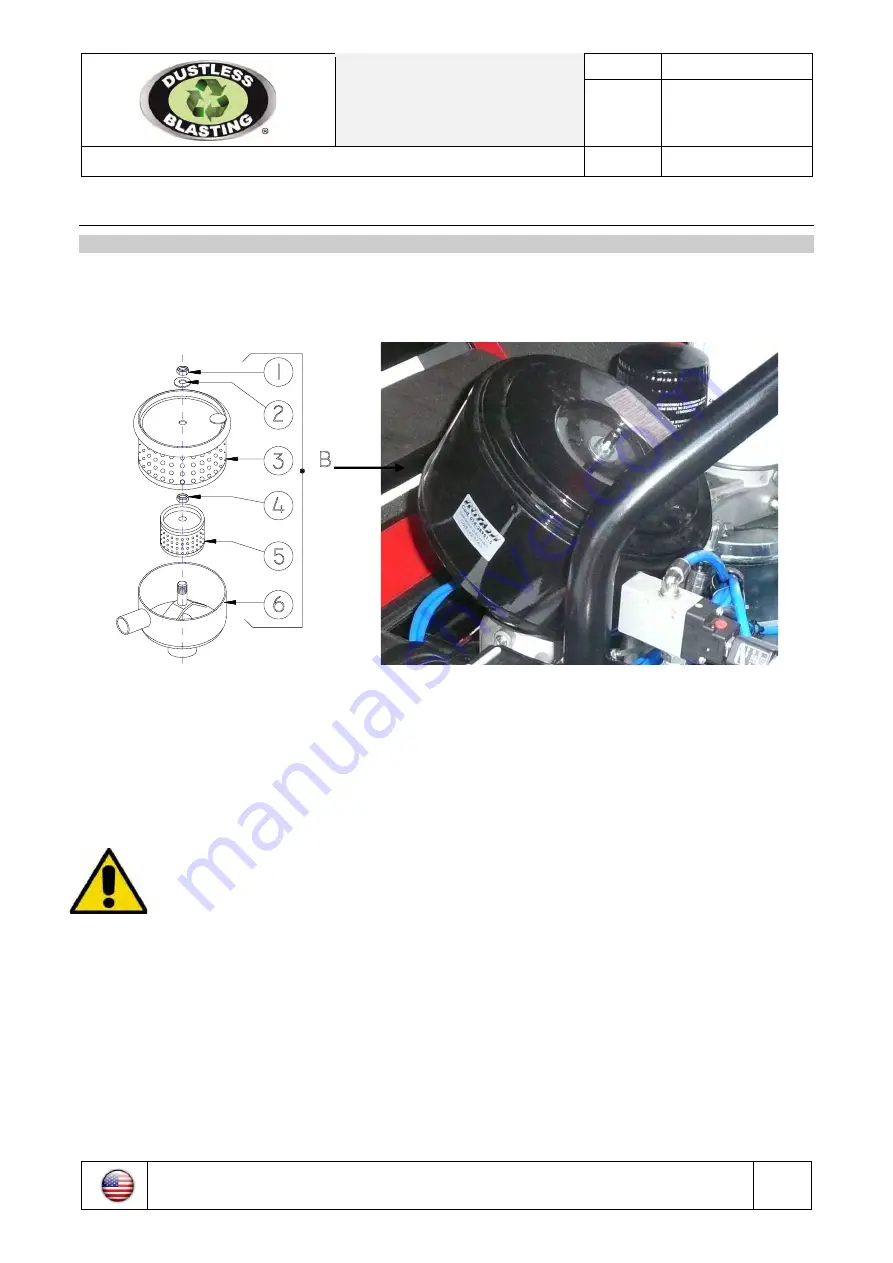
USER'S AND
MAINTENANCE
MANUAL
Date:
01/31/2020
Code
MAN D185T4F-DB
ENG
Air Compressor : D185T4F-DB
Revision 03
Copyright © 2014, ROTAIR S.P.A. - All rights reserved
.
This manual is intellectual property of ROTAIR S.P.A.
Its full or partial reproduction is forbidden under any form, on any support and by any means, without the
written authorization by ROTAIR S.P.A.
Page
47/59
13.4 Maintenance
13.4
-
1
CHECKING AIR FILTERS (INTAKE VALVE)
This check should be performed periodically
after
every 100 hours of work
.
If the machine operates
in
severe
conditions, especially
very dusty environment
s
, it will be necessary
to perform these checks
on a
daily basis.
COMPRESSOR AIR FILTER
Figure 13.4-1A
Compressor
air filter
The filter consists of two filtering elements. To check them, loosen the nut (Figure13.4-1A, (1)
) and remove
the element of the 1st stage
(outer)
(3). Should any traces of dust be noticed on the element of the
2nd stage
(inner)
(5), remove this one also by removing the nut (4).
The filter element must never be washed with water or other substances, but it must be
replaced after every 500 hours of work.