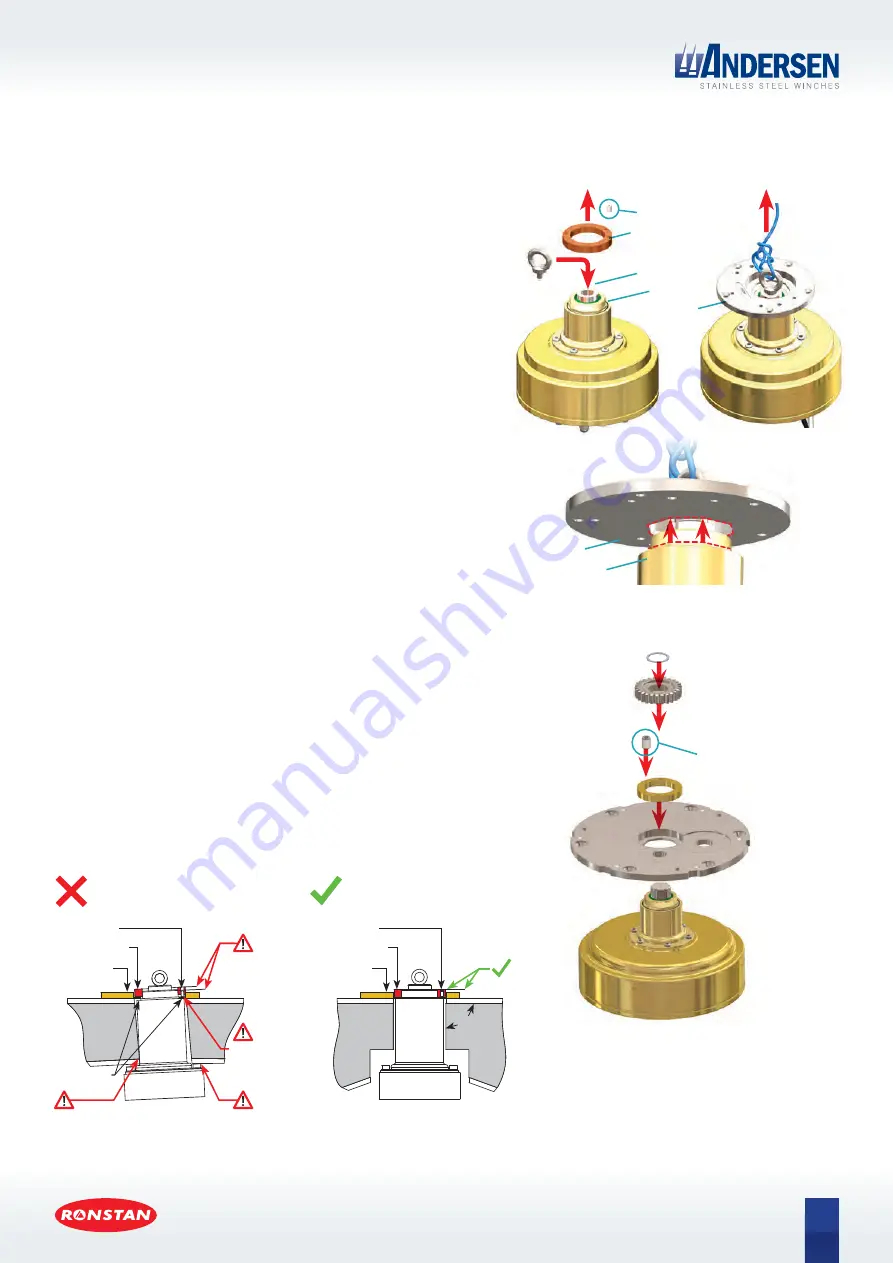
9
PRODUCT MANUAL
68/72ST Below Deck Compact Motor
™
STEP 3
Fit the motor unit to the deck plate
Correct alignment of the motor during assembly is essential. Improper
alignment can cause excessive noise and vibration and lead to
premature wear of bearings and gears. For best results the following
steps should be carried out by two persons.
3.1 Refer to the exploded diagram and remove the circlip [2],
gearwheel [3] to expose the clamping ring [6].
3.2 Back out the locking grub screw [5] and use the pin spanner
[A6] to remove the clamping ring from the top of the drive shaft
housing, taking care that the O-ring underneath remains in place.
3.3 Screw the M6 eye bolt [A5] into the threaded hole in the top of
the drive shaft. Attach a strong rope or use a lifting device to raise
the motor unit into position so that the drive shaft protrudes
through the large octagonal hole in the deck plate.
3.4 Align the motor unit so that the protruding octagonal detail at the
top of the drive shaft housing mates snugly with the octagonal
recess in the deck plate, for a uniform flush fit.
3.5 Fit and securely tighten the clamping ring using the pin spanner,
then insert and tighten the locking grub screw. Watertight
assembly is ensured by the O-ring under the deck plate; no
additional sealant is required.
3.6 After securing the clamping ring, reassemble the gearwheel and
circlip on the shaft.
3.7 Refer to the diagrams below to check for correct clearance and
alignment.
Octagonal detail on drive shaft housing
mates with recess in deck plate.
Correct mating of
drive shaft housing top flange
with underside of winch base
Incorrect mating of
drive shaft housing top flange
with underside of winch base
90°
Clamping Ring
Grub Screw
Clamping Ring
Grub Screw
Motor flange
Non-aligned hole in
deck preventing correct
motor alignment
Inadequate underdeck
clearance preventing
correct motor alignment
Deck Plate
Deck Plate
Grub screw
protruding too
far
Clamping ring
not parallel to
deck plate
2.
4.
5.
Clamping ring
Grub screw
Drive shaft
Deck plate
O-ring
Eye bolt
Deck plate
Drive shaft housing
Locking
grub
screw
3.