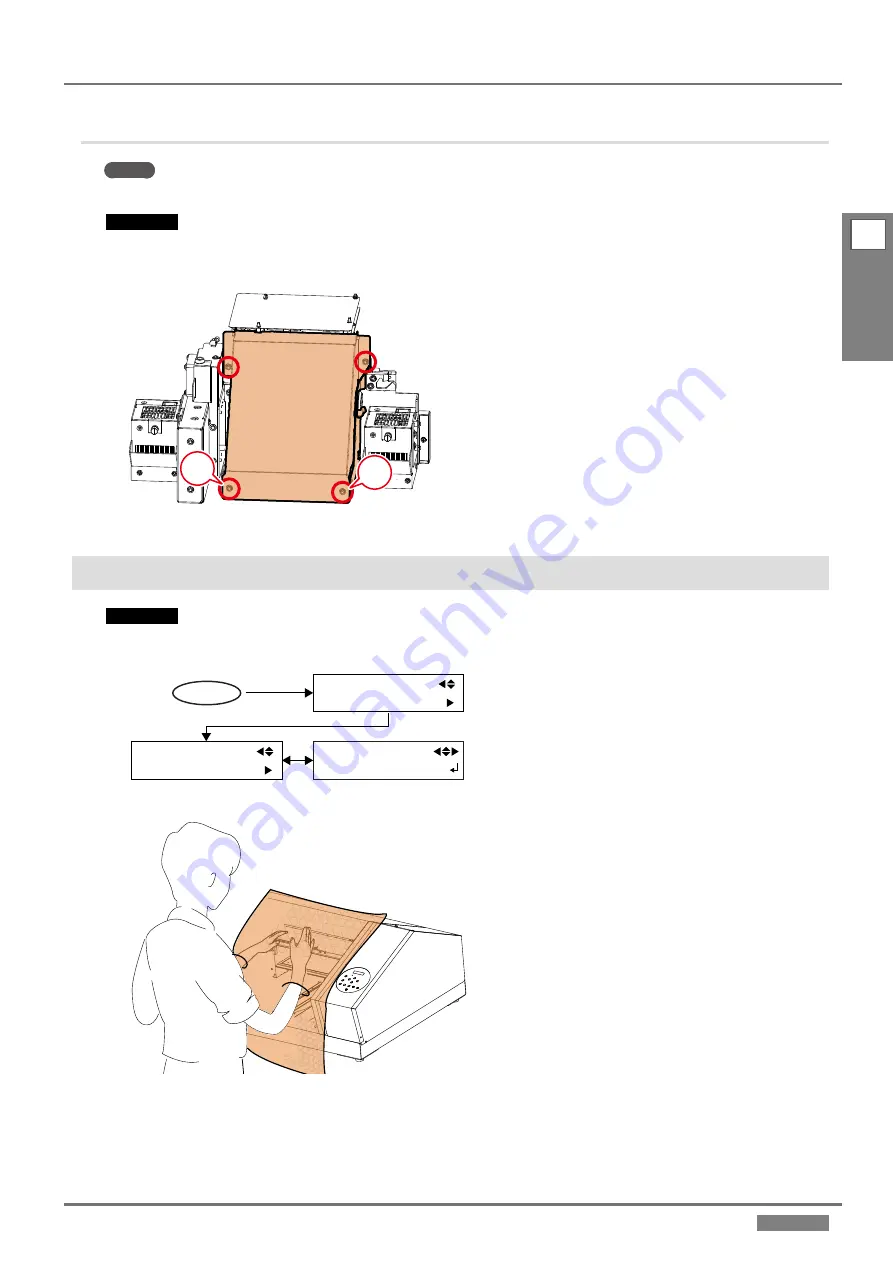
1-96
LEF2-300
1
R
EPLACEMENT
Linear Encoder Board Replacement
Notes when attaching carriage cover
NOTE
When attaching the carriage cover, tighten four screws loosely first, then tighten them fully to secure the cover.
CAUTION
When tightening the two screws on the front, be careful not to tighten them too hard. Doing so may cause the carriage
cover to be distorted and the print heads may become shifted.
!
!
Workflow
CAUTION
•
To prevent hardened ink from entering into the nozzle, refresh print head before the adjustment. Perform medium cleaning
on all print heads if 20 minutes passes.
FUNCTION
CLEANING
MEDIUM CL.
FUNCTION
CLEANING
MEDIUM CL.
AB
•
Always use the UV protection sheet during this adjustment, or ink will harden and clog inside the ink line.