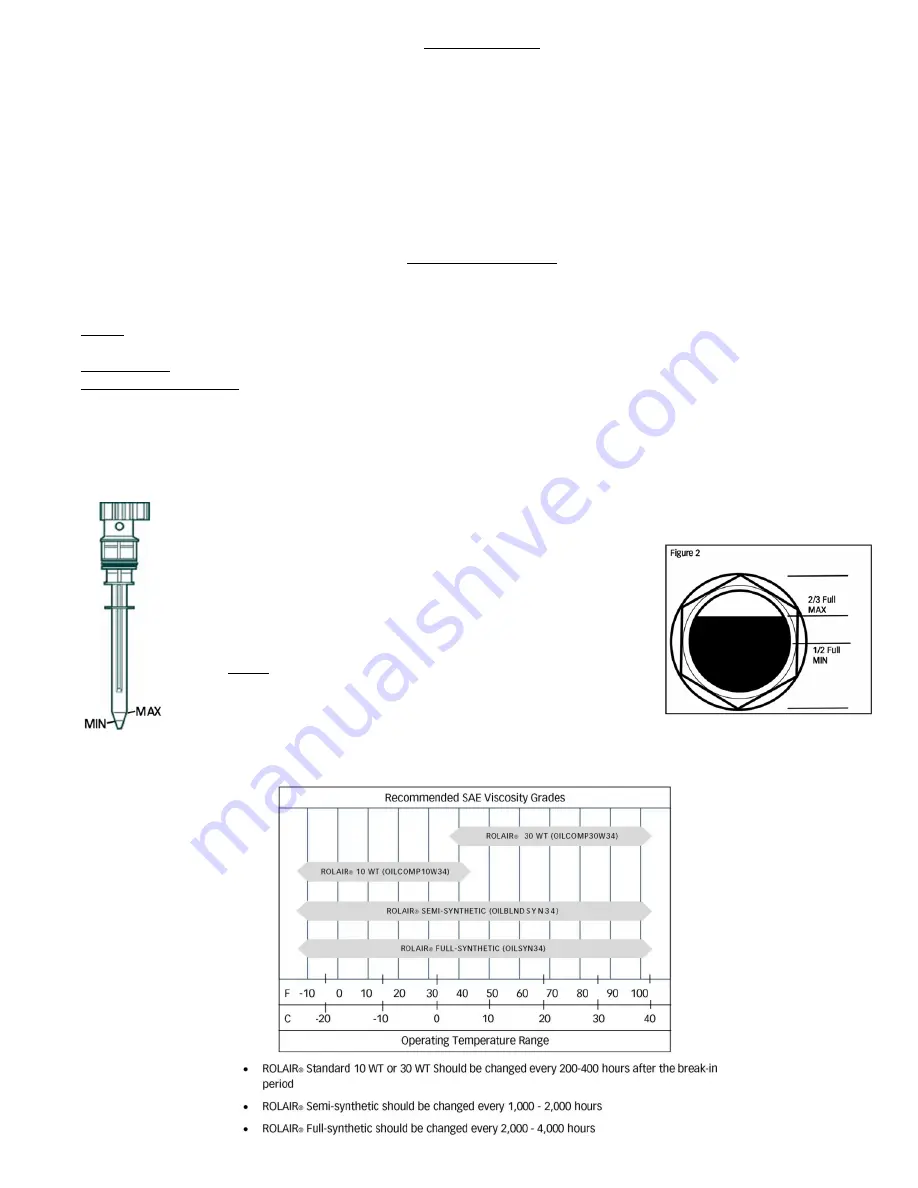
- 9 -
OPERATION
(con’t.)
High Altitude Operation:
Due to a decrease in atmospheric pressure air compressor pumps produce less CFM at higher elevations. As
a rule of thumb the output will decrease approximately three percent per 1000 feet of elevation. Also, because air at
higher elevations is less dense and does not cool as well, electric motors cannot be subjected to the full nameplate
service factor amp rating and may need to be upgraded to avoid repeated overheating.
Direct drive or hand-carry compressors built with cold-start valves may need to be modified when operated
in higher elevations. Carburetors on gas-powered air compressors may also need to be rejetted to perform properly
at higher elevations. Contact our factory Customer Service Department if your normally reliable air compressor fails
to operate correctly at higher elevations.
MAINTENANCE
Your new air compressor represents the finest engineering and construction available. Even the best
machinery requires periodic maintenance. Please stick to the maintenance schedule and consider the suggestions
that follow to keep your compressor in peak condition.
NOTE: Always unplug or shut down your compressor and drain the air tanks completely before attempting any
type of maintenance. Wait for compressor to cool before servicing.
IMPORTANT: Replace the oil after the first 50 hours of operation.
MAINTENANCE HINTS:
1) Use a soap/water solution to check for air leaks.
2) Never clean filters with a flammable solvent.
3) Retorque head bolts only after pump has cooled.
4) Move motor 1/4" and roll belts back on to increase
belt tension on electric units.
5) Never weld on air tank(s).
6) Use heat to loosen Loctite seal on drain valves, engine
pulleys, and flywheels before attempting to remove.
OIL CHART
LUBRICATION
Prior to each use, make a habit of checking the pump oil level. Most
direct-drive air compressors have a dipstick with casting marks that indicate
the minimum and maximum acceptable levels of oil. Our belt-driven pumps
have a sight gauge, located on the outside of the crankcase, to make the task
even easier. Always maintain the oil level at the maximum mark on the
dipstick or to 2/3 full in the sight gauge
Do not operate the pump with an inadequate or excessive amount of
oil. The cost of failures which occur due to incorrect oil levels will not be
covered under warranty.
DO NOT USE A DETERGENT OIL!
NOTE: Unit must be level when in operation