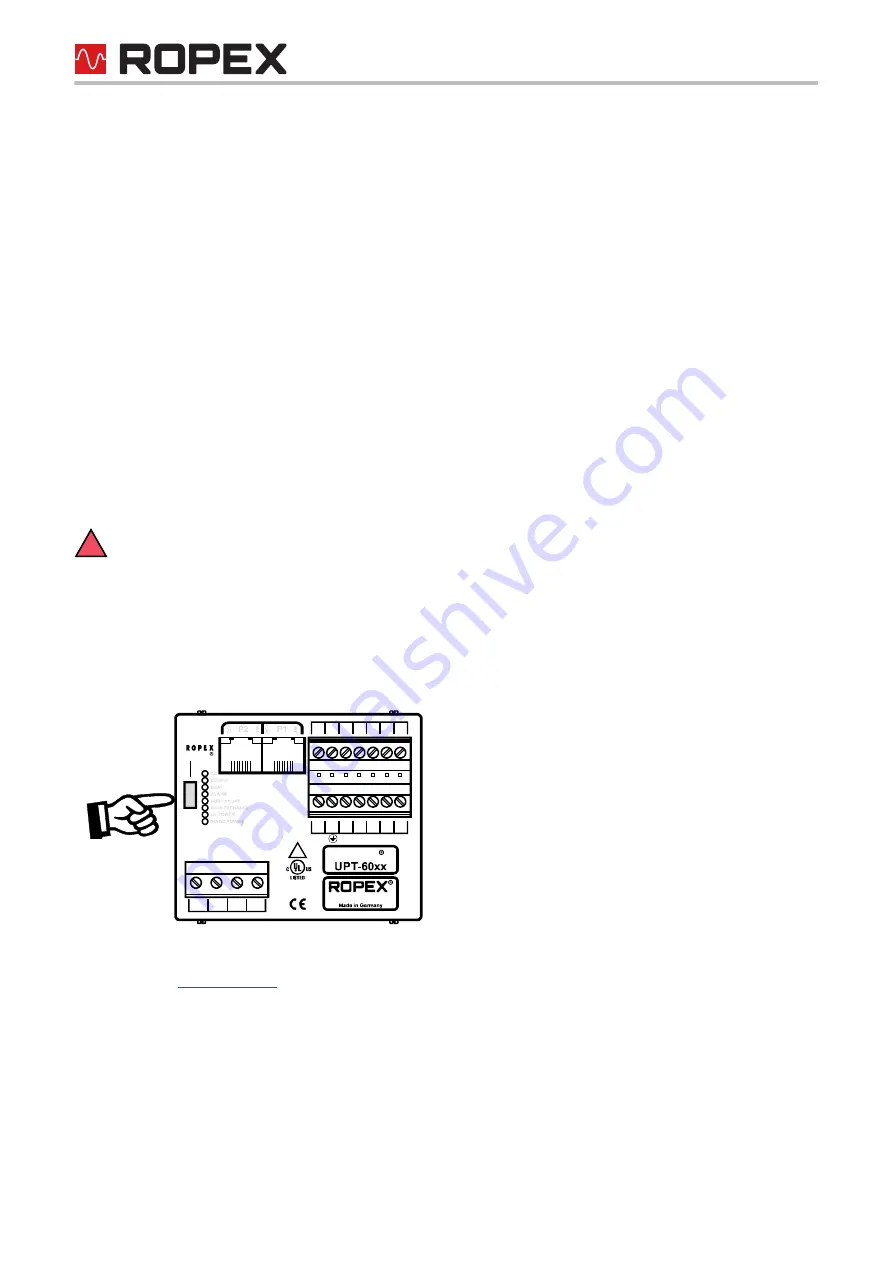
Device functions
Seite 44
UPT-6012
Version 2
An indicating instrument can be connected to this output in order to visualize the temperature of the heating ele-
ment.
The ROPEX ATR-x temperature meter is optimally adapted to this application in every respect (size, scale,
dynamic behaviour) and can be used for this, if needed (
section 13 "How to order" on page 56).
The meter not only facilitates SET-ACTUAL comparisons but also enables other criteria such as the heating rate,
set point achieved within the specified time, cooling of the heating element etc. to be evaluated.
The temperature meter additionally permits disturbances in the control loop (loose connections, contacting or
wiring problems) as well as any line disturbances to be observed extremely efficiently and interpreted accordingly.
The same applies if several neighbouring control loops interfere with one another.
If a fault is signalled, this analog output is used to display a selective error message (
8.11
Booster connection
The UPT-6012 controller has a connection for an external switching amplifier (booster) as standard. This connec-
tion (at terminals 15+16) is necessary for high primary currents (continuous current > 5 A, pulsed current > 25 A).
The booster should be connected as described in section 6.7 "Wiring diagram with booster connection" on
page 14.
The connecting cable to the booster must not be longer than 1 m; it must also be twisted in order to
reduce EMC interference to a minimum.
8.12
USB interface for visualization software ROPEXvisual
®
A USB interface (type: Micro USB) is provided for system diagnostics and process visualization. This USB inter-
face enables a data connection to be set up to ROPEXvisual
®
, the ROPEX visualization software.
The ROPEX visualization software is described in a separate document. The software and the documentation are
available in the
(search term: “Visual”).
!
12 13 14 15 16 17 18
9
8
6
5
10 11
7
4
3
2
1
www.
.de
ROPEX
Visual
!
PROCESS CONTROL
EQUIPMENT
E464680
CIRUS