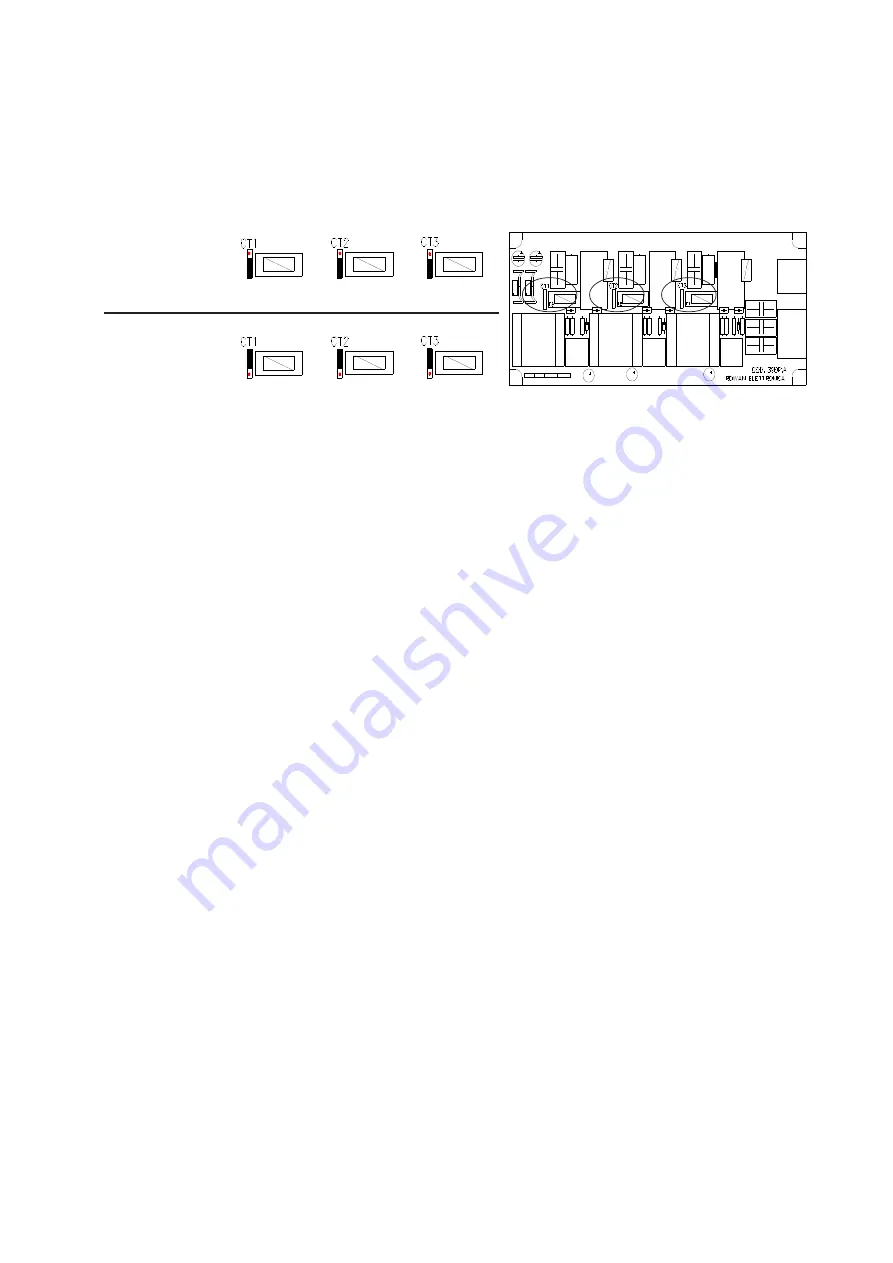
ROWAN ELETTRONICA s.r.l. - Via Ugo foscolo, 20 - 36030 CALDOGNO (Vicenza)
page 11 out of 24
F1
F1
F3
F3
F2
F2
SETTING AT WORKS
PRELIMINARY OPERATIONS:
Before fixing the card, it is convenient to prepare the 3 adjusters according to the supply voltage. It should be kept in mind
that the card comes out of the Rowan laboratories set for the higher range of voltages. To reach the adjusters housed in the
lower card which goes to the power terminal board, the snap on terminals and then the silk screened cover should be
removed. The cover support columns should then be unscrewed, and the upper card which goes to the command terminal
board delicately overturned. The adjusters should be pre-set as follows:
Card pre-set for
1 7 0 V A C ÷ 2 6 0 V A C
supply field
Card pre-set for
3 3 0 V A C ÷ 5 0 0 V A C
supply field
F1 - F2 - F3 0.5 A fuses, controlling protection
The microswitches, trimmers and leds (their functions are explained on pages 6, 7 and 8) can be found on the
upper card, where the rest of the pre-settings are carried out.
To take the card to minimum basic operation (motor speed control from potentiometer), follow these instructions:
Pre-set the S3 micro according to the polarity of the motor to be adjusted
2 pole motor / S3 micro open
4 - 6 pole motor / S3 micro closed
In the case of 6 pole motors, it is further necessary to adjust the P4 trimmer in an anticlockwise direction until the tachimetric
generator produces approx. 5.7 VDC with the potentiometer or DC signal at maximum.
Choose the acceleration and deceleration ramp range:
S2 micro open
P1 trimmer adjustment field (deceleration), minimum 0.02 sec. - max. 2 sec.
P2 trimmer adjustment field (acceleration), minimum 0.02 sec. - max. 2 sec.
S2 micro closed
P1 trimmer adjustment field (deceleration), minimum 0.25 sec. - max. 25 sec.
P2 trimmer adjustment field (acceleration), minimum 0.25 sec. - max. 25 sec.
Connect RUN and STOP IN RAMP as shown in the main connecting diagram on page 4; keep in mind that the two contacts
must be closed to let the motor turn.
Connect the speed adjusting potentiometer (optimal value 10K) to 3 wires of terminals 3 - 6 - 7, open the S1 micro and
close S12; when cursor 6 is towards terminal 7 (6 - 7=0VDC) the motor is stationary; when cursor 6 is towards terminal 3
(6 - 7= -10VDC) the motor turns at maximum speed.
Set the remaining microswitches as follows: S5-S6-S8-S12 closed and S4-S7-S9-S10-S11 open.
Connect the motor card according to the instructions given on pages 8 and 9:
Star or triangle connect according to the line and the motor plate details; earth the motor.
The tachimetric generator signal, which should be connected to terminals 1-2 of the 390S card, should be taken from
terminals 1-2 of the motor terminal board.
The cooling fan supply (230VAC - 50/60Hz) should be taken to terminals 3-4 of the motor terminal board and the motor fan
should not be connected to the motor operation but to the control panel operation. By doing this it is possible to cool the
motor even during rest periods; in motors with threephase cochlear fans connection is carried out directly on the fan base.
The thermal sensor is connected to terminals 5-6 of the motor terminal board. It is a normally closed contact (1A-230VAC),
which should be applied in series to the emergencies - in fact it is inserted directly onto the motor windings and opens if the
temperature reaches the safety limit for tropicalised windings in class H (150°C).
TO MAKE THE MOTOR ROTATE
Adjust the potentiometer so that the cursor connected to terminal 6 is in short with terminal 7.
Supply the card, the motor should be motionless.
The lit L1 (power on) pilot light indicates the presence of supply at the controlling circuits. The L6 running pilot lights up
to indicate that the motor can turn.
Turn the potentiometer. The motor should follow the increase or decrease adjustment with the acceleration and deceleration
ramps set. Verify that the maximum speed is reached, eventually retouch maximum calibration with the P3 trimmer
(MAXIMUM REVS.). Be careful not to exceed the maximum adjustment as this would send the motor into overabsorption,