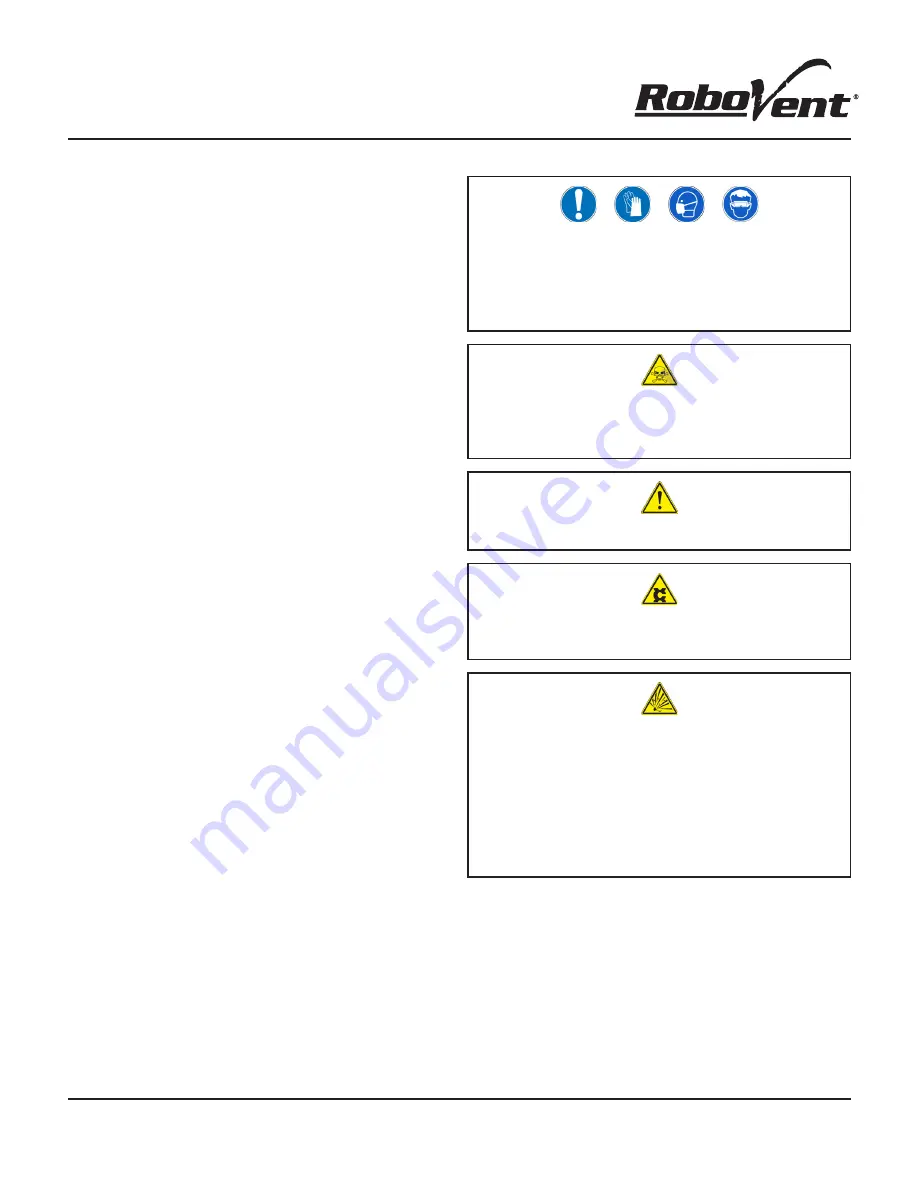
ProCube Owner's Manual & Operating Instructions
E2-20171010
©2017 ROBOVENT PRODUCT GROUP, INC.
4
Introduction
Whilst it can perform in ‘high-loading’ applications, such as robotic weld-
ing, plasma cutting, and grinding applications, these processes generate
more fume and particles than what is practical for the collection capacity
of the ProCube machine. Therefore, it is not recommended for use in such
applications.
Some welding conditions or atmospheres can generate oily or sticky
particulate that ‘blinds’ the filter media. Blinding occurs when the pores
in the fiber of the media become blocked so that pulse cleaning does not
remove the blockage, leading to diminished cleaning results, finally result-
ing in reduced filter life. If you notice decreased filter life, or if differential
pressure of the filter does not drop after an offline cleaning cycle, it may
indicate blinding. You can improve filter condition by welding clean mate-
rial, reducing the amount of oil on parts, and/or limiting use of anti-spatter
spray. Nozzle gel must not be used with fume extraction welding guns.
Metal particulate collected from welding or related processes can be
combustible when built-up in the collector, on the filter, or in hoses.
Combined with the presence of sparks in the incoming air stream, this
presents a potential fire risk. Typically, turbulence in the hose extinguishes
sparks; for additional protection, the machine is equipped with a Delta3
Spark Arrestor. Despite these features, it may be possible for a spark to
get through. Observe the process periodically to ensure intake of sparks
is not excessive. Often, the position of inlets can be adjusted to prevent a
consistent intake of sparks or settings on the process can be adjusted to
reduce sparks.
Follow all regulations applicable to your workplace and usage conditions.
RoboVent or a consultant in your area can assist with compliance
If the intake becomes obstructed, shut the machine down and fix the issue
to prevent overheating of the motor and blower. Overpressure is indicated
by the red band on the airflow gauge.
The blower motor is designed for continuous duty. Starting the motor more
than six times per hour, however, can decrease its life. When using the
AutoSaver function, it is possible for the number of starts to exceed this
count. The program delays shut-off for one minute after welding stops to
evacuate fumes from the hose and to allow for pauses between welds.
Pay attention to a typical production cycle: if there are breaks in welding
longer than one minute, keep track to make sure motor will not be required
to start more than six times per hour. If this frequency will be exceeded,
either switch the unit on before each period of welding, or leave the unit on
throughout the day.
Personal Protective Equipment (PPE) is required when servicing the
machine. Specific requirements are to be determined by applicable
regulations, dust toxicity testing and your workplace policies. As a
general rule, gloves, dust mask and safety goggles are recommended
to prevent exposure to or inhalation of dust.
Some dusts collected from welding and related processes can be
hazardous. The factory is responsible to test for toxicity and determin-
ing precautions for emptying and disposing hazardous waste.
The ProCube is not designed to filter gases, odors or noxious fumes.
This filtration machine is not approved for filtration of Carcinogenic,
Mutagenic, or Reproductively-harmful (CMR) substances.
The ProCube unit is not designed for use in explosive atmospheres,
potentially explosive atmospheres, or for extracting substances from
such atmospheres. Neither is it intended to process substance which
could create an explosive or potentially explosive atmosphere inside
the machine. If the dust to be extracted may create aforementioned
conditions, it must be sampled and tested for explosivity. Responsibility
lies with the factory to perform testing and ensure compliance with
NFPA guidelines.