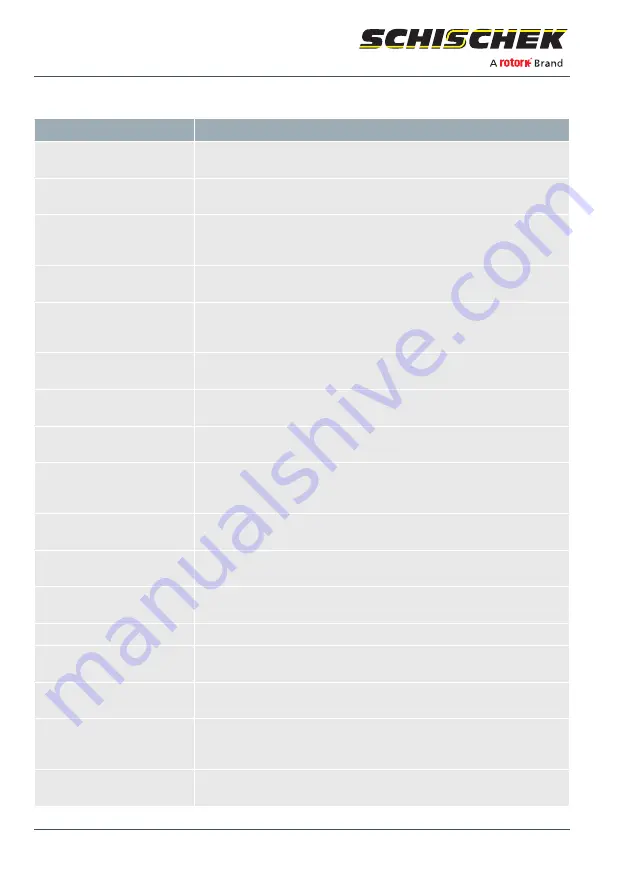
3.11 Accessories
Name
Explanation
Ex/Red/InSwitch
External, upgradeable and locally adjustable auxiliary switch with two
potential-free switch contacts, for retrofitting on ... max rotary drives
Ex/Red/InBox-3P
Terminal box suitable for ... max rotary drives with 1 cable, for OPEN-
CLOSED or 3-point mode
Ex/Red/In-3P/SW
Terminal box suitable for ... max rotary drives with 1 cable, for OPEN-
CLOSED or 3-point mode + 2 cables for external auxiliary switches Ex/
Red/InSwitch
Ex/Red/In-Y/S
Terminal box suitable for ... max rotary drives with 2 cables, for continu-
ous or 3-point mode + integrated limit switches
Ex/Red/InBox-Y/S/SW
Terminal box suitable for ... max rotary drives with 2 cables, for continu-
ous or 3-point mode with fe 2 cables for external auxiliary
switches Ex/Red/InSwitch
Ex/Red/InBox-BF
Terminal box suitable for ... max rotary drives with 1 cable, for all Ex/
Red/In-BF
Ex/Red/InBox-BF/SW
Terminal box suitable for ... max rotary drives with 1 cable, for all Ex/
Red/In-BF + 2 cables for external auxiliary switches Ex/Red/InSwitch
MKK-S, MKK-M
Installation bracket for ... terminal boxes for direct installation on size S
or M rotary drives
KB-S
Clamping device for round damper shaft, diameter 10
mm to 20
mm,
and square damper shaft, 10
mm to 16
mm, incl. rotation lock, suitable
for … size S box rotary drives
KB-A
Clamping device for round damper shaft diameter 1/2
", suitable for
"North America"-… size S box rotary drives
HV-SKU
Manual adjustment with locking mechanism, suitable for size S, short
design
HV-SLU
Manual adjustment with locking mechanism, suitable for size S, long
design for adding ... box or ... switch
HV-MU
Manual adjustment with locking mechanism, suitable for size M
AR-12-xx
Square insert to reduce axle intake from 12
mm × 12
mm to 11
mm,
10
mm, 9
mm or 8
mm (size S)
AR-16-xx
Square insert to reduce axle intake from 16
mm × 16
mm to 14
mm or
12
mm (size M)
Ex/InPro-TT-...
Safety temperature limiter for fire dampers, triggered at 71
°C
/
72
°C,
with 1
m unconnected cable end, only suitable for …Box-BF drives (Ex-
Max, RedMax and InMax models)
EXC-DS1/VA
Safety temperature limiter for duct installation, potential-free contact,
switches at 70
°C…160
°C (in 10° steps)
3 | Device description
188
Translation of the original installation guide · Version 1.0 · 2021-05-27