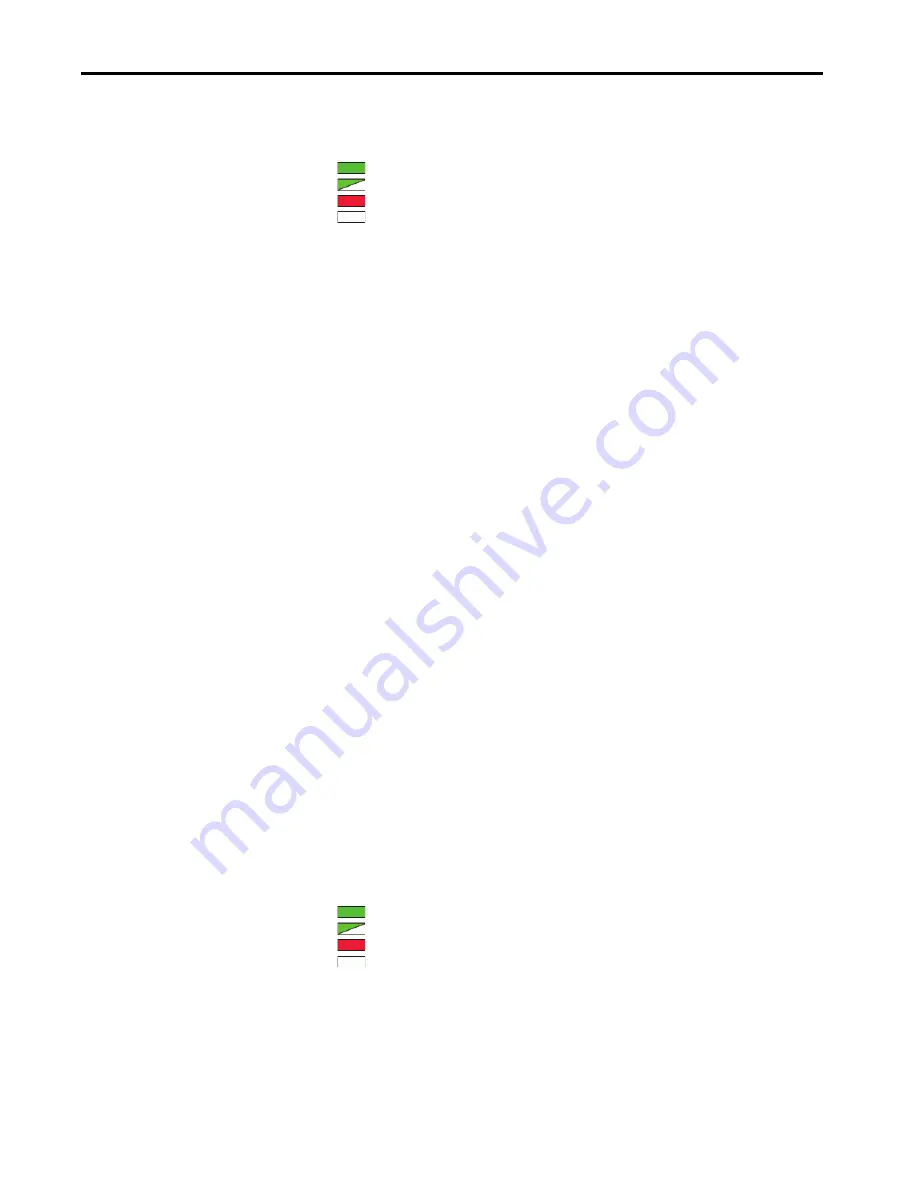
Rockwell Automation Publication 442G-UM001B-EN-P - May 2016
61
Troubleshooting and Assistance
Appendix A
DIA LED Illuminated and State LED Flashes Two Times (series
connection only)
Fault:
Input error
Possible causes:
• 24V DC missing at safety inputs Fl1A and/or Fl1B of the first Access
Box.
• FI1A is connected with FO1B or FI1B is connected with FO1A.
• Conventional safety components (switching contacts) are connected to
FI1A and/or FI1B.
• A safe control system with clocking outputs is connected.
• All connections are correct, but there is no common potential for the
series-connected devices (several power supply units for one chain).
• An upstream unit is set as a standalone device.
Remedy:
1. Check the wiring and correct it or switch off the clock pulses or check the
upstream devices for incorrect DIP switch configuration.
2. Switch off the voltage at all devices
or
press the reset button (if present) that controls ALL integrated reset inputs
in the series connection
3. Close the door(s).
4. Switch the voltage on again
or
release the reset button
5. Wait until the State LED flashes at regular intervals.
The Access Box is now ready for operation again.
DIA LED Illuminated and State LED Flashes Three Times
Fault:
Handle assembly read error (e.g. error in code/code not readable).
Possible causes:
• EMC interference, e.g. caused by clocked cables near the Access Box.
• Hardware fault in the handle assembly
Power
State 2 x flash
DIA
Lock
Power
State 3 x flash
DIA
Lock