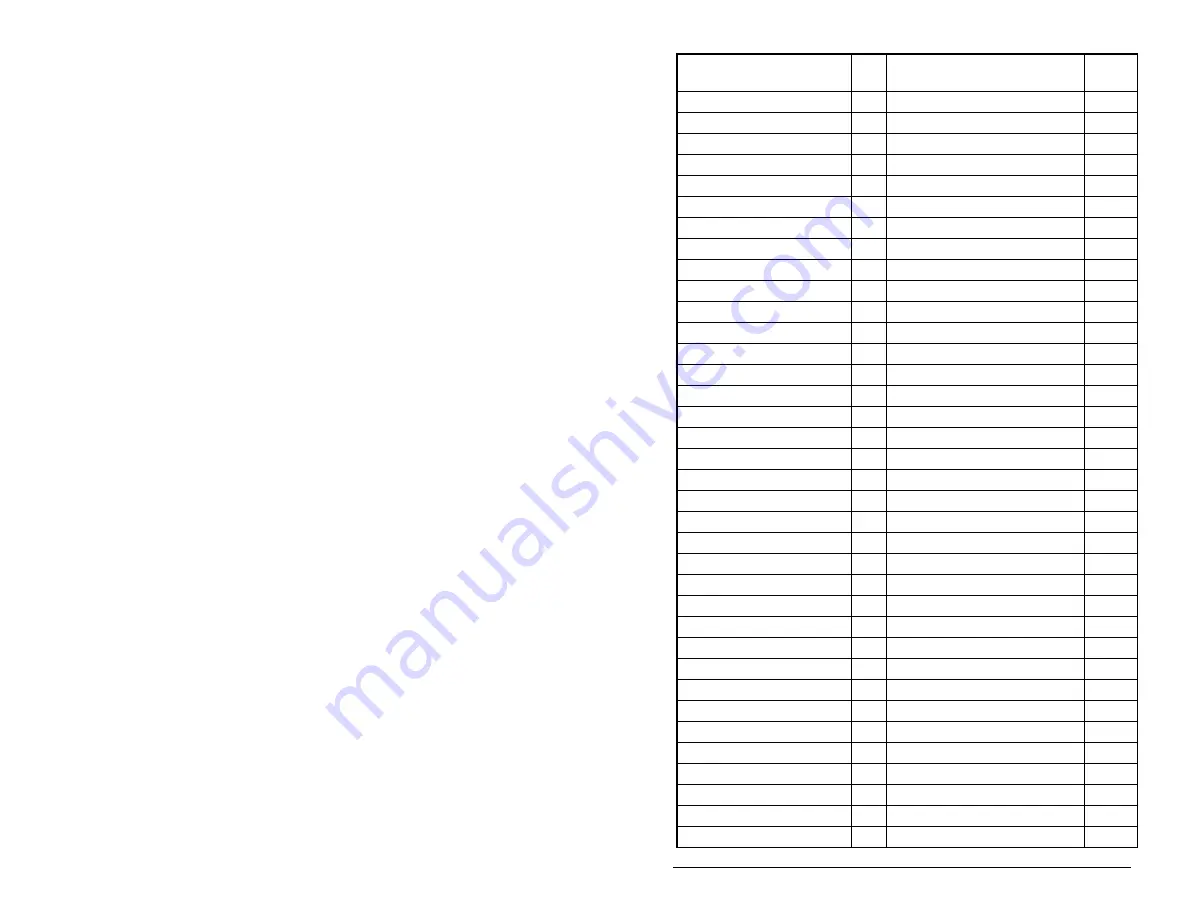
Parameters Cross-Referenced by Name
B-5
Motor Type
40 Motor Control>Motor Data
12-8
Mtr NP Pwr Units
46 Motor Control>Motor Data
12-10
Output Current
3 Monitor>Metering
12-5
Output Freq
1 Monitor>Metering
12-5
Output Power
7 Monitor>Metering
12-6
Output Powr Fctr
8 Monitor>Metering
12-6
Output Voltage
6 Monitor>Metering
12-6
Overspeed Limit
83 Speed Command>Spd Mode & Limits
12-19
Param Access Lvl
196 Utility>Drive Memory
12-56
PI Configuration
124 Speed Command>Process PI
12-30
PI Control
125 Speed Command>Process PI
12-31
PI Error Meter
137 Speed Command>Process PI
12-37
PI Fdback Meter
136 Speed Command>Process PI
12-37
PI Feedback Sel
128 Speed Command>Process PI
12-34
PI Integral Time
129 Speed Command>Process PI
12-34
PI Lower Limit
131 Speed Command>Process PI
12-35
PI Output Meter
138 Speed Command>Process PI
12-37
PI Preload
133 Speed Command>Process PI
12-35
PI Prop Gain
130 Speed Command>Process PI
12-34
PI Ref Meter
135 Speed Command>Process PI
12-36
PI Reference Sel
126 Speed Command>Process PI
12-33
PI Setpoint
127 Speed Command>Process PI
12-33
PI Status
134 Speed Command>Process PI
12-36
PI Upper Limit
132 Speed Command>Process PI
12-35
Power Loss Mode
184 Dynamic Control>Stop/Power Loss
12-52
Power Loss Time
185 Dynamic Control>Stop/Power Loss
12-52
Power Up Marker
242 Utility>Faults
12-72
Preset Speed 1
101 Speed Command>Discrete Speeds
12-26
Preset Speed 2
102 Speed Command>Discrete Speeds
12-26
Preset Speed 3
103 Speed Command>Discrete Speeds
12-26
Preset Speed 4
104 Speed Command>Discrete Speeds
12-26
Preset Speed 5
105 Speed Command>Discrete Speeds
12-26
Preset Speed 6
106 Speed Command>Discrete Speeds
12-26
Preset Speed 7
107 Speed Command>Discrete Speeds
12-26
Rated Amps
28 Monitor>Drive Data
12-8
Rated kW
26 Monitor>Drive Data
12-8
Parameter Name
No.
Path (File>Group)
Page
No.
Summary of Contents for Reliance electric 6SP201-015
Page 14: ...1 2 SP600 AC Drive User Manual ...
Page 54: ...Mounting the Drive 3 16 ...
Page 82: ...6 12 SP600 AC Drive User Manual ...
Page 96: ...7 14 SP600 AC Drive User Manual ...
Page 232: ...Parameter Descriptions 12 102 ...
Page 280: ...B 8 SP600 AC Drive User Manual ...
Page 282: ...C 2 SP600 AC Drive User Manual ...
Page 284: ...D 2 SP600 AC Drive User Manual ...
Page 298: ......
Page 299: ......