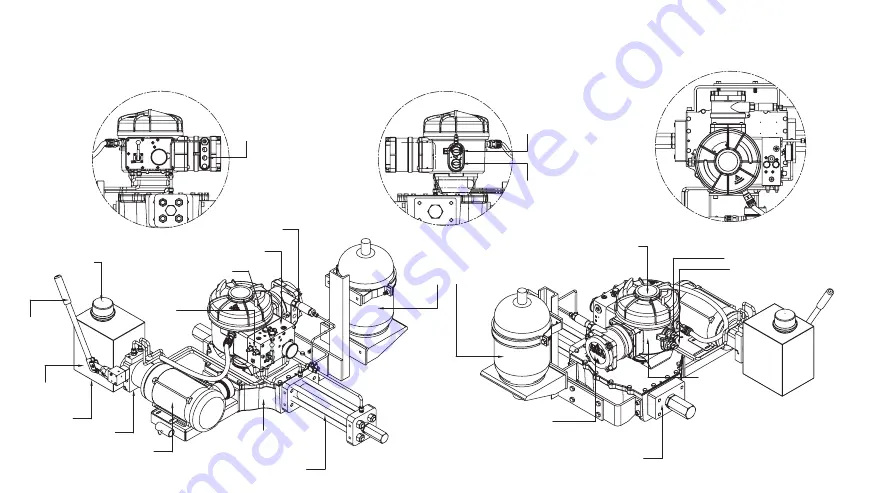
5
Identifying Actuator Parts
IV
1/2" NPT
Cable Entries
Local/Remote
Switch
Open/Close
Switch
Filler/Breather
Manual
Override
Pump
Hydraulic
Reservoir
Oil Drain
Plug
Pump
Motor
Actuator
Center Body
Hydraulic Cylinder
Manual Override Lever
Manifold
1/2" NPT
Cable Entries
Accumulator
(If applicable)
Terminal Compartment
Spring Canister
(If applicable)
Control
Module
Display Window
Open/Close
Switch
Local/Remote Switch
Speed Control
Valves