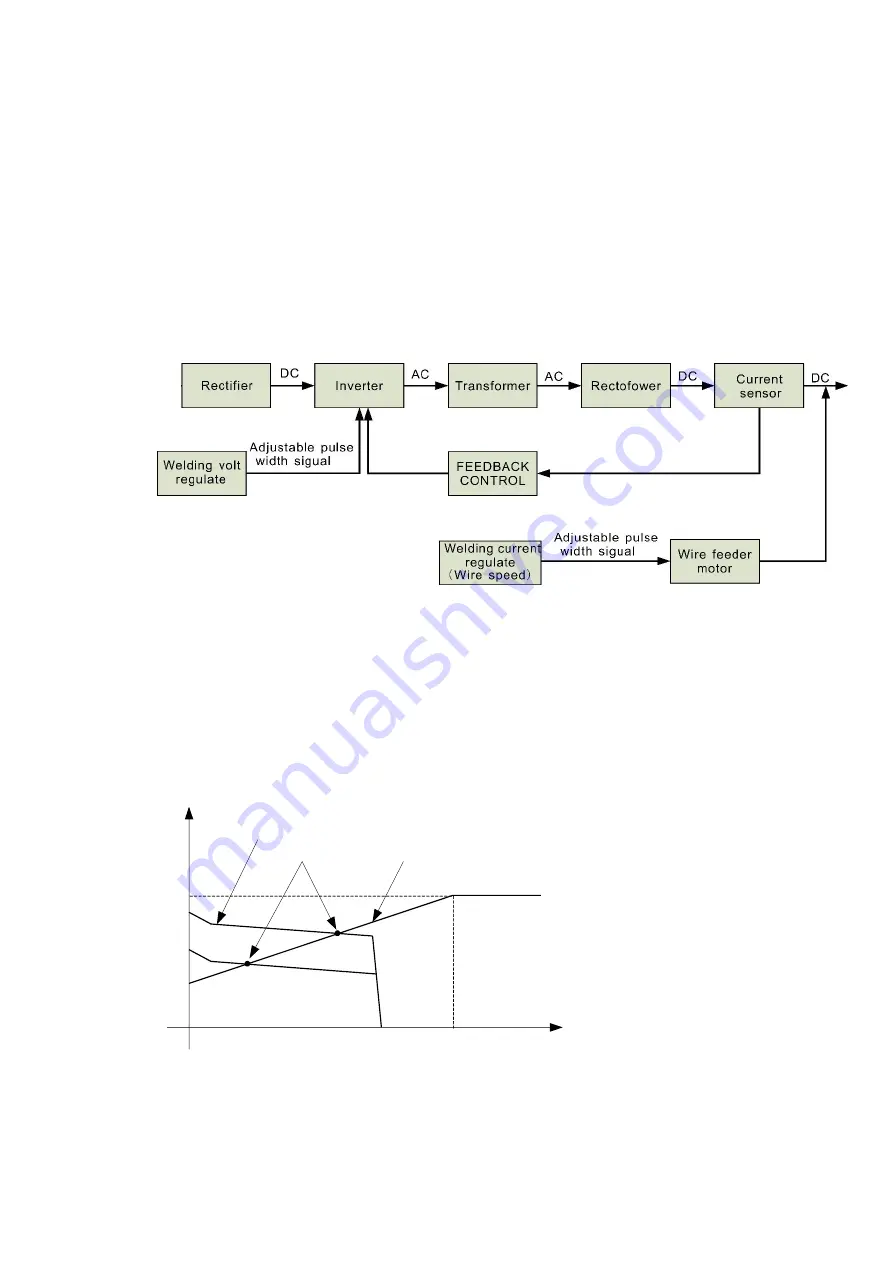
9
•
2.2. Working Principle
The working principle of RONCHWELD 250MIG arc welding machine is shown as the following
figure. Single-phase 220V work frequency AC is rectified into DC
(
312V
)
, then is converted to
medium frequency AC (about 40KHz) by inverter device (IGBT), after reducing voltage by medium
transformer (the main transformer) and rectifying by medium frequency rectifier (fast recovery
diodes), and is outputted by inductance filtering when MIG. Meanwhile, the welding current
parameter can be adjusted continuously and infinitely to meet with the requirements of welding
craft.
•
2.3. Volt-Ampere Characteristic
RONCHWELD 250MIG welding machine has an excellent volt-ampere characteristic, whose graph
is shown as the following figure. The relation between the rated loading voltage U
2
and welding
current I
2
is as follows: U
2
=14+0.05I
2
(V)
44
14
0
600
I
o
(
A
)
U
o
(
V
)
Working point
Volt-ampere characteristic
The relation between the rated loading
voltage and welding current
Single-phase AC
220V, 50/60HZ
Summary of Contents for 250MIG
Page 1: ...SERIES 250MIG MIG ...
Page 10: ...10 2 4 Principles of welding ...
Page 16: ...16 4 OPERATION ...
Page 23: ...23 5 3 ELECTRICAL SCHEMATIC DRAWING ...
Page 24: ...24 250MIG MIG ...