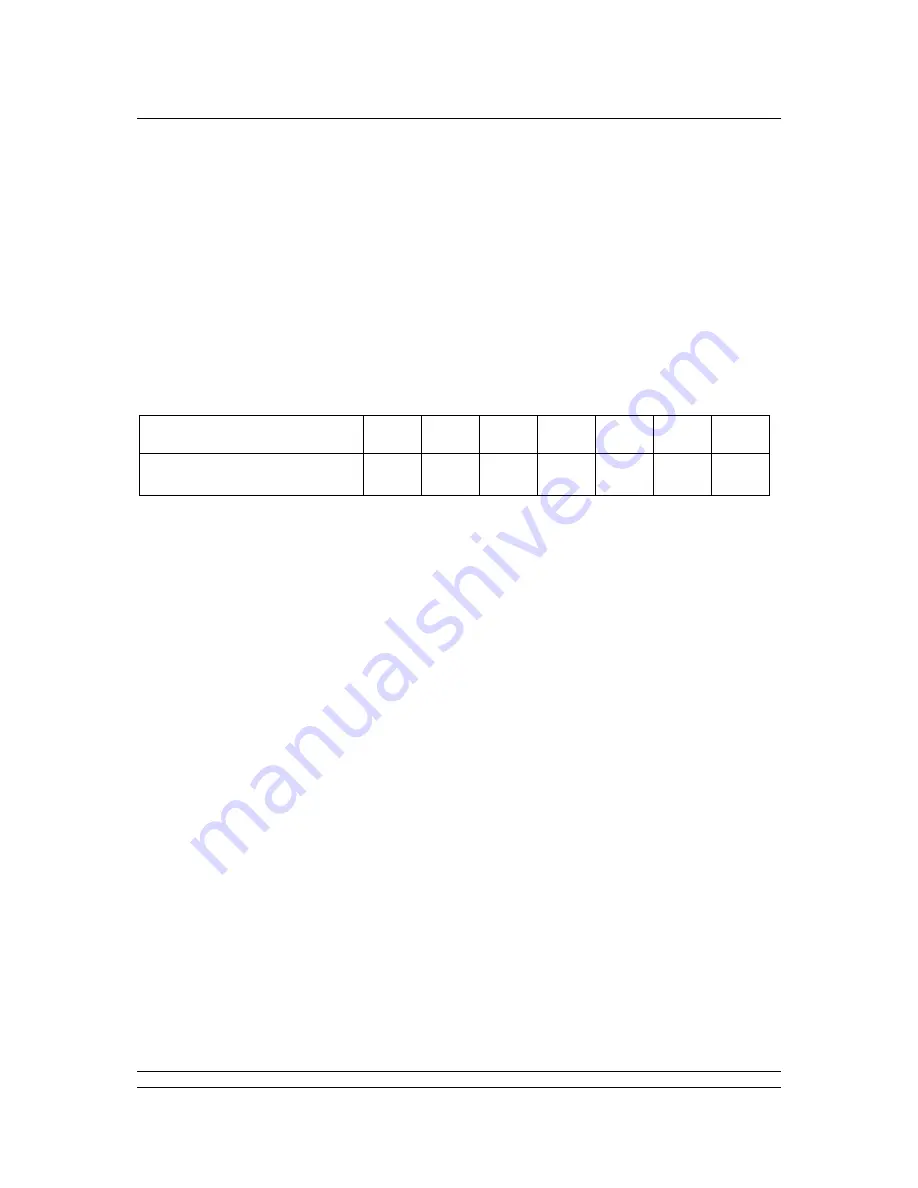
Profibus Communication
Publication PUB088-005-00_1017
51 of 84
F
ou
nd
ati
on
F
iel
db
us
FF
-01
In
s
tal
lat
io
n m
an
u
al
6
PROFIBUS DP COMMUNICATION
6.1 Electrical Specification
Line Electrical Specification:
RS485, two wire, half duplex
6.2 Protocol
Profibus DP
Cyclic (V0) and Acyclic (V1) communication
Supported Baud Rates
9k6, 19k2, 45k45, 93k75, 187k5, 500k, 1M5
Data Speed (Baud)
9k6
19k2
45k45
93k75
187k5
500k
1M5
Maximum Slave Response
Delay Time (mS)
15
15
15
15
15
15
50
6.3 Single Highway, Single Channel
When using a single channel version the following must be set up:
Address
With IQ and IQT actuators the address can be set using the IrDA
communication link directly with the actuator and the IQ setting tool.
For all actuator variants the address can be set over the highway
using a Class 2 master.
Baud Rate
This is selected by the PLC.
Slave Configuration
One of the 10 configurations for the slave must be chosen.
Basic Parameterisation
The basic parameters such as deadband and motion inhibit time can
be set using either the GSD file or a suitable PDM or FDT utility. The
default settings will be suitable for most systems.
Communication will be established automatically between the PLC and the card once the correct GSD
has been identified. If the actuator cover is opened there are several LEDs on the circuit board that
are used to indicate communication activity. These indicate both the communication between the
Profibus highway and the card and the communication within the cards two main processors.