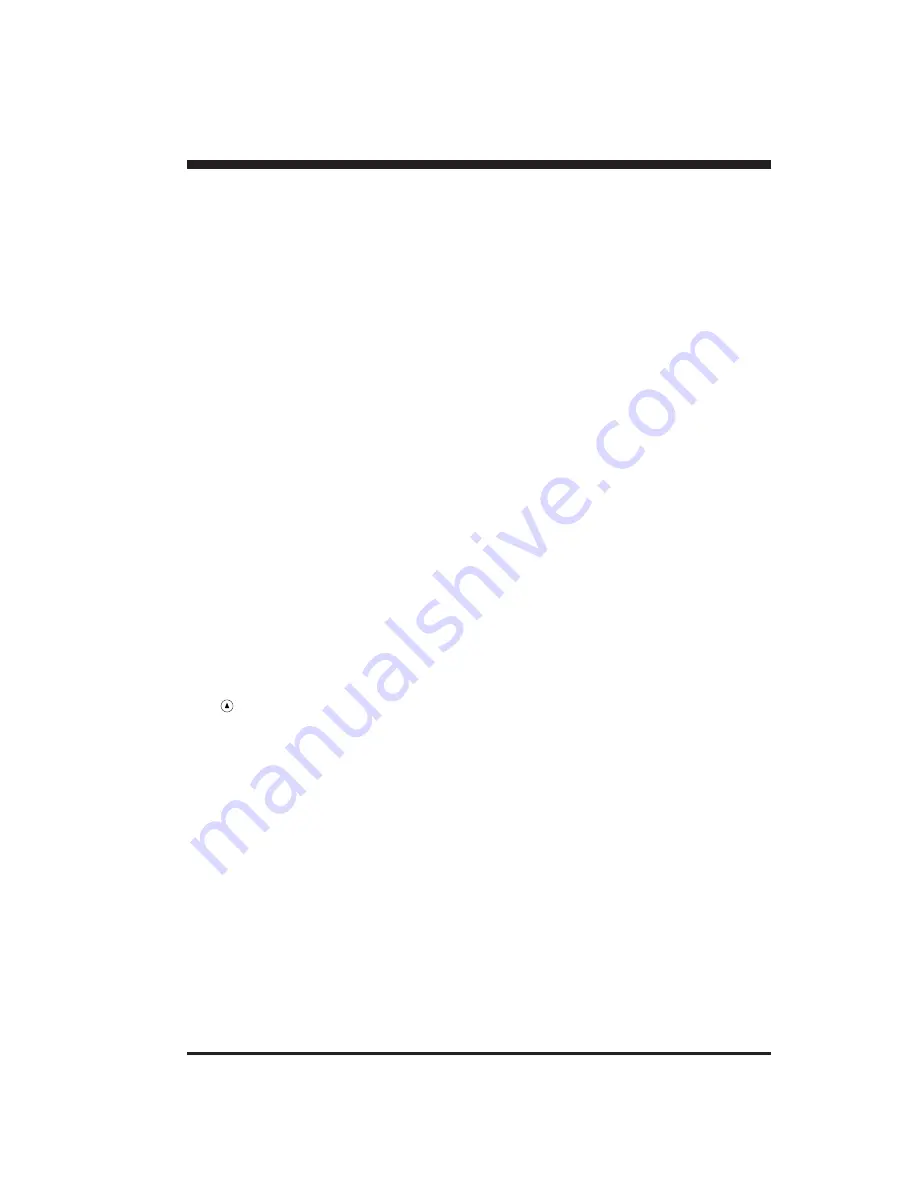
17
• If you are using a program that you have created yourself, have correct commands been sent?
The PNC-900 is equipped with the CAMM-GL III instruction system. For details, refer to "8 List of CAMM-GL III
Instructions" on page 18.
• Do the DIP switch settings match the settings made for the application software?
Refer to "4-2 DIP Switch Settings" on page 5 to make the correct DIP switch settings.
• Does the connecting cable match the settings for the application software and the computer?
Refer to the operation manuals for your application software and computer to select and connect the appropriate cable.
The sheet is not cut properly
• Are the blade and blade holder installed correctly and securely?
Install these so that there is no looseness (see "4-3 Installing the blade" on page 6).
• Is the blade chipped?
If it is, replace it with a new one (see "4-3 Installing the blade" on page 6).
• Check if there are any dirty deposits on the blade.
If dirty, remove and clean the blade.
• Make sure you are using an appropriate blade force setting.
Perform a "cutting test," then adjust the blade force slider as necessary to obtain the optimum blade force (refer to page 9, "4-
6 Cut Test to Check Blade Force").
• If you are cutting a thick sheet, set DIP switch SW-8 to ON (heavy). (See "4-2 DIP Switch Settings" on page 5 and "Cutting
a Thick Sheet" on page 11.)
The sheet slips away from the pinch rollers during the cutting process
• Are the sheet loading levers on both the left and right sides raised?
If a sheet loading lever has not been raised, then the sheet has not been secured in place. Make sure that the pinch rollers on
the left and right sides are within the boundaries of the sheet, and raise the sheet loading levers. (Refer to "4-4 Loading a
Sheet" in on page 4.)
• Make sure the sheet is parallel with the grit roller.
If the front edge of the sheet you are working with is at an angle, cut off the odd-shaped part to make it straight, then align it
so that it is parallel with the grit roller.
• If the sheet is to be advanced over a long distance, moving the movable pinch roller inward slightly can help prevent the
sheet from becoming dislodged. Also, after loading the sheet, it is recommended that you carry out cutting after first using
the
key to advance the sheet by the amount that will be used for cutting, and make sure that the sheet does not slip away
from the stationary and pinch rollers.
• If a roll sheet is used, carry out cutting after first pulling out the amount of sheet that is to be used. The sheet is susceptible
to slips when it is pulled out by the cutting process.
• Make sure that the left and right edges of the sheet do not touch the inner surfaces of the PNC-900 during cutting. Such
contact may not only damage the sheet, but could also make normal sheet advancing impossible and cause the sheet to slip.