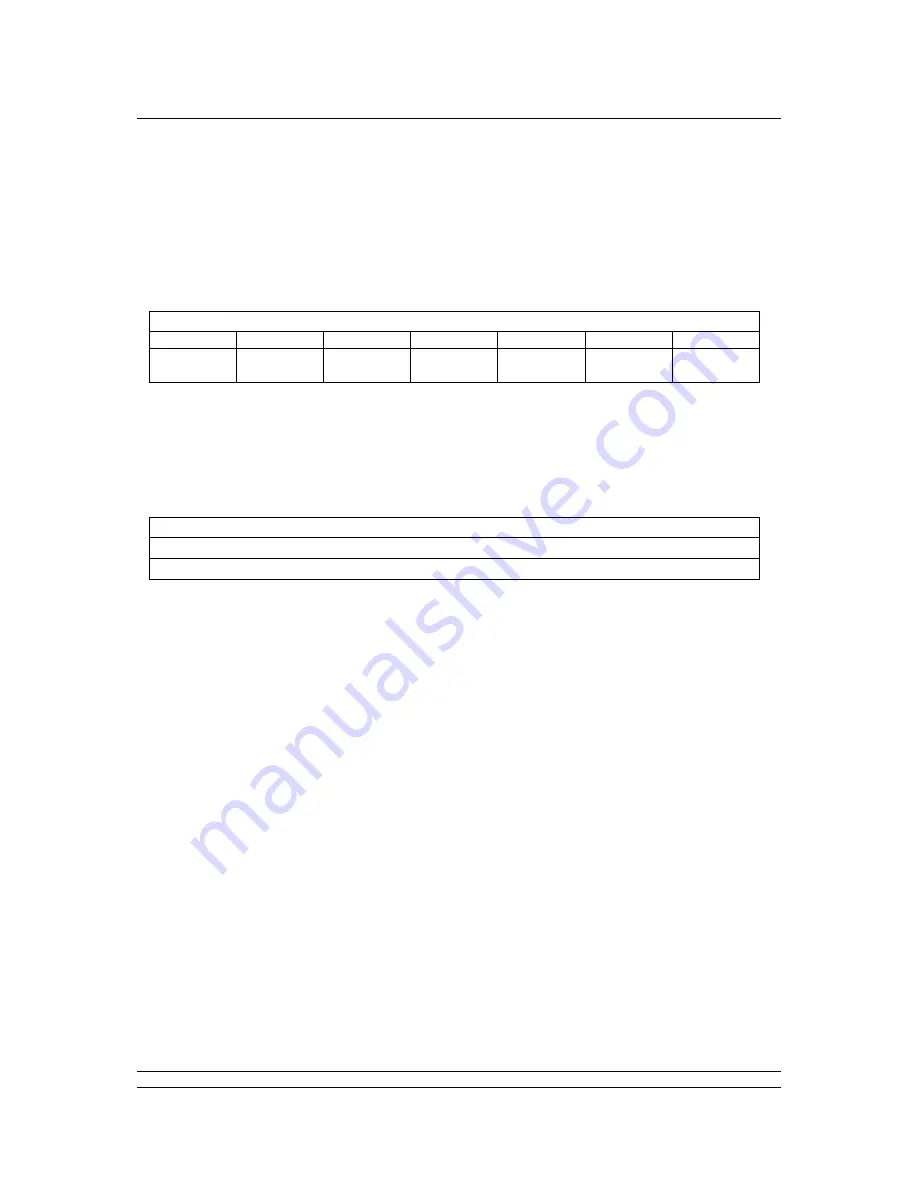
Input and Output Signals
Publication PUB088-005-00_1017
39 of 84
F
ou
nd
ati
on
F
iel
db
us
FF
-01
In
s
tal
lat
io
n m
an
u
al
5.1.2
Profibus Control using the ACTCON Register
A single register is provided to allow the digital control of the actuator. Writing to the individual bits in
the register causes the actuator to open, close, stop, ESD, adopt Positioning mode or perform a
Partial Stroke and at the same time cancels any other command set. The bit written changes any
output states already set to the new value. Only one bit may be written in a command. If more than
one bit is set then the whole register is ignored.
ACTCON Register
Bit 6 - 15
Bit 5
Bit 4
Bit 3
Bit 2
Bit 1
Bit 0
Reserved
Part Stroke
Position
Enable
ESD
Open
Close
Stop
5.1.3
Profibus Control using the POS_DV register
The analogue position control function requires two registers to be set.
A desired position value to move the valve to should be placed in the POS_DV register
The ACTCON register must be set to Position mode ( 0010 hex)
POS_DV Register
Register value: 0 to 1000 (0 to 3E8)
Position demand: 0.0% to 100.0% of valve travel
When the ACTCON register with Position mode set is sent, the actuator will position to the value set in
the POS_DV register and any other commands that are currently being carried out will be cancelled.
If the POS_DV register is set to 0% and limited range positioning is not being used the actuator will
operate as though a ‘close’ command had been sent. Similarly if the POS_DV register is set to 100%
under thes
e conditions the actuator will interpret the instruction as an ‘open’ command.
Note that when limited range positioning is used and the actuator is in the fully closed position a
POS_DV value of 0%, or when the actuator is in the fully open position a POS_DV value of 100%, are
not acted upon.