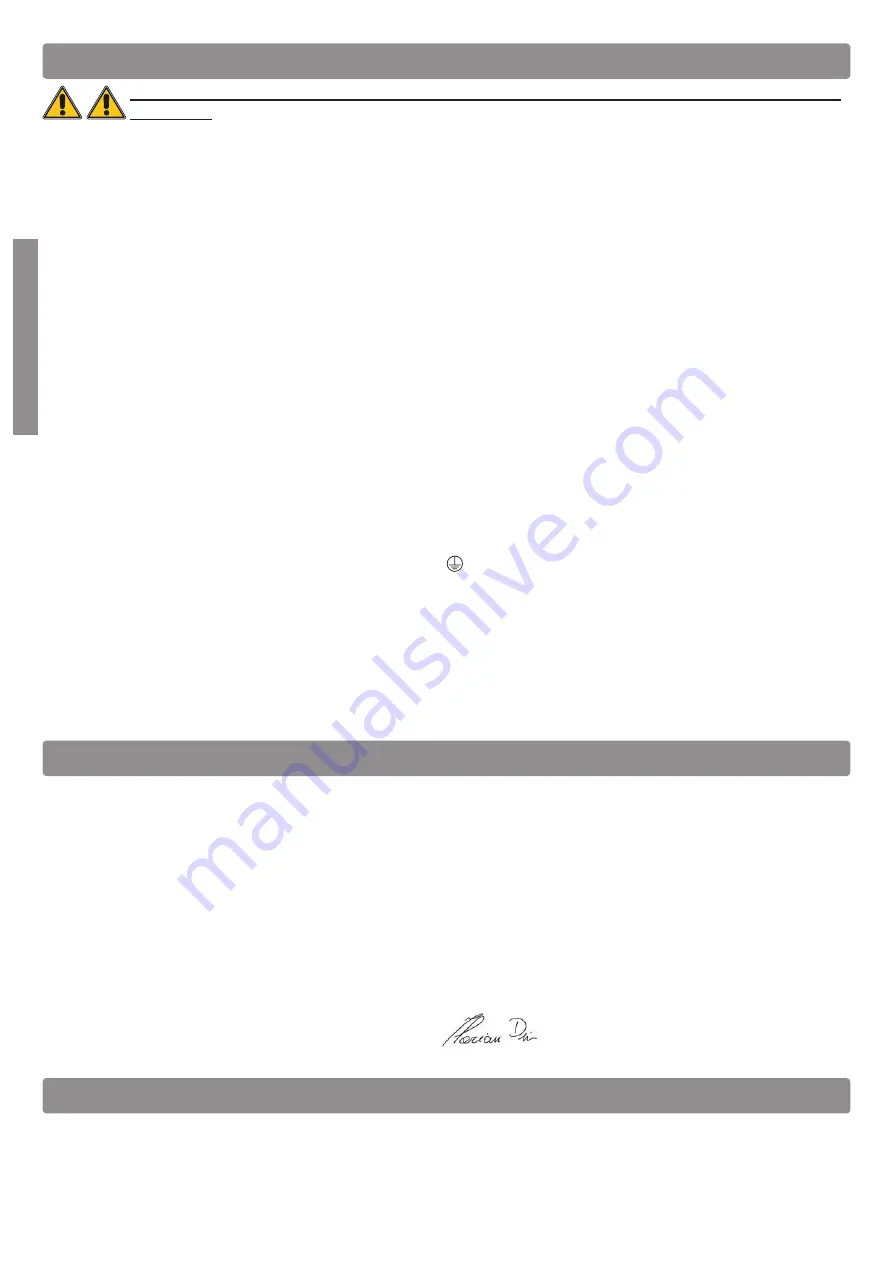
16
EN
16
1
GENERAL SAFETY PRECAUTIONS
Failure to respect the information given in this manual may cause personal injury or damage to
the device.
This installation manual is intended for qualified personnel only.
ROGER TECHNOLOGY cannot be held responsible for any damage or injury due to improper use or any use other the intended usage indicated in this
manual.
Installation, electrical connections and adjustments must be performed by qualified personnel, in accordance with best practices and in compliance
with applicable regulations.
Read the instructions carefully before installing the product. Bad installation could be dangerous.
Before installing the product, make sure it is in perfect condition:
if in doubt, do not use the equipment and contact qualified personnel only.
Do not install the product in explosive areas and atmospheres: the presence of inflammable gas or fumes represents a serious safety hazard.
Before installing the motorisation device, make all the necessary structural modifications to create safety clearance and to guard or isolate all the
crushing, shearing, trapping and general hazardous areas.
Make sure the existing structure is up to standard in terms of strength and stability.
ROGER TECHNOLOGY is not responsible for failure to observe Good Working Methods when building the frames to be motorised, or for any
deformation during use.
The safety devices (photocells, safety edges, emergency stops, etc.) must be installed taking into account: applicable laws and directives, Good
Working Methods, installation premises, system operating logic and the forces developed by the motorised door or gate.
The safety devices must protect against crushing, cutting, trapping and general danger areas of the motorised door or gate.
The European standards EN 12453 and EN 12445 define the minimum safety requirements for the operation of automatic doors and gates. In
particular, these standards require the use of force limiting and safety devices (sensing ground plates, photocell barriers, operator detection function
etc.) intended to detect persons or objects in the operating area and prevent collisions in all circumstances.
Where the safety of the installation is based on an impact force limiting system, it is necessary to verify that the characteristics and performance of
the automation system are compliant with the requisites of applicable standards and legislation.
The installer is required to measure impact forces and programme the control unit with appropriate speed and torque values to ensure that the door
or gate remains within the limits defined by the standards EN 12453 and EN 12445.
ROGER TECHNOLOGY declines all responsibility if component parts not compatible with safe and correct operation are fitted.
Display the signs required by law to identify hazardous areas.
Each installation must bear a visible indication of the data identifying the motorised door or gate.
An omnipolar disconnection switch with a contact opening distance of at least 3mm must be fitted on the mains supply.
Make sure that upline from the mains power supply there is a residual current circuit breaker that trips at no more than 0.03A and overcurrent cutout
upstream of the electrical system in accordance with best practices and in compliance with applicable regulations.
When requested, connect the automation to an effective earthing system
that complies with current safety standards.
During installation, maintenance and repair operations, cut off the power supply before opening the cover to access the electrical parts.
The electronic parts must be handled using earthed antistatic conductive arms.
Only use original spare parts for repairing or replacing products.
The installer must supply all information concerning the automatic, manual and emergency operation of the motorised door or gate, and must
provide the user with the operating instructions.
The packaging materials (plastic, polystyrene, etc.) should not be discarded in the environment or left within reach of children, as they are a potential
source of danger.
Dispose of and recycle the packing components in accordance with the standards in force.
These instruction must be kept and forwarded to all possible future user of the system.
2
DECLARATION OF CONFORMITY
I the undersigned, as acting legal representative of the manufacturer:
Roger Technology - Via Botticelli 8, 31021 Bonisiolo di Mogliano V.to (TV)
hereby DECLARE that the appliance described hereafter:
Description: Automatic barrier
Model
: BIONIK serie
Is conformant with the legal requisites of the following directives:
• Directive
2006/42/EC
(Machinery Directive)
and subsequent amendments
;
• Directive
2014/35/EU
(Low Voltage Directive)
and subsequent amendments
;
• Directive
2011/65/EC
(RoHS Directive)
and subsequent amendments
;
• Directive
89/106/CEE
CPD Directive)
and subsequent amendments
;
and that all the standards and/or technical requirements indicated as follows have been applied:
EN 61000-6-3
EN 61000-6-2
EN 13241-1
Last two figures of year in which marking was applied
|
17.
Place
: Mogliano V.to Date: 21-04-2017 Signature
3
INTENDED USE
The BIONIK automated barrier is specifically conceived for installations in private or public car parks, in residential, commercial or industrial areas or
in high traffic zones.
This product may only be used for its expressly intended purpose. Any other usage is prohibited.
ROGER TECHNOLOGY cannot be held directly or indirectly responsible for any damage resulting from incorrect, inappropriate or unreasonable usage
of this product.
Summary of Contents for BI/004
Page 1: ......