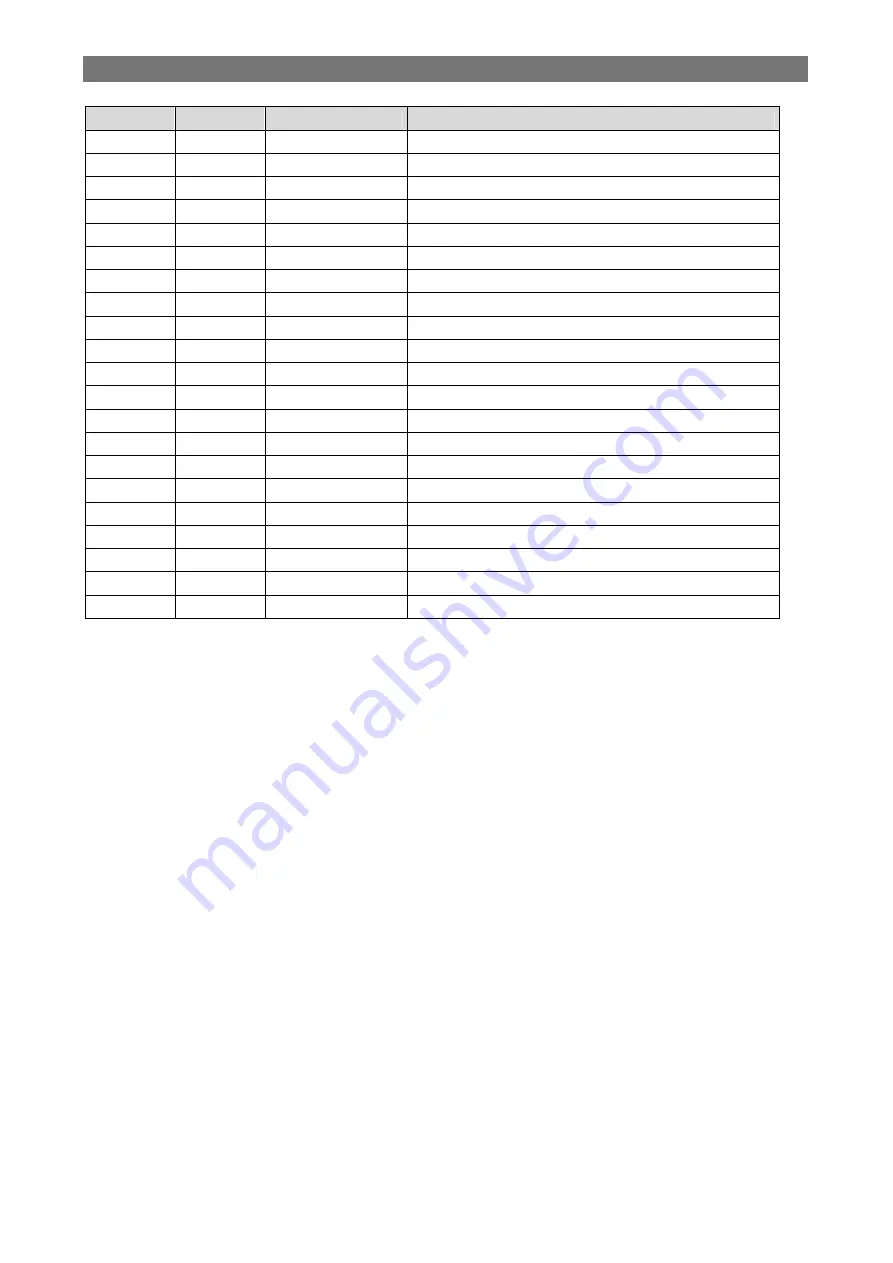
Pos:
Qty.
Code
Description
1
1
KE971PL05Z
M04.Z
central
manifold
KE
2000
(80
‐
250
bar)
2
1
KE970TR008
TR08
Coupling
3
1
V389669E20
VE1
‐
NC
‐
EM
electric
valve
cav.V096004
4
1
R3897TA226
TC4
Plug
for
cavity
‐
(only
thread)
5
1
V388540000
PMC12
Hand
pump
(1.5
cc)
6
1
K250113000
Lever
M10
L=190
mm
7
1
CV10114302
18GH
pump
5.0cc
+
screw
M8x85
8
1
K3976SE449
S423
Plastic
Tank
12Lt.
9
1
K234062000
Suction
pipe
3/8"
L=385
10
1
K225566000
Suction
filter
3/8"
female
15l/min
(90
micron)
11
1
K234722000
Return
pipe
M12x1
l=400
12
1
C014120000
Adaptor
3/8"
for
pipes
Ø6/4
13
1
C1622S1380
948
Electric
motor
three
phase
2.2kW
230
‐
400V
50Hz
14
1
V38951900G
STF14P
Compensated
flow
control
valve
7l/min
15
1
C166401OH2
S2
‐
CE+C
Coil
24Vac
50Hz
18W
with
connector
16
1
CR12009000
Plug
DIN
908
1/4"BSPP
+
copper
ring
17
1
F331514000
G80
mounting
bracket
18
1
K2501VT014
Assembly
kit
for
plastic
tank
19
1
R3897PB001
Sealing
plastic
cap
for
relief
valve
20
1
C165747000
Oil
filling
plug
1/2"BSPP
21
1
C013620000
Adaptor
1/4"
‐
JIC
1/2"
‐
UNF
Summary of Contents for SGL35
Page 2: ......
Page 4: ......
Page 44: ...Diagrams spare parts lists 40 117592 03 2013 Figure 1 ...
Page 45: ...Figure 2 ...
Page 46: ...Diagrams spare parts lists 42 117592 03 2013 Figure 3 Figure 4 ...
Page 47: ...Figure 5 Figure 7 Figure 6 ...
Page 48: ...Diagrams spare parts lists 44 117592 03 2013 Figure 8 ...
Page 49: ...Figure 9 ...
Page 52: ...Diagrams spare parts lists 48 117592 03 2013 ...