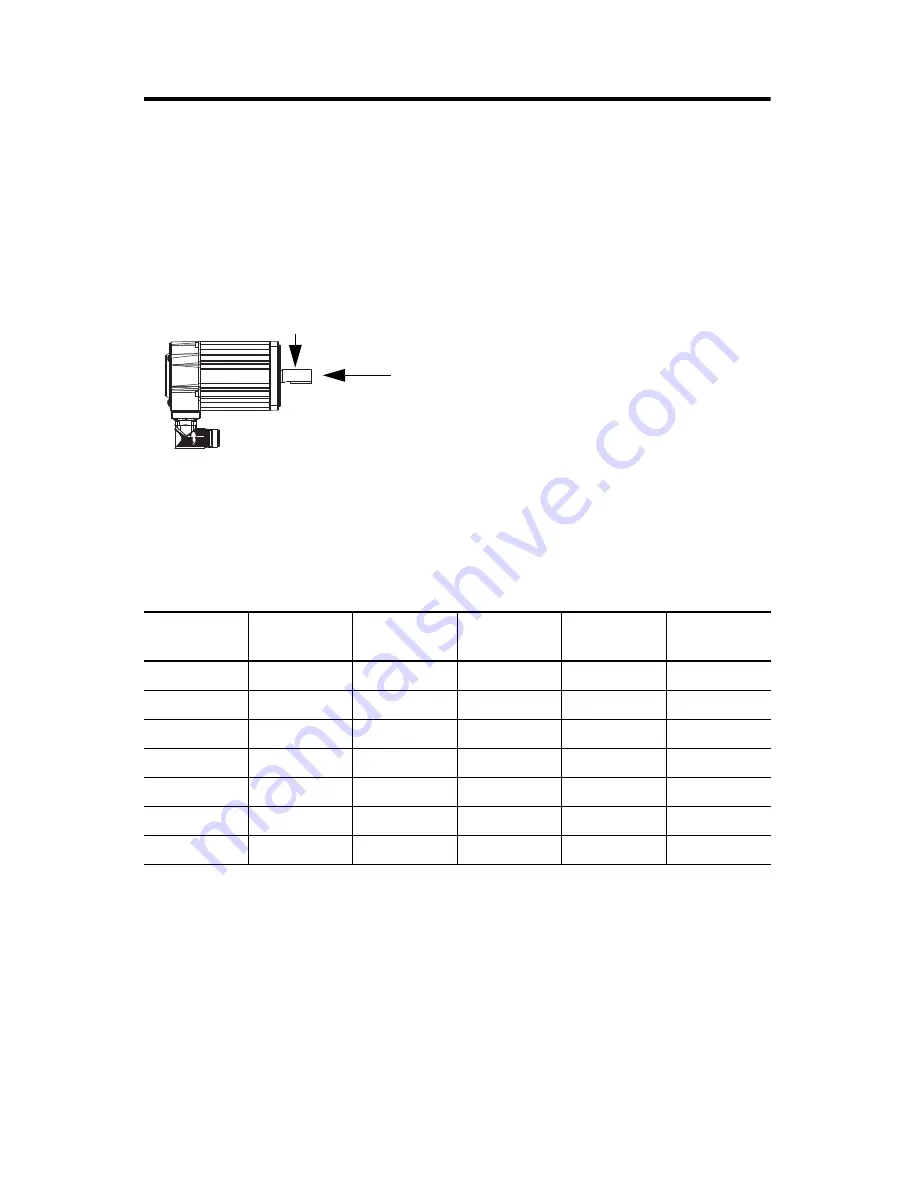
20
MP-Series Low Inertia Servo Motor Installation Instructions
Publication MP-IN002C-EN-P - April 2009
Motor Load Force Ratings
Motors are capable of operating with a sustained shaft load. The load force
locations are shown in the figure and maximum values are in the tables.
Loads are measured in kilograms; pounds are mathematical conversions.
Load Forces on Shaft
The following tables represent 20,000 hour L
10
bearing fatigue life at various loads
and speeds. This 20,000 hour life does not account for possible application-specific
life reduction that can occur due to bearing grease contamination from external
sources.
Radial Load Force Ratings
Motor
500 rpm
kg (lb)
1000 rpm
kg (lb)
1500 rpm
kg (lb)
2000 rpm
kg (lb)
3000 rpm
kg (lb)
MPL-B640
253 (557)
200 (442)
—
159 (351)
139 (307)
MPL-B660
275 (607)
219 (482)
—
173 (382)
151 (334)
MPL-B680
291 (641)
230 (508)
—
183 (404)
160 (353)
MPL-B860
347 (764)
275 (607
—
219 (481)
—
MPL-B880
367 (810)
292 (643
—
231 (510)
—
MPL-B960
466 (1028)
370 (816)
323 (713)
—
—
MPL-B980
494 (1089)
392 (864)
352 (775)
—
—
Axial Load Force
Radial load force applied at center of shaft extension.