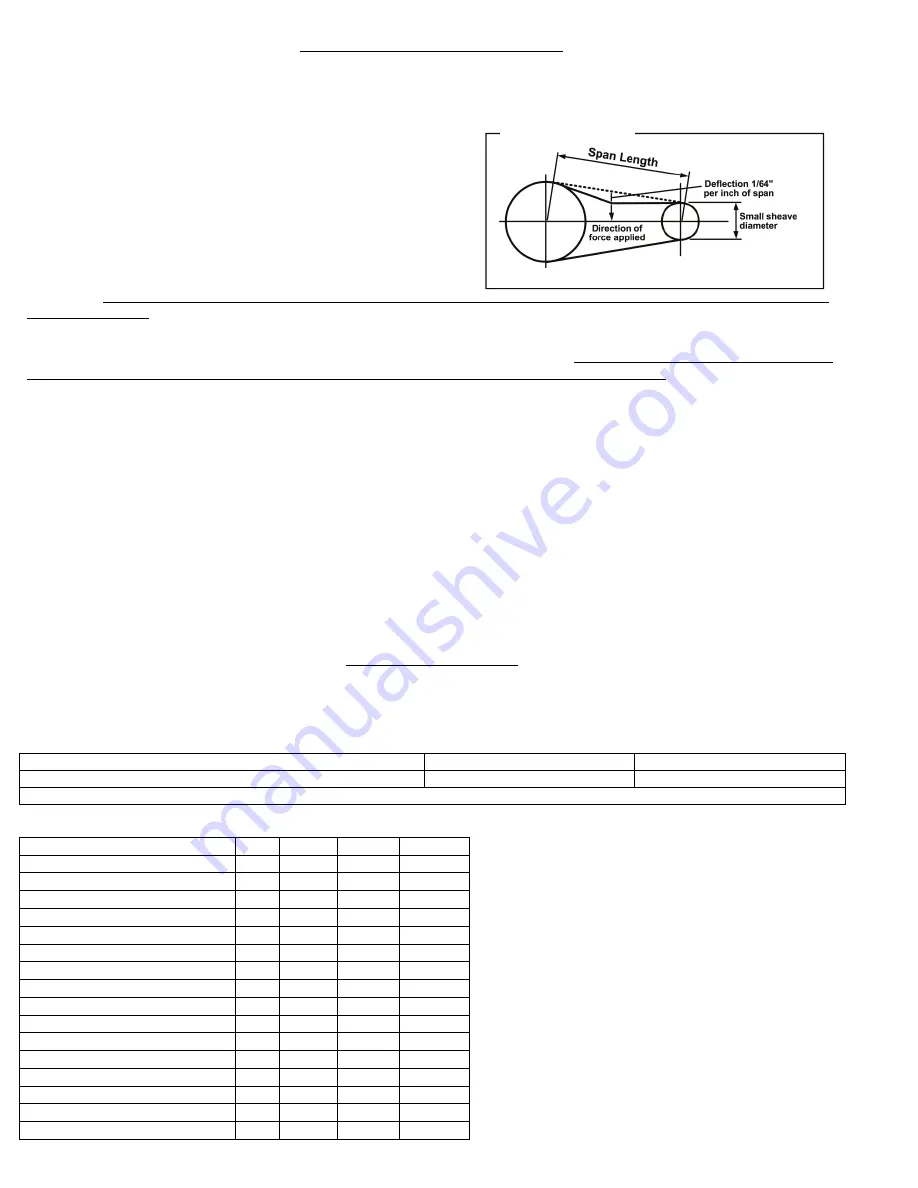
SYSTEM COMPONENTS
E
fficiency and safety are the primary concerns when selecting components for compressed air systems. Products of inferior quality
can not only hinder the performance of the unit, but could cause system failures or bodily harm. Select only top quality components
for your system. Call your local ROLAIR distributor for quality parts and professional advice.
DRIVE PULLEYS: Drive pulleys must be properly aligned and drive-belt
tension set to specifications. Improper pulley alignment and belt tension
can cause motor overloading, excessive vibration and premature belt
and/or bearing failure.
GUARDS: All mechanical action or motion is hazardous in varying
degrees and needs to be guarded. Guards should be designed to
achieve the required degree of protection and still allow full air flow
from the compressor flywheel across the unit. Guards shall be in
compliance with O.S.H.A. safety and health standards and any state or
local codes. When the compressor is installed, make sure guard side is at least 18” away from the wall to provide adequate cooling
of motor and pump.
CHECK VALVES: Check valves are designed to prevent back-flow of air pressure in the compressed air system (air flows freely in
one direction only.) The check valve must be properly sized for air flow and temperature. Do not rely upon a check valve to isolate a
compressor from a pressurized tank or compressed air delivery system during maintenance procedures!
MANUAL SHUT-OFF VALVES: Manual shut-off valves block the flow of air pressure in either direction. This type of valve can be
used to isolate a compressor from a pressurized system, provided the system is equipped with a safety-relief valve capable of being
manually released. The safety-relief valve should be installed between the manual shut-off valve and the compressor.
SAFETY-RELIEF VALVES: Safety-relief valves aid in preventing system failures by relieving system pressure when compressed air
reaches a determined level. A check valve and safety relief valve are required in all compressed air systems. Safety-relief valves are
pre-set by the manufacturer and under no circumstances should the setting be changed.
PRESSURE SWITCHES: The pressure switch detects the demand for compressed air and allows the motor to start. When the
demand is satisfied, the unit stops and unloads the head pressure with a short hissing noise. Engine-driven units use a pilot valve
instead of a pressure switch. It will discharge compressed air to atmosphere or open the intake valve upon reaching a
predetermined pressure setting.
PRESSURE VESSELS: ASME coded pressure vessels must not be modified, welded, repaired, reworked or subjected to operating
conditions outside the nameplate ratings. Such actions will negate code status.
MAINTENANCE
Regular maintenance insures trouble-free operation. Your new compressor represents the finest engineering and construction
available. However, even the finest machinery requires periodic maintenance. A good maintenance program will add years of
service to your air compressor. The following is recommended as a minimum maintenance program. For your protection,
disconnect power supply after each day’s operation and drain air from system before performing any maintenance.
OIL TABLE
Temperature
0-40°
40° & Above
NON-DETERGENT – Straight Weight
10WT*
30WT*
*For maximum performance and service life, we recommend using ROLAIR Premium Quality compressor oil.
*Check and re-torque (see chart on pg. 7) only after
pump has completely cooled to room temperature.
**Always make sure crankcase vent (breather) is free
and unobstructed when changing or checking oil.
MAINTENANCE HINTS:
1) Use a soap/water solution to check for air leaks.
2) Never clean filters with a flammable solvent.
3) Re-torque head bolts only after pump has cooled.
4) Move motor 1/4" and roll belts back on to increase belt
tension on electric units.
5) Never weld on air tank(s).
6) Use heat to loosen Loctite seal on drain valves, engine
pulleys and flywheels before attempting to remove.
Recommendation
Daily Weekly Monthly Quarterly
Check Oil Level
X
Drain Moisture from Tank(s)
X
Inspect Air Filter(s)
X
Check for Unusual Noise or Vibration
X
Inspect Belt Guard
X
Check for Air or Oil Leaks
X
Clean Exterior of Air Compressor
X
Check Condition of Vibration Pads
X
Tighten/Re-torque Bolts*
X
Check Belt Tension
X
Check Operation of Safety Valve
X
Change Compressor Oil**
X
Clean/Change Air Filter
X
Perform Pump Up Time Test
X
Check Operation of System Controls
X
Check Air Tanks for Dents/Leaks
X
DRIVE PULLEY