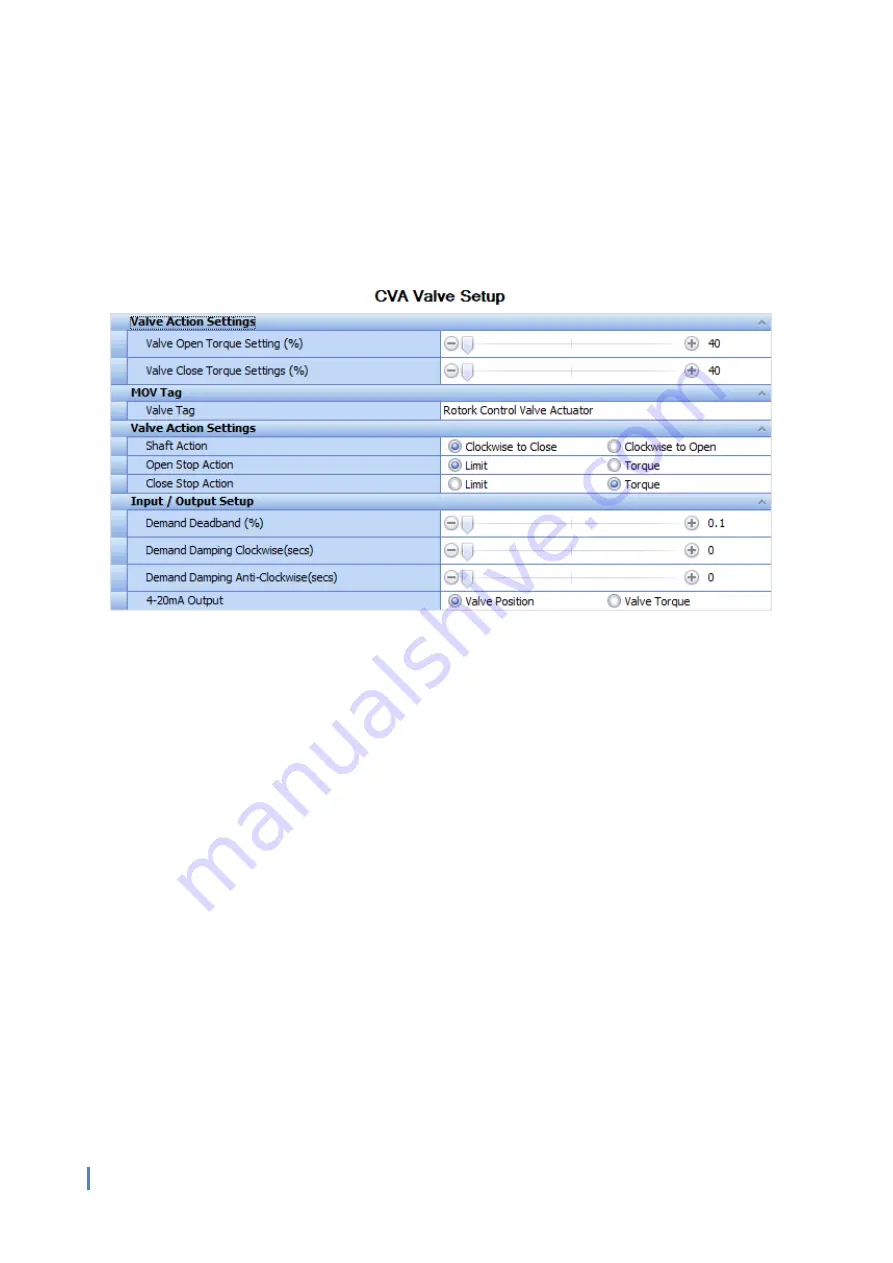
26
5.1.12 Force Sensor Serial No.
This is where the Force Sensor serial number can be entered and viewed. Rotork Service Engineer use
only.
5.1.13 User Interface Serial No.
This is where the User Interface serial number can be entered and viewed. Rotork Service Engineer use
only.
5.2 Actuator Configuration - CVA Valve Setup
5.2.1 Valve Action Settings
Valve Open Torque/Thrust Setting (%)
The slider sets the percentage of rated torque/thrust the actuator will be limited to during operation in
the open direction. This is adjustable between 40% and 100%.
Valve Close Torque/Thrust Setting (%)
The slider sets the percentage of rated torque/thrust the actuator will be limited to during operation in
the closed direction. This is adjustable between 40% and 100%.
5.2.2 MOVTag
Valve Tag
This is a user defined name for the actuator consisting of up to 32 alpha-numeric or symbolic characters.
It is normally used by operators to specify a unique tag based on location or a description of the
actuator. This setting is linked directly to the Valve Tag in the CVQ/CVL Device Information Menu (See
Section 5.1.1).
5.2.3 Valve Action Settings
Shaft Action
Specify the output direction of the actuator. CVL actuators can be configured for extend to close or
extend to open operation. CVQ actuators can be configured for clockwise to close or anti-clockwise to
close.
Summary of Contents for Insight 2
Page 1: ......