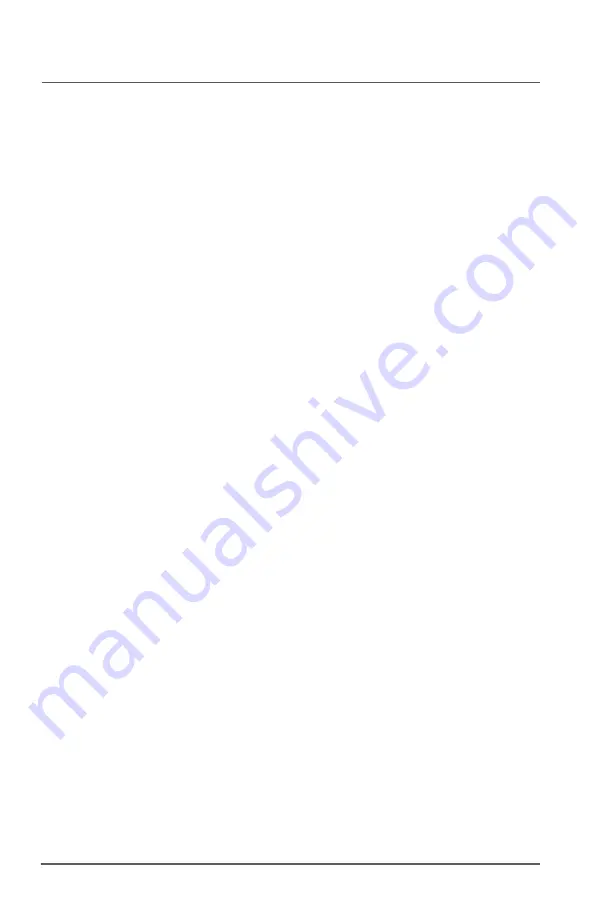
32
ROBOVENT • PFX SERIES OWNER’S MANUAL
SECTION 800
Standard Maintenance
Note: To be performed while there is no welding occurring
1. Record
ΔP/Static pressure reading from the controller while the unit is operating.
2. Turn off the system. (Blower motor only!)
3. Remove and replace Spark Arrestance filters. (Metal mesh in first track at intake).
A.
Clean the entire inlet plenum to include:
i.
Spark arrestor filter (metallic filter) tracks and cover door
ii.
Inlet Plenum Box (inside and outside)
Note:
Most particulate can usually be vacuumed out; however, if it is high in oil content, it
will tend to smear. If smearing occurs then a commercial degreaser can be used to assist in
cleaning. The cleaning does not have to return the system to new condition, but should be
void of pockets of particulate.
4. Replace metal mesh filters in the filter cabinet with clean ones.
5. Clean out bottom of filter cabinet.
6. Vacuum out the visible material.
7. Turn on the collector and record the new P/Static Pressure.
8. Check for excessive motor/blower vibration.
9. Check overall system for any loose bolts or screws, and also door latches, hinge wear.
10. Wipe off any major hand prints off collector door, control panel that may have gotten there
while doing the service.
11. Clean up any fallen debris from the system service.
12. Observe the welding process when possible and determine if sparks are getting near
the inlet.
Notes:
Any single spark has the potential to cause a fire. Observation is always the best way to
determine if potential exists or if something has changed since the last service.
If the welding parameters change, (i.e. weld wire size, shielding gas mixture, new parts or
supplier) then we should verify spark containment away from the inlets.
Summary of Contents for PFX Series
Page 2: ......
Page 6: ......
Page 7: ...ROBOVENT PFX SERIES OWNER S MANUAL 7 SECTION 100 Important Safety Instructions ...
Page 9: ...SECTION 200 Features of the PFX Series Collector ...
Page 11: ...SECTION 300 Receiving Inspection ...
Page 13: ...SECTION 400 General Description ...
Page 15: ...SECTION 500 Specifications ...
Page 26: ...26 ROBOVENT PFX SERIES OWNER S MANUAL ...
Page 27: ...SECTION 600 Installation ...
Page 29: ...SECTION 700 Operation ...
Page 35: ...SECTION 900 VFD Maintenance Procedure ...
Page 38: ...38 ROBOVENT PFX SERIES OWNER S MANUAL ...
Page 39: ...ROBOVENT PFX SERIES OWNER S MANUAL 39 SECTION 1000 Motor Greasing Guide ...
Page 48: ...48 ROBOVENT PFX SERIES OWNER S MANUAL ...
Page 49: ...ROBOVENT PFX SERIES OWNER S MANUAL 49 SECTION 1100 Troubleshooting ...