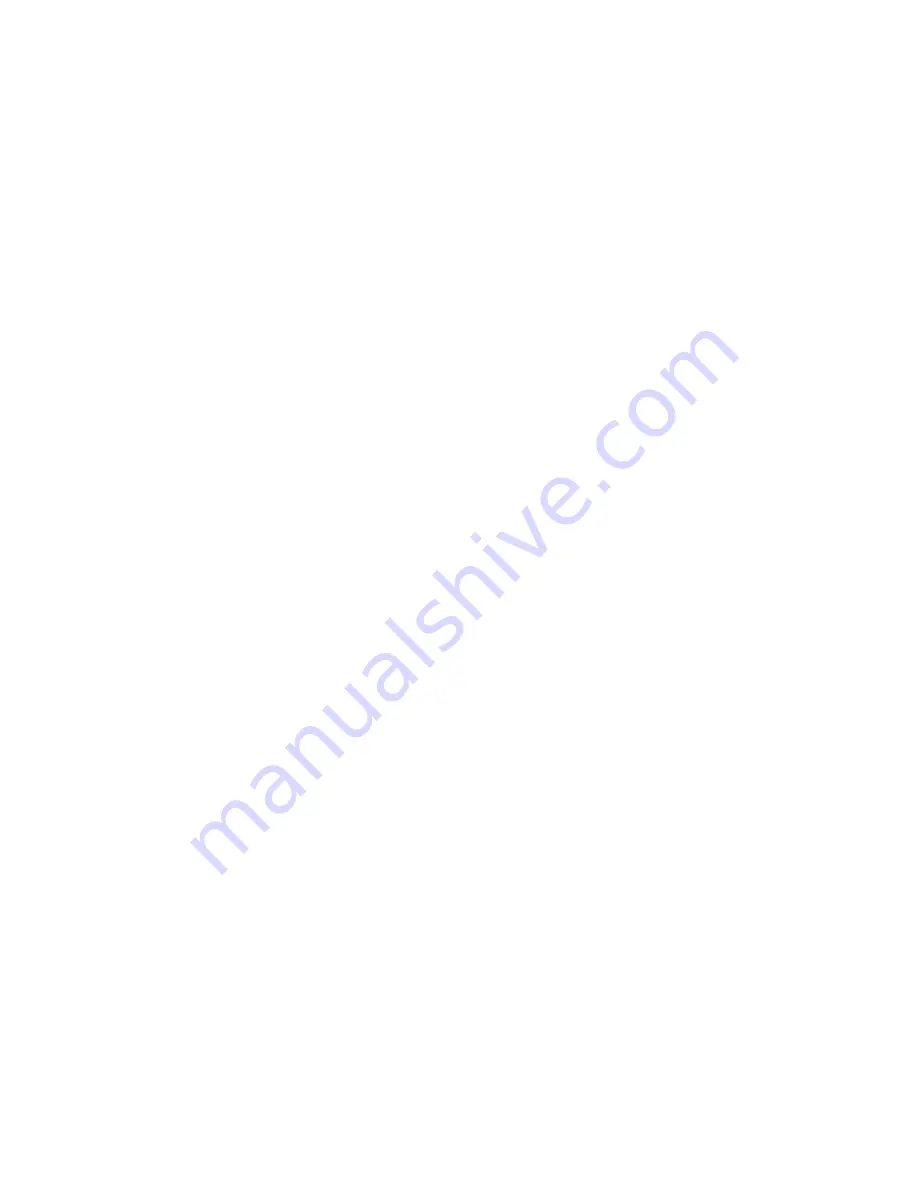
TOOL KIT
The following items are included with your locomotive.
One 60m1 bottle of special steam oil for use in the cylinder lubricator.
One 60m1 syringe with plastic tube for filling the boiler with water.
One water top up pump bottle.
One set of spare washers and ‘0’ rings.
One spare gas jet.
One Allen key for cylinder socket cap screws.
One wheel setting (back to back) gauge and key
(
Manual Blanche & Charles only
).
One pair of protective gloves.
One cleaning duster.
RUNNING IN
All locomotives are test run before leaving the factory, but will require several
hours of running in, when new, to overcome initial tightness and allow valves
etc. to ‘bed in’ completely. It is recommended that the model is run with light
loads for the first few hours of operation. Also, the loco will waste a proportion
of it’s water and steam until ‘run in’ due to leaking slide valves, a tendency to
prime more, and simply overcoming the initial tightness of the moving parts. As
the model heats up and cools down each time you raise steam, screws and nuts
have a tendency to stretch and loosen a little so you will also need to make
regular checks and ‘nip up’ any that become loose. Most are quite visible and
easy to get to however if there is any steam leaking from the valve chests
between the frames, refer to the Trouble Shooting section.
ACCESS TO THE CONTROLS
For normal operation, all controls are accessible without the need to remove any
part of the locomotive, however, for ease of servicing, the cab roof hinges up.
Lift the roof vertically at the front about 12 millimetres, then it will hinge
forward over the front of the cab. The gas regulator is located in the right hand
side of the cab. The boiler top up valve is on top of the boiler under the brass
steam dome. The gas filler valve is located on top of the gas tank in the front
right hand corner of the cab. On manual control engines, the steam regulator is
accessible through the left hand cab doorway, and reversing lever through the
right hand cab doorway.
The displacement lubricator is positioned in the front left hand side of the cab.
The switch for the locomotive r/c equipment is on the front of the tender (FR
Linda version) or coal truck (Penrhyn versions).
The radio control batteries and receiver are housed inside the tender (FR Linda
version) or coal truck (Penrhyn versions). Access to these is by lifting up the
dummy coal load.
4