts on the bracket 25...
Page 27: ...Fig 3 9 Robotiq Vacuum Gripper with pigtail cable and device cable wiring scheme 27...
Page 35: ...Fig 4 1 Vacuum Gripper control logic overview 35...
Page 57: ...7 Click on the New Project icon in the upper left corner of the screen 57...
Page 58: ...AirPick Instruction Manual 8 Enter a name for your program and click on the OK button 9 58...
Page 76: ...Fig 6 5 Minimum and maximum arrangement possibilities of the air nodes position 76...
Page 77: ...AirPick Instruction Manual 6 1 3 Air nodes Fig 6 6 Air nodes dimensions 77...
Page 103: ...AirPick Instruction Manual 12 Appendix Fig 12 1 Pneumatic schema of the AirPick Vacuum Gripper...