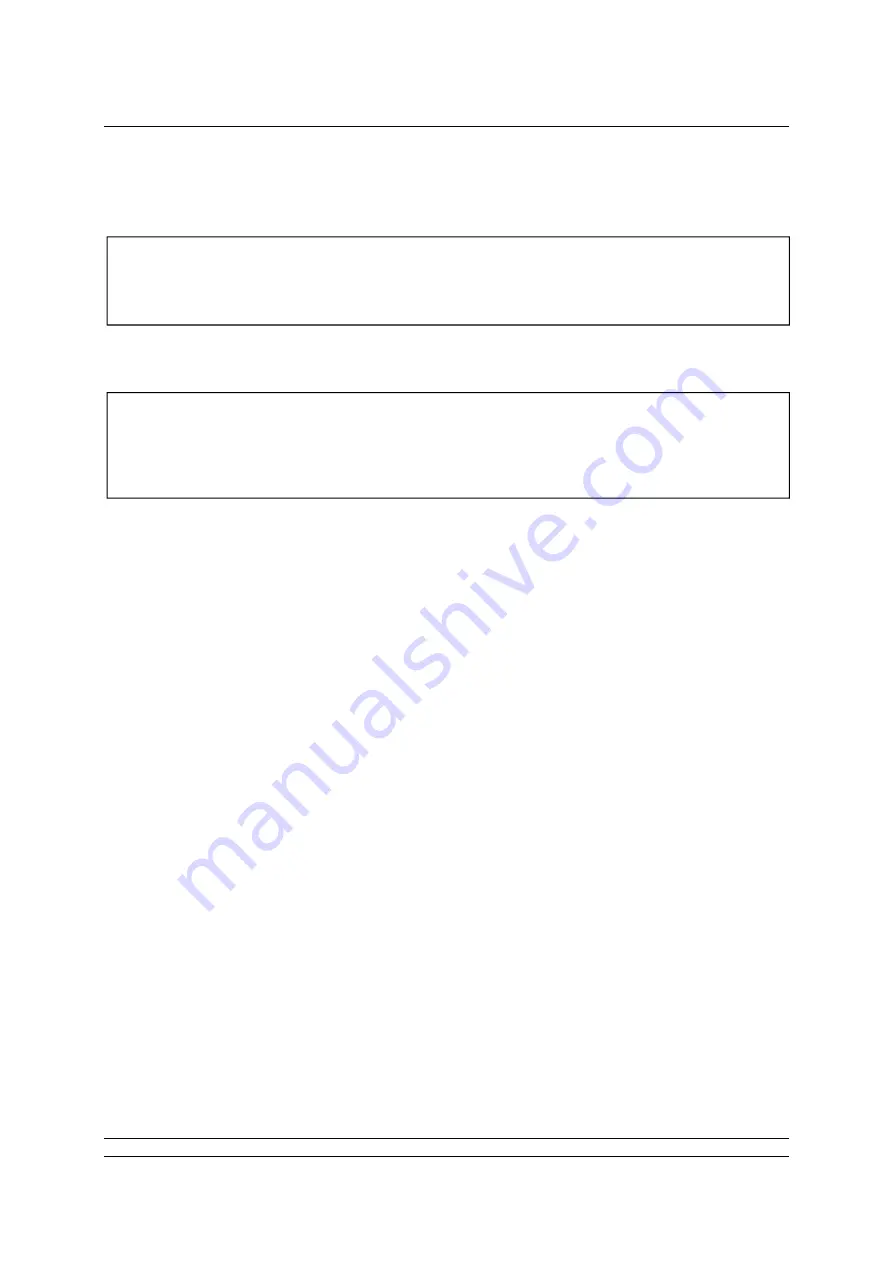
Input and Output Signals
Publication PUB091-003-00_0119
35 of 76
The bit will remain true (1) until the actuator position changes by 2%
or more.
Valve Jammed
This bit will be true (1) if the actuator is stationary at the end of travel
and fails to move away from the seat of the valve when a network
command requests it to do so. The actuator will trip on excessive
torque due to the valve being jammed in the seat. The MFU fails to
see movement and reports this status after the time set in the
associated parameter during the MFU set up. (This could indicate a
thermostat trip in a ROMpak actuator).
The bit will remain true (1) until the actuator position changes by 2%
or more.
Valve Moving by Hand
The manual movement of the valve is reported as true (1)
if the actuator is moved by the handwheel away from the last position.
The percentage of travel required to trip the indication is set in the
associated parameter during MFU set up.
The bit will remain true (1) until the actuator is moved electrically by
either the local controls or a network command.
Moving Inhibited
This bit will be true (1) when the Motion Inhibit Timer is active or the
Interrupter Timer is active (IQ/IQT only), or both are active.
The Motion Inhibit Timer is used in position control to prevent the
actuator from exceeding its prescribed number of starts per hour, or to
reduce the effects of hunting during closed loop control.
The Interrupter Timer in the IQ/IQT can be used over part or the entire
actuator stroke to slow down the effective speed of valve travel.
When under network control, the control signal does not need to be
re-applied when this bit is true, as the control action will continue once
the time has elapsed.
Position Control Enabled
This bit will be true (1) when a Position command is
being actioned. This data can be used to indicate that positioning
mode has control of the actuator.
Watchdog Recovery
The MFU watchdog automatically resets the processor if
it is tripped. This bit will be true (1) following a watchdog trip for the
time period set in the associated watchdog timeout parameter.
Note:
Attempting to restart the actuator to move towards the obstruction (even if the
obstruction no longer exists) is not possible, the actuator will not restart. The actuator
must be electrically reversed away from the obstruction before attempting to continue in
the original direction.
Note:
Attempting to restart the actuator to move out of the seated position is not possible. The
actuator must be reversed before it will run in the same direction again. The jammed
seat must first be released manually before electrical control is attempted. The problem
may be overcome by adjusting the actuator torque setting which is designed to provide
extra power on leaving the seated position.