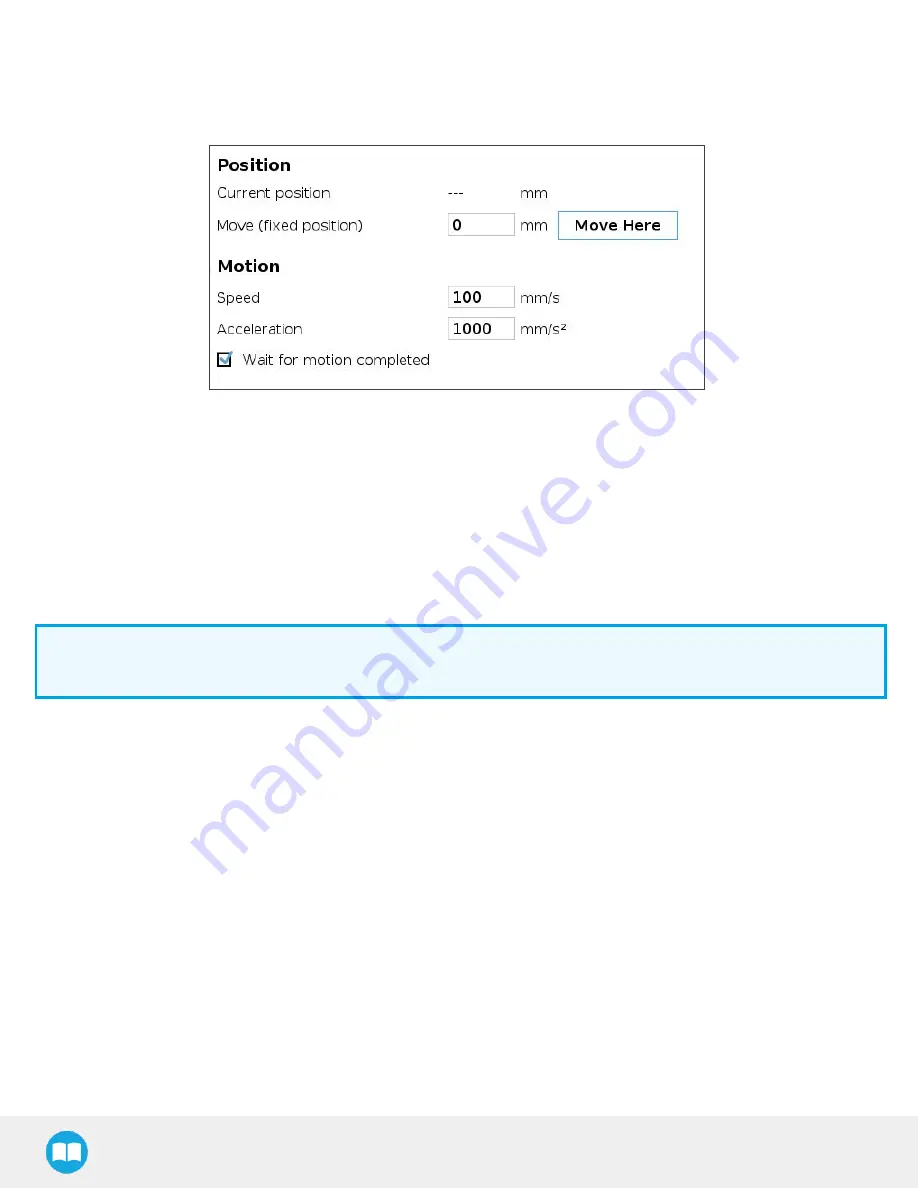
5.1.2. Linear Axis Move node
l
The Linear axis move node can be used to move the linear axis to a specific position. It can be used inside or outside the Palletizer
node.
5.2. Vacuum Gripper behavior
Workpiece gripping / releasing is performed by changing the values of the gripper input registers. While the control is very simple,
some behaviors deserve a better explanation. The Vacuum Gripper can work in two different mode: the Automatic and Advanced
modes. For more details, please refer to the AirPick Vacuum Gripper instructions manual.
5.3. AirPick Vacuum control over Universal Robots with URCaps
Info
Please refer to the AirPick Vacuum Gripper instructions manual to have all the information about the URCap.
70
Summary of Contents for PALLETIZING SOLUTION
Page 12: ...Palletizing Solution Instruction Manual 12...
Page 72: ...6 1 2 AirPick Vacuum Gripper Fig 6 1 AirPick general dimensions 72...
Page 73: ...Palletizing Solution Instruction Manual 6 1 3 Extra Reach Bracket 73...
Page 74: ...6 1 4 Bracket for two 2 Suction Cups Fig 6 2 Two air nodes bracket s dimensions 74...
Page 80: ...80...
Page 95: ...1 2 2 Safety Connections Fig 12 2 Universal Robots Controller Safety Connections Schema 95...