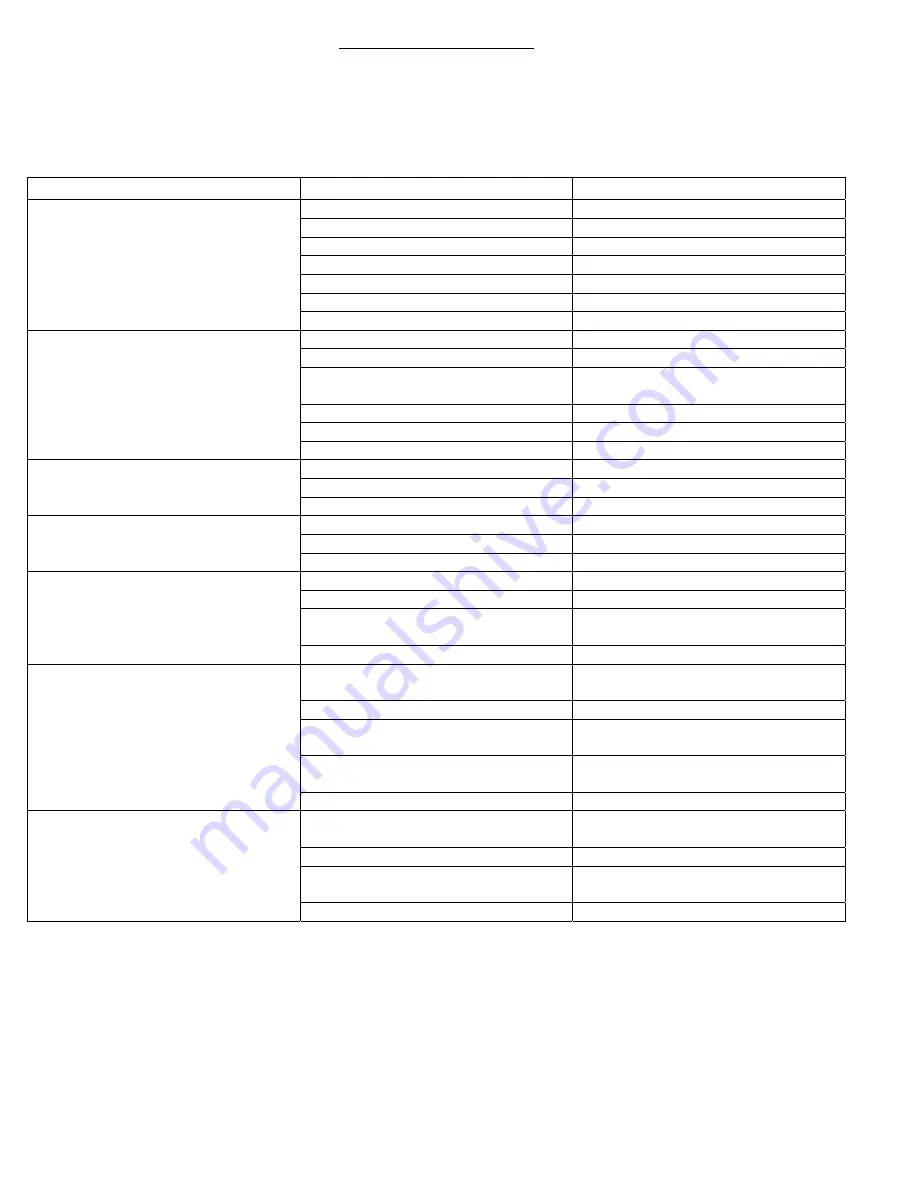
- 12 -
TROUBLESHOOTING
WARNING
-
Make sure you completely understand all of the safety warnings and operation of each system
control component before attempting any maintenance or repair. Always drain the tank pressure completely, make
sure the power cord is unplugged, and unit has time to cool before performing any maintenance or service
operations.
PROBLEM
CAUSE
SOLUTION
Pump is slow to build tank pressure
Loose/slipping belt
Adjust belt tension
Excessive leaks in system
Correct air leaks
Blown gasket
Replace head gaskets
Broken reed valve
Replace reed valves
Obstructed intake filter
Clean or replace intake element
Leaking regulator
Replace regulator
Defective pilot valve
Replace pilot valve
Excessive oil consumption
Too much oil in crankcase
Drain to proper level
Improper weight of oil
Replace with proper oil
Obstructed crankcase vent
Replace dipstick or oil fill
plug/crankcase vent
Dirty/plugged intake filter
Clean/replace intake filter
Worn piston rings
Take unit in for service
Scored cylinder
Take unit in for service
Knocking noise
Loose pulley or flywheel
Tighten appropriate parts
Loose belts
Adjust belt tension
Internal pump problem
Take unit in for service
Overheating compressor
Poor ventilation
Relocate compressor
Improper pump rotation
Contact an electrician
Internal pump problem
Take unit in for service
Electric motor dead,
will not even hum
Thermal overload tripped
Locate and push reset button
Reset physically broken
Replace overload/reset
Loose motor leads or electrical
connection
Locate and correct loose electrical
connection(s)
Short in power cord
Replace power cord
Motor trips overload/reset button
Motor is starting/stopping
excessively
Install constant speed or dual control
kit
Overload is defective/weak
Replace overload
Improper gauge of extension cord
Use longer lengths of air hose or
heavier cord
Stripped or poorly tightened motor
thru bolts
Retighten or replace stripped thru
bolts
Cracks in end bell or housing
Take unit in for service
Gasoline engine is hard to start
Fouled, incorrect, or improperly
gapped spark plug
Install proper spark plug after
gapping to factory specs
Improper engine oil level
Fill to top of threads for oil plug
Improper weight of pump or engine
oil
Change to proper weight of oil for
operating temperature
Improper or old gas
Take unit in for service