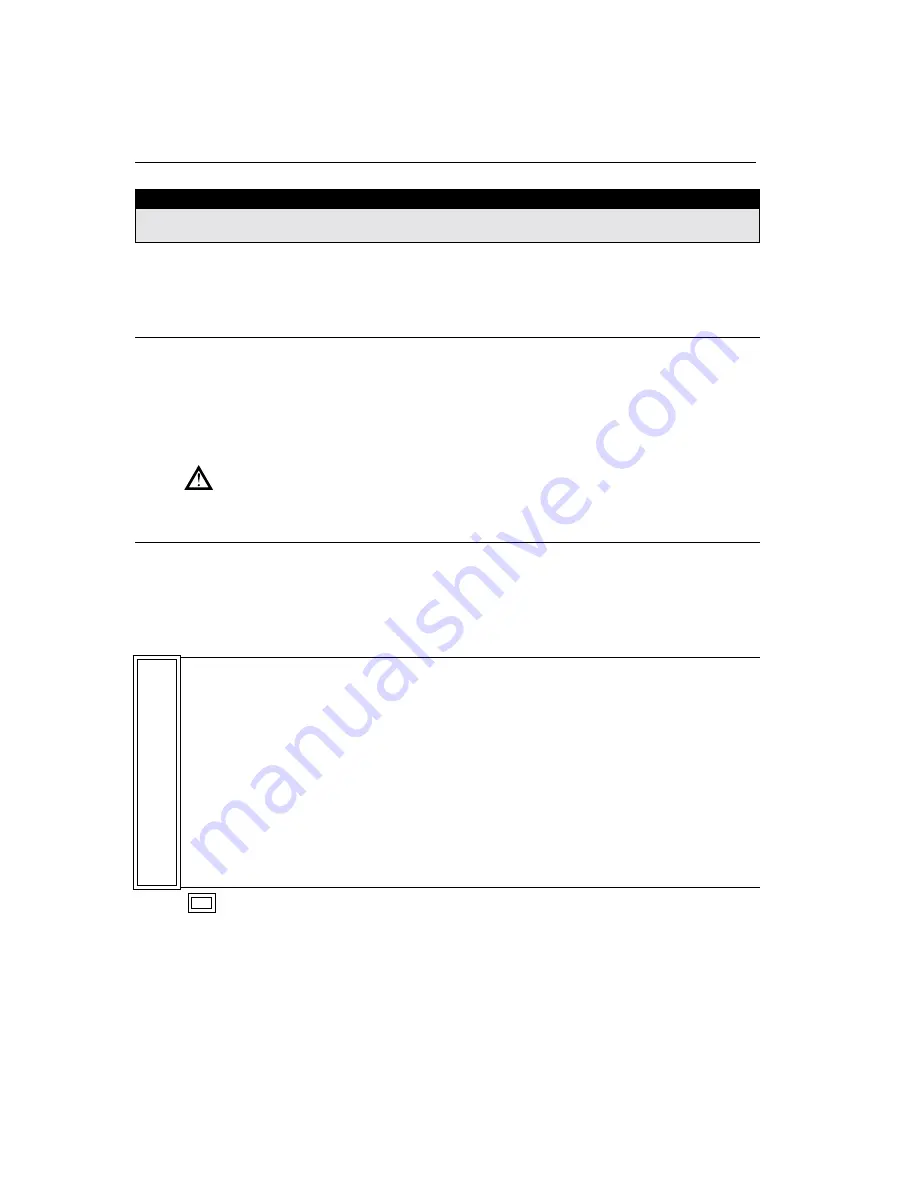
5-14
Parameters and Programming
71
[IR Compensation]
The programmed value adds a voltage to the output based on the torque current.
An additional 31 volts (150%) is added to 460 volt units to compensate for stator
resistance. 15.5 volts (150%) is added for 230 volt units. If the drive trips on an
F07 - Motor Overload fault, or has trouble accelerating to commanded speed,
this value should be reduced. A setting of 0% disables this function.
0/150
1%
50%
72
[Slip Compensation]
This parameter compensates for the inherent slip in an induction motor.
A frequency is added to the commanded output frequency based on torque
current. If motor shaft speed decreases significantly under heavy loads then this
value should be increased. A setting of 0.0 Hz disables the function. This
parameter along with P83 - [PI Process Reference] also activates PI control in
drives using Firmware Version FRN 7.06. See page 5-17 for PI Control Setup and
Activation instructions.
0.0/5.0
0.1 Hz
2.0 Hz
73
[Reverse Disable]
When this parameter is set to a 1, reverse is disabled. The reverse command
may come from the analog input, TB3-5, the keypad or a serial command. With
a negative analog input and reverse disabled, the frequency command will be
zero in bipolar mode and minimum frequency in unipolar mode. All digital reverse
inputs including two-wire Run Reverse will be ignored with reverse disabled.
Important:
This parameter cannot be programmed while the drive is running.
0/1
Numeric
value
0
74
[Analog Select]
Settings: 0 = unipolar analog input 0 to +10V
1 = bipolar analog input -10 to +10V
Important:
With this parameter set to bipolar (setting 1), the parameter settings
for P75 - [Analog Input Minimum] and P32 - [Minimum Frequency]
are ignored. In addition, all other reverse inputs (Program Keypad
Module, Remote Keypad Module, CopyCat Keypad Module, TB3-5
control terminal block, or serial communication module) are ignored
with the exception of when P46 - [Input Mode] is programmed to
setting 7. (This applies to drives with firmware version FRN 7.03 and
later.) When P46 - [Input Mode] setting 7 is active, and TB3-8 is
closed, the frequency source is P58 - [Internal Frequency] and the
direction will be commanded from the control terminal block (either
terminal TB3-5 or TB3-6).
Important:
This parameter cannot be programmed while the drive is running.
0/1
Numeric
value
0
Program Group
No.
Parameter Name/Description
Min./Max.
Range
Units
Factory
Default
ATTENTION:
Hazard of personal injury or equipment damage
exists due to unpredictable changes in motor speed. Do not use
P72 - [Slip Compensation]
and
P83 - [Process Reference]
to disable
PI control while the drive is running. Disable PI control only when
the drive is stopped.
This parameter applies only to the Analog Signal Follower model.
Summary of Contents for Allen-Bradley 160 SSC Series
Page 12: ...1 6 Getting Started End of Chapter ...
Page 58: ...5 20 Parameters and Programming End of Chapter ...
Page 66: ...A 4 Specifications End of Chapter ...
Page 75: ...Accessories and Dimensions B 9 Drilling Template A Figure B 10 ...
Page 76: ...B 10 Accessories and Dimensions Drilling Template B Figure B 11 ...
Page 82: ...C 6 CE Conformity End of Chapter ...
Page 87: ......