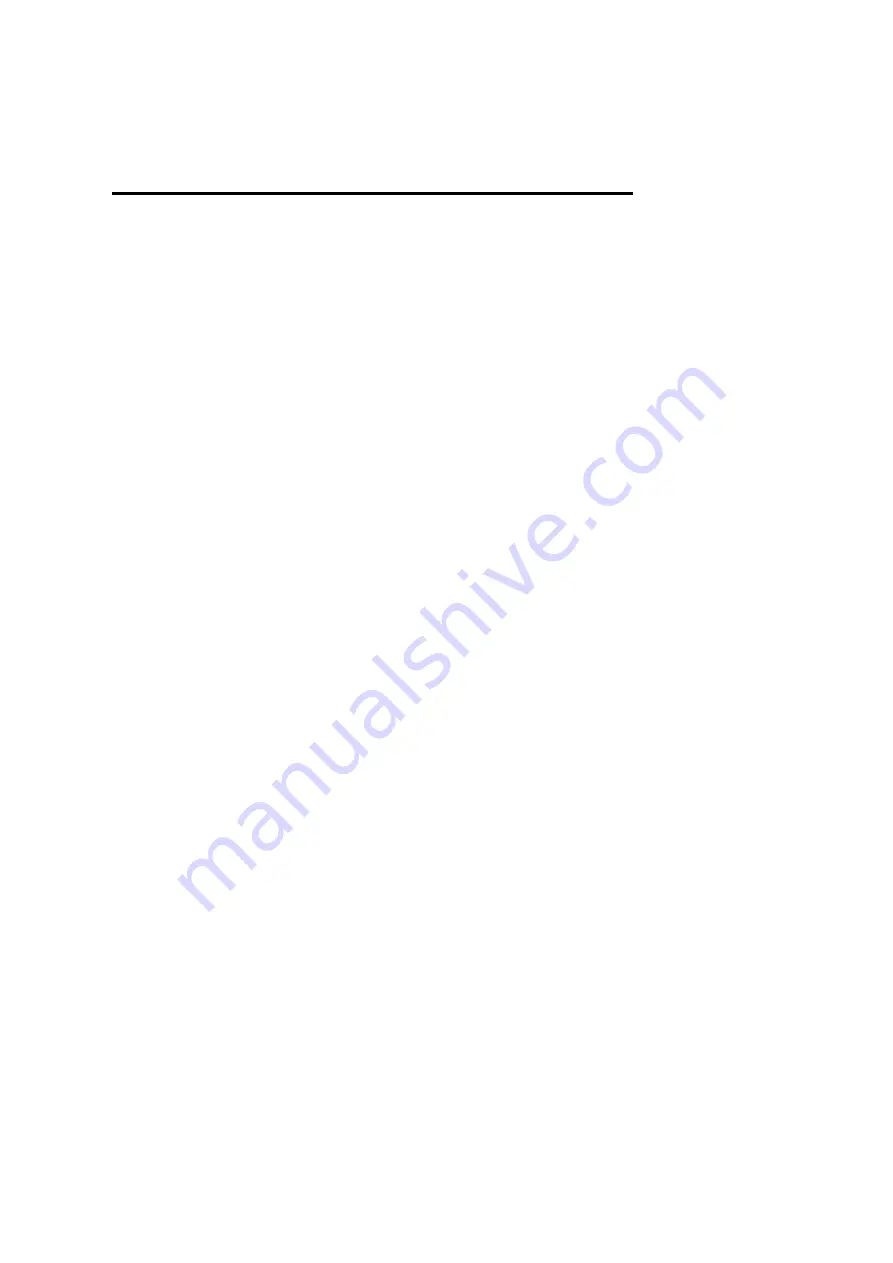
WORKSHOP MANUAL BULLET
Page 104
BULLET 350 CC/500 CC - TORQUE VALUES
ENGINE
ITEM
Kg-m
LB-inch
Rocker Bearing Stud Nut (3/16”)
1.30
112.0
Crank Pin Nut (7/8”)
13.80
1200.0
Timing Shaft Nut (3/4”)
9.20
800.0
Cylinder Head Nut (5/6”)
3.30
285.0
Crankcase Joint Nut (M6 1/4”)
0.90
78.0
Crankcase Joint Nut (M8 5/16”)
1.10
95.0
Gearbox End cover Bolt (1/4”)
1.00
85.0
Alternator Nut (Rotor) (9/16”)
5.50
475.0
Clutch Mounting Nut (9/16”)
5.50
475.0
Main Shaft Nut In Gear Box (5/8”)
6.50
565.0
Rocker Box Stud nut
1.45
125.0
Oil feed and Return Filter Assy.
3.00
260.0
Rocker Oil Pipe Banjo Union
1.00
85.0
Rocker Oil Screwed Bush
1.60
138.0
Oil Feed Plug
1.60
138.0
Oil Cleaner Cap Nut
1.40
120.0
Chain case Front att. nut
1.40
120.0
CHASSIS
Frame Stud Nut-Gear Box (1/2”)
3.20
277.0
Front Engine Plate Stud Nut (1/2”)
3.20
277.0
Rear Engine Plate Stud Nut (Bot.) (3/8”)
2.00
175.0
Rear Brake Cam Lever Nut (7/15”)
2.00
175.0
Chainstay Stud Nut (1/2”)
3.50
300.0
Front Fork End Cap Nut (5/16”)
1.30
112.0
Rear Wheel Lock Nut (M22)
7.50
650.0
Rear Wheel Spindle Castle Nut (M16)
6.50
565.0
Rear Shock Absorber Upper (3/8”)/Lower Nut (3/8”)
2.50
215.0
Front Mudguard Stay Screw Nut (1/4”)
0.30
25.0
Front Engine Plate Stud Nut (M8)
1.50
130.0
Front Mudguard Stay Stud Nuts (5/16”)
1.20
104.0
Handle Bar Clip Bolt (5/16”)
3.30
286.0
Handle Bar Clip & Seat Stud Nuts (5/16”)
2.40
208.0
Main Footrest Nuts (3/8”)
1.20
104.0
Coil Fixing Bolt and Nuts (M6)
0.45
40.0
Regulator Fixing Nut (M6)
0.45
40.0
Rear Mudguard Carrier Stud Nut (Top) (3/8”)
2.00
175.0
Rear Mudguard Carrier Stud Nut (Bottom) (7/16”)
2.50
216.0
Rear Engine Plate Stud Nut (M8)
1.50
130.0
Eye Bolt Stud Nut (5/16”)
1.50
130.0
Tank Fixing Nut (3/8”)
1.60
140.0
www.hitchcocksmotorcycles.com
Summary of Contents for 350 BULLET 1989
Page 9: ...WORKSHOP MANUAL BULLET Page 9 w w w h i t c h c o c k s m o t o r c y c l e s c o m ...
Page 17: ...w w w h i t c h c o c k s m o t o r c y c l e s c o m ...
Page 34: ...WORKSHOP MANUAL BULLET Page 34 w w w h i t c h c o c k s m o t o r c y c l e s c o m ...
Page 37: ...w w w h i t c h c o c k s m o t o r c y c l e s c o m ...
Page 41: ...WORKSHOP MANUAL BULLET Page 41 w w w h i t c h c o c k s m o t o r c y c l e s c o m ...
Page 58: ...WORKSHOP MANUAL BULLET Page 58 w w w h i t c h c o c k s m o t o r c y c l e s c o m ...
Page 69: ...WORKSHOP MANUAL BULLET Page 69 w w w h i t c h c o c k s m o t o r c y c l e s c o m ...
Page 73: ...w w w h i t c h c o c k s m o t o r c y c l e s c o m ...
Page 77: ...w w w h i t c h c o c k s m o t o r c y c l e s c o m ...
Page 103: ...w w w h i t c h c o c k s m o t o r c y c l e s c o m ...
Page 105: ...w w w h i t c h c o c k s m o t o r c y c l e s c o m ...
Page 107: ...WORKSHOP MANUAL BULLET Page 107 w w w h i t c h c o c k s m o t o r c y c l e s c o m ...
Page 108: ...WORKSHOP MANUAL BULLET Page 108 w w w h i t c h c o c k s m o t o r c y c l e s c o m ...
Page 109: ...WORKSHOP MANUAL BULLET Page 109 w w w h i t c h c o c k s m o t o r c y c l e s c o m ...
Page 110: ...WORKSHOP MANUAL BULLET Page 110 w w w h i t c h c o c k s m o t o r c y c l e s c o m ...
Page 111: ...WORKSHOP MANUAL BULLET Page 111 w w w h i t c h c o c k s m o t o r c y c l e s c o m ...
Page 113: ...WORKSHOP MANUAL BULLET Page 113 w w w h i t c h c o c k s m o t o r c y c l e s c o m ...