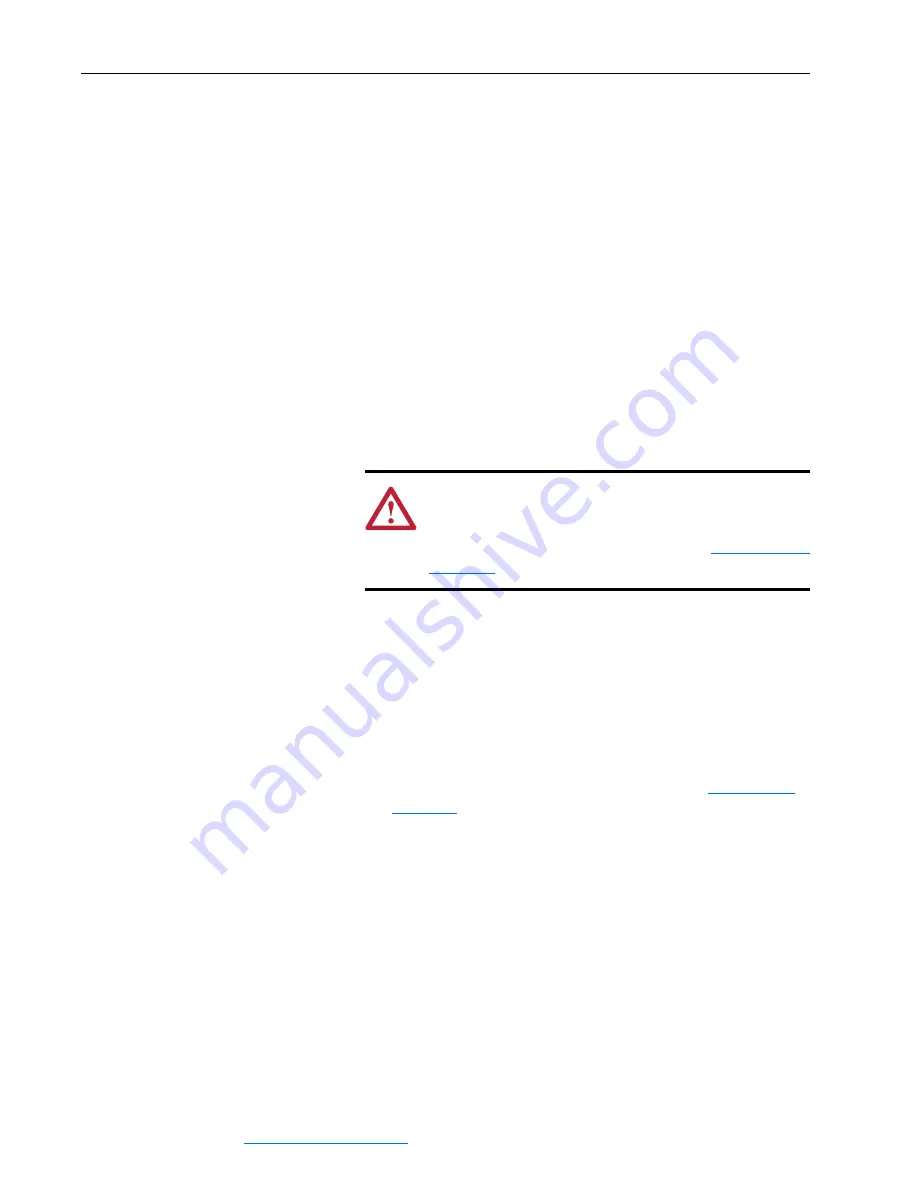
PowerFlex Digital DC Drive User Manual -
Publication 20P-UM001C-EN-P - July 2008
2-14
Drive Start Up
10. Configure the Speed Feedback Parameters:
1. Access the “Speed Feedback” group and configure the following
parameters:
❏
Par 414 [Fdbk Device Type] - Select the source for motor
velocity feedback: 1 “Encoder”, 2 “DC Tach” or 3 “Armature”
(default). If operating the drive in field weakening mode, Par
414 [Fdbk Device Type] must be set to 1 "Encoder" or 2 "DC
Tach".
❏
Par 457 [Spd Fdbk Control] - If you are using an encoder or
tachometer, set this parameter to 1 “Enabled” to activate speed
feedback control.
❏
If the speed feedback source is an analog tachometer, set the
fine scaling value in Par 562 [Anlg Tach Gain]. This value is
used to scale the analog tachometer feedback signal after it has
been conditioned by the drive hardware.
❏
If the speed feedback source is a digital encoder, enter the
pulses per revolution from the encoder nameplate in Par 169
[Encoder PPR].
❏
If the speed feedback source is a digital encoder, set Par 652
[Encoder Err Chk] to 1 “Enabled” to activate monitoring of the
digital encoder signals (verifies the presence of the A, B, A-, B-
signals). Par 457 [Spd Fdbk Control] must be set to 1
“Enabled” for encoder monitoring to occur. Switch S20 must be
set correctly to prevent Encoder faults. Refer to
2. Access the “Speed Command” file and press Enter.
3. With the “Limits” group selected, press Enter and configure the
following parameters:
❏
Par 1 [Minimum Speed] - Enter the minimum speed reference
limit.
❏
Par 2 [Maximum Speed] - Enter the maximum speed required
by the application (this can be above the motor base speed if
field weakening is used).
!
ATTENTION: The drive can overspeed if DIP switch
S4 is set incorrectly, or the tach is wired incorrectly.
Failure to observe this precaution could result in damage
to the drive or process equipment. Refer to