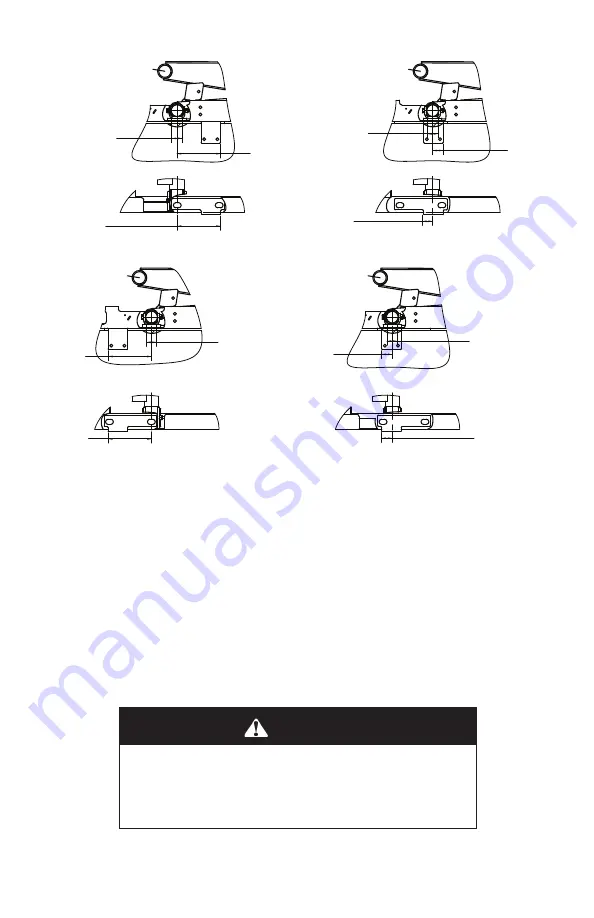
14
1841488G
April 2022
------------------------------- OR ---------------------------------
2.00
CRITICAL
WELD AREA
2.00
MIN
2.00
MIN
8.25
MAX
2.00
CRITICAL
WELD AREA
8.25
MAX
8.25
MAX
8.25
MAX
2.00
CRITICAL
WELD AREA
2.00
CRITICAL
WELD AREA
2.00
MIN
2.00
MIN
Figure 7:
Mounting Angle Location
2. Locate the ideal mounting angle location along the chassis frame
while keeping within the guidelines shown in Figure 7. Ensure the
weld from the sub-frame to the mounting angle will be positioned
directly below the saddle tube.
NOTE:
Optional 10 gauge rivet spacers may be positioned under the
mounting angle and the rear hinge angle to clear rivets on the truck
frame.
DANGER
Welding, oxy-fuel cutting, or grinding sparks can cause
fuel to ignite which in turn can lead to injury or death.
Always take adequate steps to avoid ignition of fuel
tanks during equipment installation.