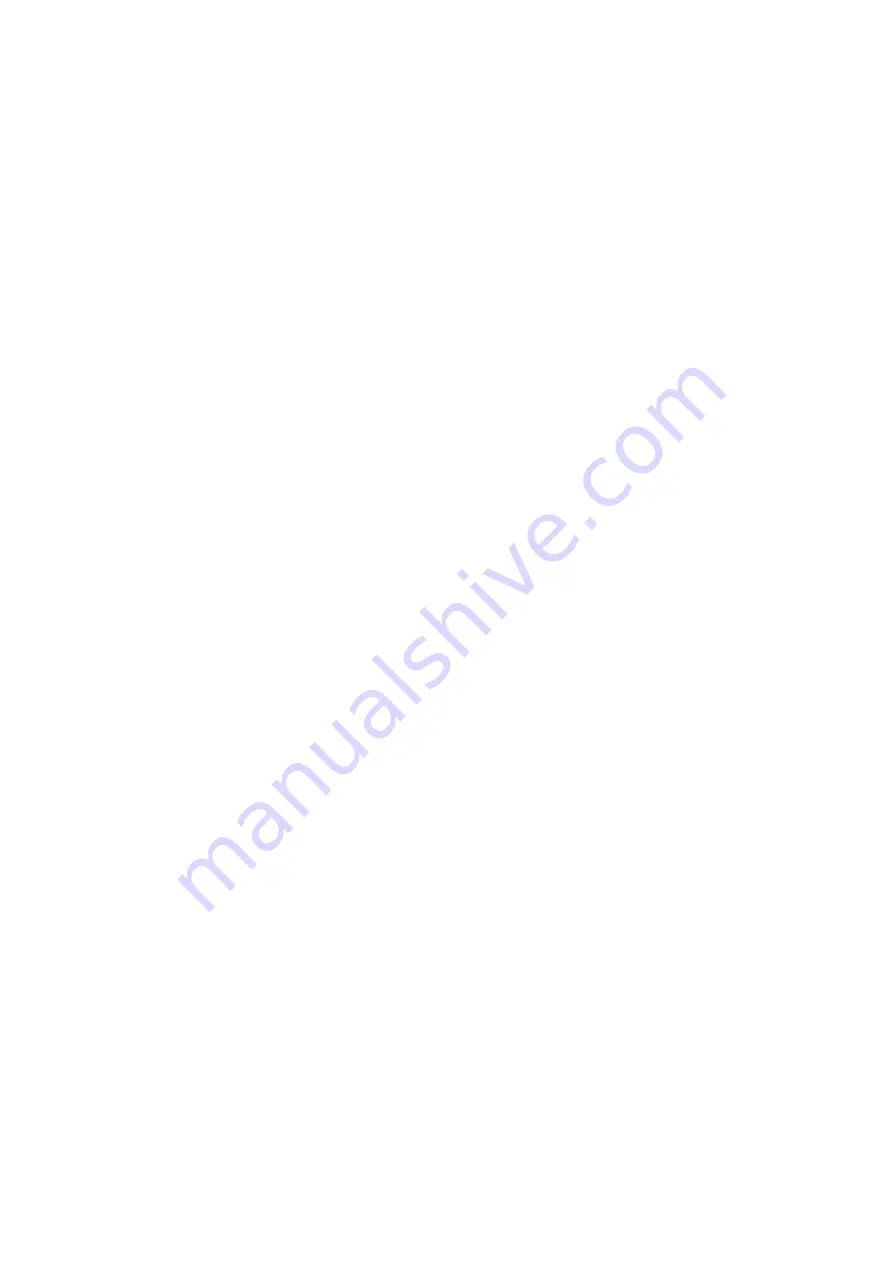
ROYAL ENFIELD WORKSHOP MANUAL
9. Reassembly of Brake Shoes to Cover Plates
Assemble each pair of shoes with their return
springs on to the pivot pin and operating cam,
putting a smear of grease in the grooves of the
pivot pin and on the operating faces of the cam.
Now fit the assembly into the cover plate,
putting a smear of grease on to the cylindrical
bearing surface of the operating cam and secure
with the pivot pin locknut, 28715, and washer,
17551. Fit the operating lever, 38905 or 38906,
on its splines in a position to suit the extent of
wear on the linings and secure with the nut,
10314, and washer, 14613. Note that the
position of the operating levers may have to be
corrected when adjusting the brake after refitting
the wheel. The range of adjustment can be
extended by moving these levers on to different
splines. Limit of wear is reached when the cam
is turned through nearly 90° with the brake hard
on so that there is a danger that the operating
springs cannot return the brake to the off
position.
10. Floating Cam Housings
Note that the cam housings, Part No. 26836,
are intended to be left free to float. The bolt
holes in the cam housings are slotted and the
securing pins, Part No. 252, are provided with
double coil spring washers beneath their heads
to enable them to be tightened sufficiently to
prevent the cam housings moving under the
influence of road shocks, while at the same time
they can be, and should be, left free enough to
be capable of being moved by hand in the
direction of the slots. The pins, 252, are secured
by locknuts, 7916, which are centre punched as
an additional precaution.
The leading shoes (i.e., those towards the rear
of the machine) have a servo action which
renders them more effective than the trailing
shoes. This servo action causes the linings on the
leading shoes to wear more quickly than those on
the trailing shoes and at the same time tends to
lift the leading shoes off the cams and press the
trailing shoes harder on to the cams. With a fixed
cam housing the result is that the majority of the
cam pressure is applied to the less efficient
trailing shoe. By leaving the housing free to float
the cam can follow up the leading shoe thus
maintaining equal pressure between the cam and
the two shoes and so making full use of the more
efficient leading shoe. Owing to the servo action
the wear on the leading shoe with a floating cam
housing is greater than that of the trailing shoe
and in time the limit of float of the cam housing
will be reached, after which the brake will
continue to function as a fixed cam brake with
some loss of efficiency. This can be restored by
removing the shoes and fitting them in the
opposite positions. Floating cam brakes are
self-centering and there is no need to take any
special precautions to see that the two linings
are of equal thickness or that the brake shoe
assembly is centred in the drum.
11. Refitting Brake Cover Plates
After assembling the brake shoe pivot pins
and operating cams into the cover plates repack
the hub bearings with grease. The recommended
greases are Castrolease (Heavy), Mobilgrease
(No. 4), Esso Grease, Energrease C3 or Shell
Retinax A. These are all medium heavy lime
soap or aluminium soap greases. The use of
H.M.P. greases which have a soda soap base is
not recommended as these tend to be slightly
corrosive if any damp finds its way into the
hubs.
Before fitting the distance washers and felt
washers make sure that the inside of the brake
drums are quite clean and free from oil or
grease, damp, etc., and replace the brake cover
plate assemblies. Securely tighten the cover
plate nuts, 31347.
12.
Wheel Rim
The rim is Type WM2-19 in. plunged and
pierced with forty holes for spoke nipples. The
spoke holes are symmetrical, i.e., the rim can be
assembled to the hub either way round. Rim
diameter after building is 19.062 in., tolerances
on the circumference of the rim shoulders where
the tyre fits being 59.930/59.870 in. The
standard steel measuring tape for checking rims
is 5/16in. wide, .011 in. thick and its length is
59.964/ 59.904 in.
13. Spokes
The spokes are of the single butted type 8-10
gauge with 90° countersunk heads, angle of
bend 95°-100°, length 6
5
/
8
in., thread diameter
.144 in., 40 threads per inch, thread form British
Standard Cycle.
14.
Wheel Building and Truing
The spokes are laced one over two and the
wheel rim must be built central in relation to the
nuts which secure the brake cover plates. The
rim should be trued as accurately as possible, the
maximum permissible run-out both sideways
and radially being plus or minus 1/32in.
15. Tyre
The standard tyre is Dunlop 3.25-19in.
Ribbed tread.
When removing the tyre always start close to
the valve and see that the edge of the cover at
the other side of the wheel is pushed down into
the well in the rim.
Section K6 Page 3
www.hitchcocksmotorcycles.com
Summary of Contents for 350 BULLET 1956
Page 7: ...ROYAL ENFIELD WORKSHOP MANUAL w w w h i t c h c o c k s m o t o r c y c l e s c o m ...
Page 57: ...ROYAL ENFIELD WORKSHOP MANUAL w w w h i t c h c o c k s m o t o r c y c l e s c o m ...
Page 69: ...ROYAL ENFIELD WORKSHOP MANUAL w w w h i t c h c o c k s m o t o r c y c l e s c o m ...
Page 77: ...ROYAL ENFIELD WORKSHOP MANUAL w w w h i t c h c o c k s m o t o r c y c l e s c o m ...