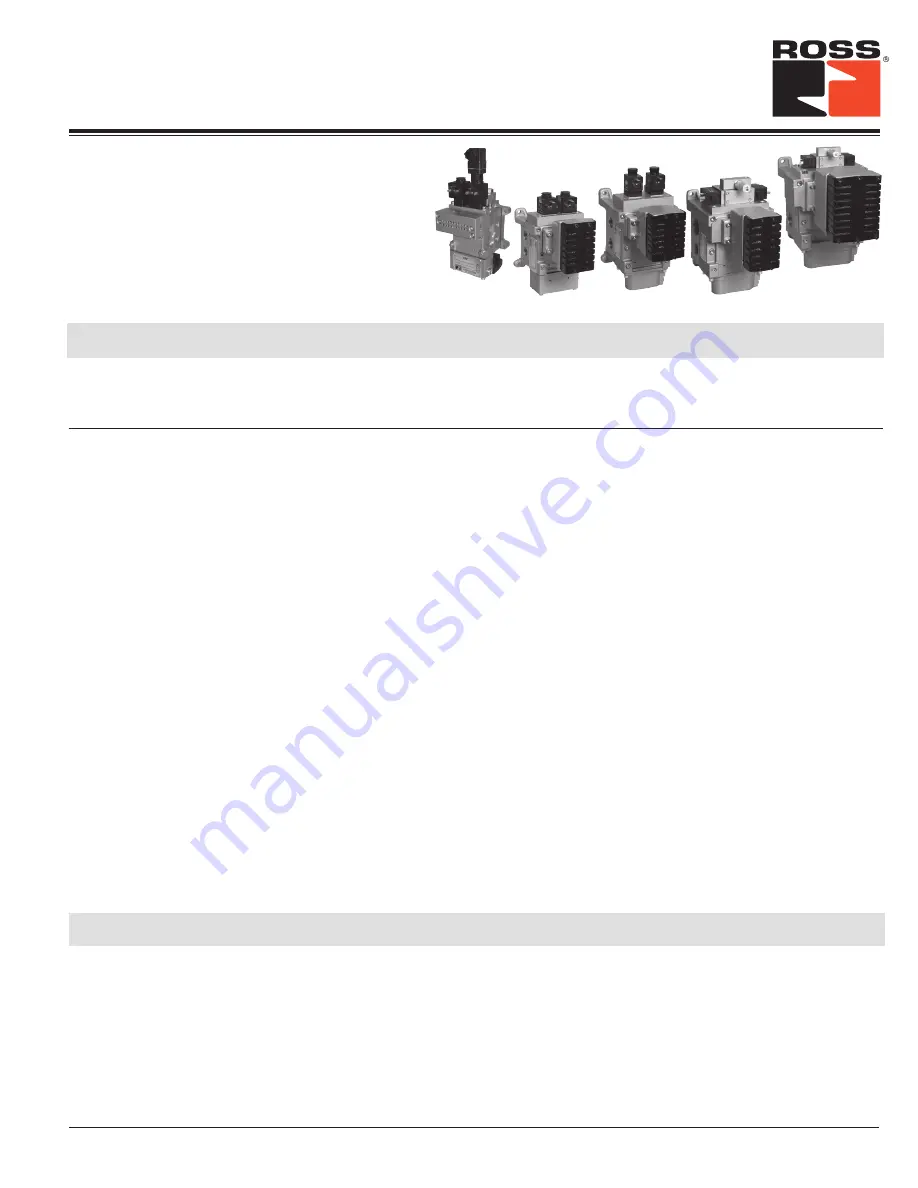
Monitored - For Clutch/Brake Control
DM
2 ®
Series
D Press Double Valves
Thank You!
Pneumatic equipment should be installed only by persons trained and
experienced in such installation.
Air Lines:
Before installing this valve in a new or existing system, the air lines
must be blown clean of all contaminants. It is recommended that a 5-micron-
rated air filter be installed in the inlet line close to the valve.
Valve Inlet (Port 1):
Be sure that the supply line is of adequate size and does
not have any restrictions (e.g., a crimp in the line, a sharp bend, or a clogged
filter element). The air supply must not only provide sufficient pressure (
see
Standard Specifications, page 3
), but must also provide an adequate flow of
air on demand. Otherwise, the valve elements will be momentarily starved
for air and the valve may fail to operate.
Valve Outlet (Port 2):
For faster pressurizing and exhausting of the mechanism
being operated by the valve, locate the valve as close as possible to the
mechanism. The lines must be of adequate size and be free of restrictions
(e.g., a crimp in the line, a sharp bend, or a clogged filter element).
Valve Exhaust (Port 3):
Do not restrict the air flow from the exhaust port as
this can adversely affect the operation of the valve. The valves are factory
equipped with a properly sized silencer. ROSS silencers reduce impact noise
by as much as 25 dB, and produce little back pressure.
Reset Port (RESET):
If your valve is not equipped with a reset solenoid on
the valve, then the RESET port should be supplied, externally, from a 3/2
normally closed valve. The lines must be of adequate size and be free of
restrictions (e.g., a crimp in the line, a sharp bend, or a clogged filter element).
Reset signals must be momentary.
Electrical Supply:
DM
2®
Series D double valves get electrical power through
plug-in connectors. The electrical supply must correspond to the voltage
and Hertz ratings of the solenoids. Otherwise, the solenoids are subject to
early failure. If power is supplied by a transformer, the power supply must be
capable of handling the maximum power. See
Valve Specifications
on page
3 for information on maximum power.
Operating Pressures and Temperatures:
Allowable ranges for pressure and
temperatures are given in the
Standard Specifications
on page 3. Exceeding
these values can adversely affect performance and shorten valve life.
Pipe Installation:
To install pipe in base ports, engage the pipe by one
turn, then apply pipe thread sealant (tape not recommended), and tighten
pipe. This procedure will prevent sealant from entering and contaminating
the valve. To install pipe with parallel threads (e.g., SAE, ISO 228-G, etc.)
do not use sealant. After installing pipe into the base ports, use compressed
air to blow any debris out of the piping, then install the valve onto the base.
Test:
After installation or repair, and prior to normal use, the internal lockout
feature of the DM
2®
Series D double valve must be tested for proper functioning.
Observe normal press operation safety precautions during these tests to avoid
personal injury or damage to equipment.
Note:
Reset may need to be performed prior to beginning the test procedure.
Also, both pilot solenoids must be de-energized prior to reset and must remain
de-energized until after the reset signal is removed.
A)
Electrically energize both pilot solenoids simultaneously, then de-energize
one pilot solenoid. This should result in a valve lockout and prevent the valve
from operating.
B)
Energize both solenoids and the valve should remain in the lockout condition.
C)
De-energize both pilot solenoids and reset the valve.
D)
Electrically energize both pilot solenoids simultaneously again. De-energize
the other pilot solenoid this time. Again, this should result in a lockout.
E)
Energize both pilot solenoids. The valve should remain in a lockout condition.
F)
De-energize both pilot solenoids and then reset the valve.
After satisfying these tests, energizing both pilot solenoids simultaneously
should result in normal operation.
Fault Indication:
If fault indication is desired, ROSS offers a status indicator
option that can be used to signal to the press controls that a fault has occurred.
The status indicator utilizes a pressure switch. The pressure switch has 4
electrical contacts. During normal operation the pressure switch is pressurized.
A lockout condition depressurizes the switch until the valve is reset. Contacts
1 and 2 are closed when the switch is depressurized (normally closed) and
contacts 1 and 3 are closed when an adequate pressure signal is applied to
the switch (normally open).
Basic Size 2
VALVE INSTALLATION
Basic Size 8
Basic Size 30
Basic Size 12
Basic Size 4
You have purchased a premium-quality ROSS
®
pneumatic valve.
It is a high quality DM
2®
Series D double valve with dynamic
monitoring and inherent lockout capability, for Category 4
applications. The valve is designed for base mounting for ease
of installation and maintenance. With care in its installation and
maintenance you can expect it to have a long and economical
service life.
Before you install this valve, read the information in this folder
completely, and save it for future reference.
ROSS
CONTROLS
®
www.rosscontrols.com
Please read and make sure you understand all installation instructions before proceeding with the installation.
Additional technical documentation is available for download at www.rosscontrols.com.
If you have any questions about installation or servicing your valve, please contact ROSS or your authorized ROSS distributor, see contact
information listed at the back of this document, or visit www.rosscontrols.com to find your distributor.
On first operation, or after repair, the pilot valve supply circuit and inherent
monitoring elements may need to be reset. This reset is accomplished by
applying a momentary air signal to the RESET port or by energizing the
optional reset solenoid momentarily on the valve. After reset, the valve will
then be ready for operation.
The air supply to each pilot valve is controlled by the position of the inlet
poppets. In the ready-for-operation position these poppets are held on their
seats and maintain pilot air flow. During shifting of the valve elements the
poppets move off seat and momentarily allow pilot air to escape to exhaust.
If either valve element fails to operate correctly, the pilot supply to the other
valve element will remain connected to exhaust causing the valve to lock-out.
The internal monitoring system will lock out the valve if the time difference
between both elements shifting fully is longer than approximately 125 mil-
liseconds. This timing is preset by restricting-orifices and chambers in the
pilot air circuit.
The main airflow from port 1 to port 2 is via crossflow passages between
both main valves, so that both valve elements must be fully shifted in order
for port 2 to be pressurized.
If the valve locks out, further operation is prevented until the valve has been
reset. Electrical signals to the solenoids must be "off" to allow the valve to
be reset.
The DM
2®
Series D double valve is completely self-contained and does not
need an external monitoring system.
VALVE OPERATION