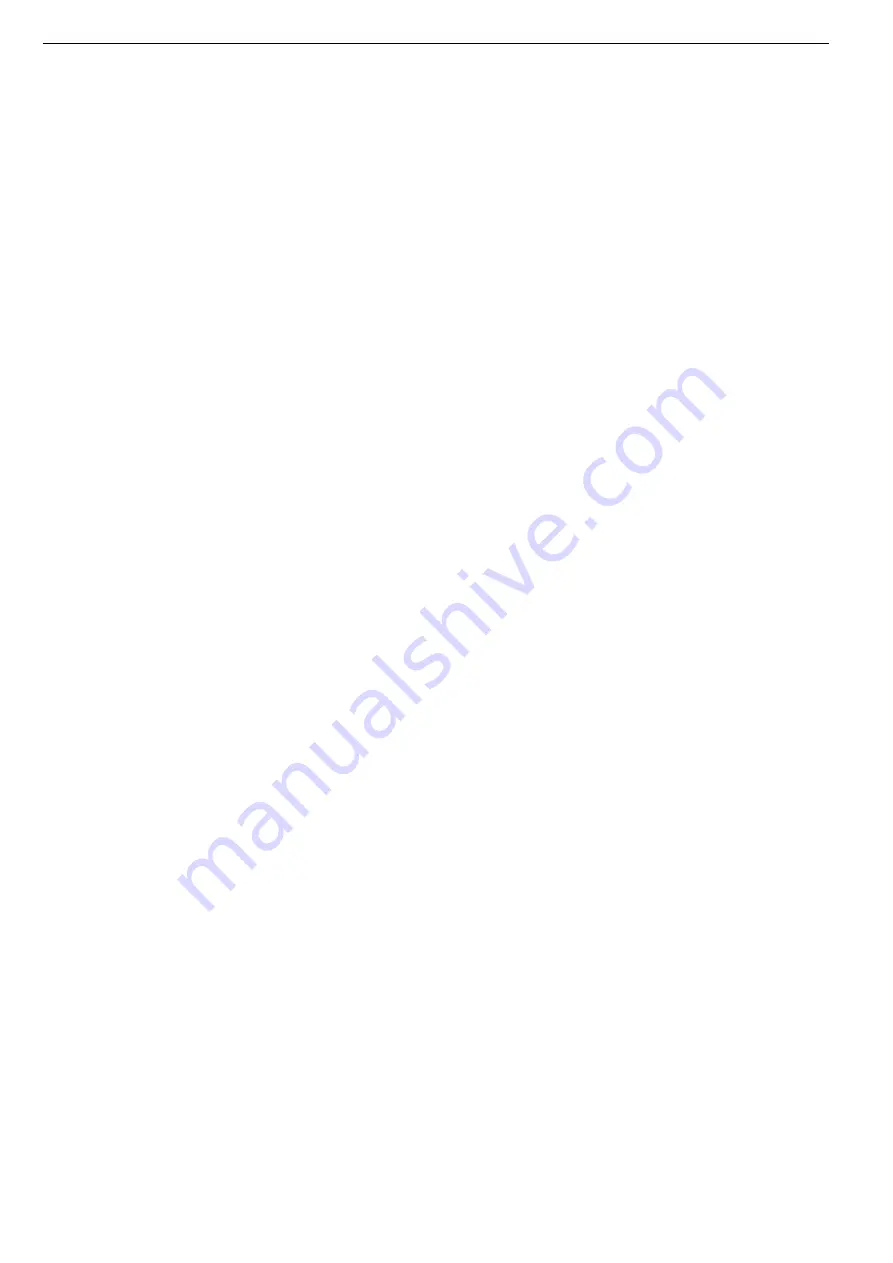
eng
eng
Specific Safety Instructions
●
Do not overload the electric pipe cutting machine. Do not use damaged
cutting wheels. Use moderate feeding pressure.
●
Caution! Keep hair, clothing and gloves away from the pipe rest when
a pipe is rotating in the rollers. Loose clothing, jewellery or long hair
could get caught between the rotating pipe and the rollers.
●
Do not reach into the rotating cutting wheel.
●
Where necessary use a material support ROLLER’S Assistent (Art. No.
120000) on each side to support long pipes and position the pipe and
material support(s) exactly with the pipe support (6) of the electric pipe
cutting machine.
1. Technical Data
1.1. Article Numbers
ROLLER’S Smart-Cut
844000
ROLLER’S cutting wheel Cu-INOX
844050
ROLLER’S cutting wheel V
844051
ROLLER’S Assistent material support on tripod
120000
ROLLER’S Herkules Y material support clamping fixture
120130
ROLLER’S Werkmeister folding workbench
120200
1.2. Application Area
Pipes of pressfitting systems made of
●
stainless steel, C-steel (not jacketed)
Ø 12 – 28 mm
●
semi-hard and hard copper
Ø 12 – 35 mm
●
composite pipes
Ø 12 – 40 mm
1.3. Speed
Idle speed of cutting wheel
125 rpm
1.4. Electrical Data
230 V 1~; 50 – 60 Hz; 200 W
fuse protection (mains) 10 A (B), intermittent service AB 2/10 min,
insulated, interference suppressed.
1.5. Dimensions
L × W × H:
405 × 90 × 103 mm (10” × 3.5” × 4”)
1.6. Weights
1.9 kg (4 lb)
1.7. Noise Data
Workplace-related emission value
76 dB(A)
1.8. Vibrations
Weighted effective value of the acceleration
2.5 m/s²
2. Commissioning
2.1. Electrical Connection
Pay attention to main voltage! Before connecting the device, make
sure that the voltage specified on the rating plate matches the mains
supply.
2.2. Installation of the Machine
Place the electric pipe cutting machine on a workbench or similar or
unscrew the pipe arm (2) and clamp the base frame (1) in a vice or
bolt the base frame to the workbench with bolts through holes (3).
Where applicable, longer pipes must be supported on both sides with
ROLLER’S Assistent (Art. No. 120000).
2.3. Installing (changing) the cutting wheel (4)
Pull out the mains plug! Select a suitable cutting wheel:
●
ROLLER’S cutting wheel Cu-INOX
for stainless steel pipes, steel
pipes and copper pipes of the pressfitting systems.
●
ROLLER’S cutting wheel V
for multi-layered composite pipes of
the pressfitting systems.
Remove hexagonal nut (5) with size 10 ring spanner. Insert (change)
cutting wheel (4). Make sure that the carrier pins of the drive shaft grip
into the holes of the cutting wheel. Replace the hexagonal nut (5).
Caution:
If an unsuitable cutting wheel is used, the wheel will be
damaged or the pipe will not be cut. Only use original ROLLER’S
cutting wheels!
3. Operation
Caution, danger of injury!
Keep hair, clothing and gloves away from the pipe rest (6) when a pipe is
rotating in the rollers. Loose clothing, jewellery or long hair could get caught
between the rotating pipe and the rollers.
3.1. Work Procedure
Mark the cut on the pipe. Pull the handle (7) far enough up so that the
pipe to be cut can be inserted into the pipe rest (6).
Caution:
Support longer pipes (see 3.2). Press the touch switch (8)
and press the handle (7) against the pipe rest and cut the pipe.
Caution:
The cut pipe sectors can fall to the floor immediately after
being cut!
3.2. Supporting the Material
Where applicable, longer pipes must be supported on both sides with
ROLLER’S Assistent (Art. No. 120000).
4. Maintenance
Pull out the mains plug before carrying out maintenance and repair work!
This work may only be performed by qualified personnel and instructed
persons.
4.1. Maintenance
Keep the rollers of the pipe rest clean. The ROLLER’S Smart-Cut gear
run with a life-long grease filling and does not need lubrication.
4.2. Inspection/Service
The motor has carbon brushes which are subject to wear. The electric
pipe cutting machine must therefore be inspected by an authorised
ROLLER service workshop from time to time. The carbon brushes
cannot be replaced so that the motor has to be changed when neces-
sary. See also 5. Behaviour in the Event of Faults.
5. Behaviour in the Event of Faults
5.1. Fault:
Electric pipe cutting machine stops during operation.
Cause:
●
Feed pressure too high.
●
Blunt cutting wheel.
5.2. Fault:
Pipe stops during cutting.
Cause:
●
Pipe not round or not deburred on the outside.
●
Idle rollers of the pipe rest soiled.
5.3. Fault:
Pipe is not cut.
Cause:
●
Unsuitable cutting wheel.
●
Pipe not round or not deburred on the outside.
●
Cutting wheel damaged.
5.4. Fault:
Electric pipe cutting machine does not start.
Cause:
●
Defective connecting cable.
●
Defective device.
5.5. Fault:
Cutting wheel goes blunt or breaks off after 1 or 2 cuts.
Cause:
●
Cutting in a notch in which the previous cutting wheel
was already blunted or damaged.
6. Manufacturer’s Warranty
The warranty period shall be 12 months from delivery of the new
product to the first user but shall be a maximum of 24 months after
delivery to the Dealer. The date of delivery shall be documented by
the submission of the original purchase documents, which must include
the date of purchase and the designation of the product. All functional
defects occurring within the warranty period, which clearly the conse-
quence of defects in production or materials, will be remedied free of
charge. The remedy of defects shall not extend or renew the guarantee
period for the product. Damage attributable to natural wear and tear,
incorrect treatment or misuse, failure to observe the operational instruc-
tions, unsuitable operating materials, excessive demand, use for
unauthorized purposes, interventions by the Customer or a third party
or other reasons, for which ROLLER is not responsible, shall be
excluded from the warranty.