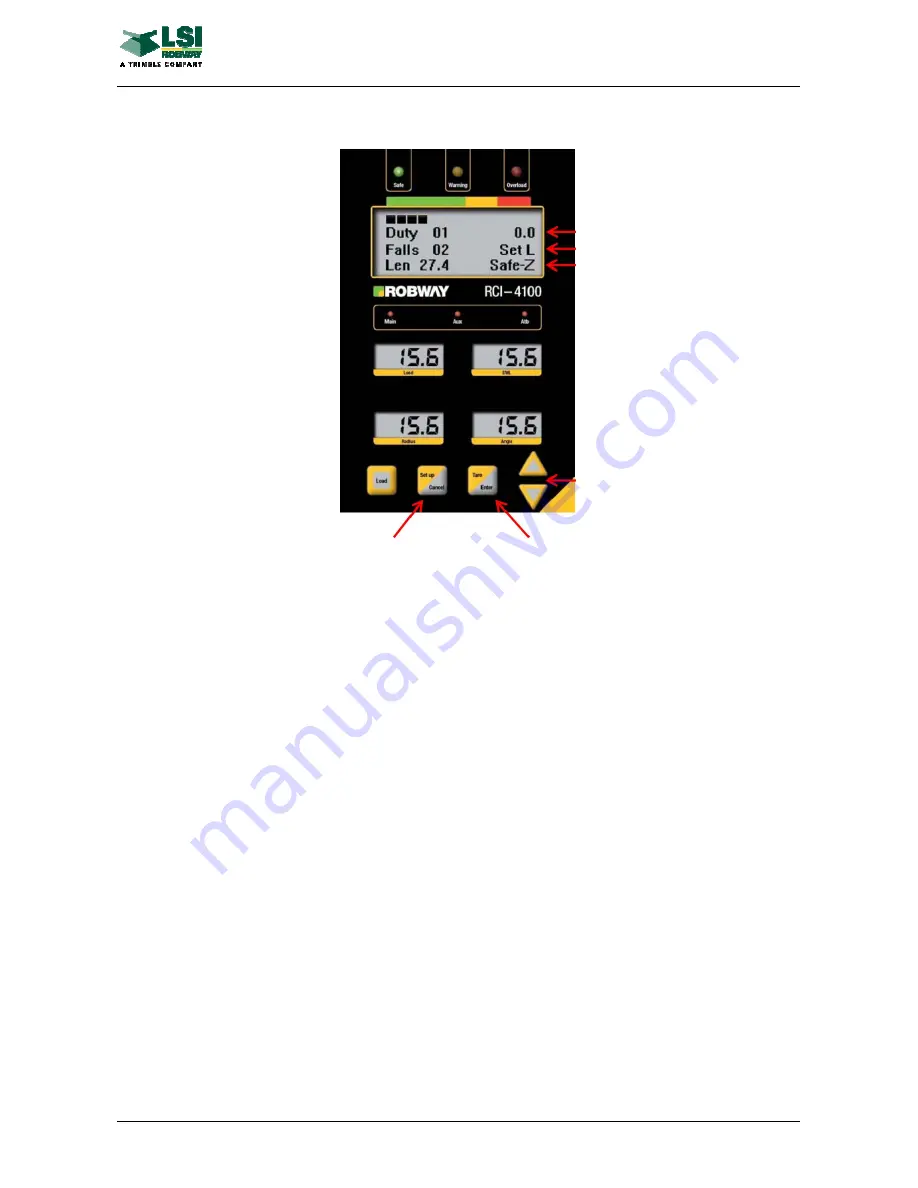
RESTRICTED SLEW ZONE MONITORING
MAN-1111 Rev H
©Copyright 2015 LSI-Robway Pty Ltd
Page 135
Checking Slew Angle
Slew angle is shown relative to the reset position (0 degree). Turning the superstructure to
the right (clockwise) increases the angle while turning it to the left (anti-clockwise) decreases
it. The full range is 0 to 360 degrees. The operator can see the current slew angle and RSZ
status of the machine by pressing the UP or DOWN arrow key for about 5 seconds while in
normal RCI mode. The alphanumeric screen will switch to RSZ view mode showing the
current slew angle and RSZ status.
Permanent and Temporary Zones
Two independent sets of zones are maintained. The permanent zone set can only be
accessed by authorised personnel who are equipped with the "over-ride" key. The temporary
set can be accessed and edited by the operator freely. The system will monitor both sets
continuously and will work out combined safety restrictions.
Press SETUP/CANCEL key to
return to RCI mode.
After selecting a menu item, press
the ENTER key to accept and
confirm the selection, or press the
CANCEL key to abort changes to
current selection.
Boom Slew Angle
Menu Items
RSZ Status
(Safe, Rest, No-Go)
Use the UP or DOWN arrow
key to select a menu item
(Set L, Set R, Lo Ang, Hi Ang,
Delete, ClrAll, Split, Unite L,
Unite R)
Summary of Contents for RCI-4100
Page 2: ......
Page 6: ......
Page 8: ......
Page 28: ......
Page 36: ......
Page 58: ......
Page 70: ......
Page 82: ......
Page 88: ......
Page 92: ......
Page 94: ......
Page 100: ......
Page 102: ......
Page 104: ......
Page 106: ......
Page 108: ......
Page 110: ......
Page 112: ......
Page 114: ......
Page 126: ......
Page 128: ......
Page 130: ......
Page 132: ......
Page 140: ......
Page 142: ...WIND SPEED MONITORING OPTION MAN 1111 Rev H Copyright 2015 LSI Robway Pty Ltd Page 142 ...
Page 144: ......
Page 147: ...WIND DIRECTION MONITORING MAN 1111 Rev H Copyright 2015 LSI Robway Pty Ltd Page 147 ...
Page 148: ......
Page 150: ......
Page 156: ......
Page 158: ......
Page 162: ...TILT SENSING OPTION MAN 1111 Rev H Copyright 2015 LSI Robway Pty Ltd Page 162 ...
Page 164: ......
Page 170: ......
Page 171: ...SYSTEM DRAWINGS MAN 1111 Rev H Copyright 2015 LSI Robway Pty Ltd Page 171 ...
Page 172: ...SYSTEM DRAWINGS MAN 1111 Rev H Copyright 2015 LSI Robway Pty Ltd Page 172 ...
Page 173: ...SYSTEM DRAWINGS MAN 1111 Rev H Copyright 2015 LSI Robway Pty Ltd Page 173 ...
Page 174: ...SYSTEM DRAWINGS MAN 1111 Rev H Copyright 2015 LSI Robway Pty Ltd Page 174 ...
Page 175: ...SYSTEM DRAWINGS MAN 1111 Rev H Copyright 2015 LSI Robway Pty Ltd Page 175 ...
Page 176: ...SYSTEM DRAWINGS MAN 1111 Rev H Copyright 2015 LSI Robway Pty Ltd Page 176 ...
Page 177: ...SYSTEM DRAWINGS MAN 1111 Rev H Copyright 2015 LSI Robway Pty Ltd Page 177 ...
Page 178: ...SYSTEM DRAWINGS MAN 1111 Rev H Copyright 2015 LSI Robway Pty Ltd Page 178 ...
Page 179: ...SYSTEM DRAWINGS MAN 1111 Rev H Copyright 2015 LSI Robway Pty Ltd Page 179 ...
Page 180: ......
Page 182: ......