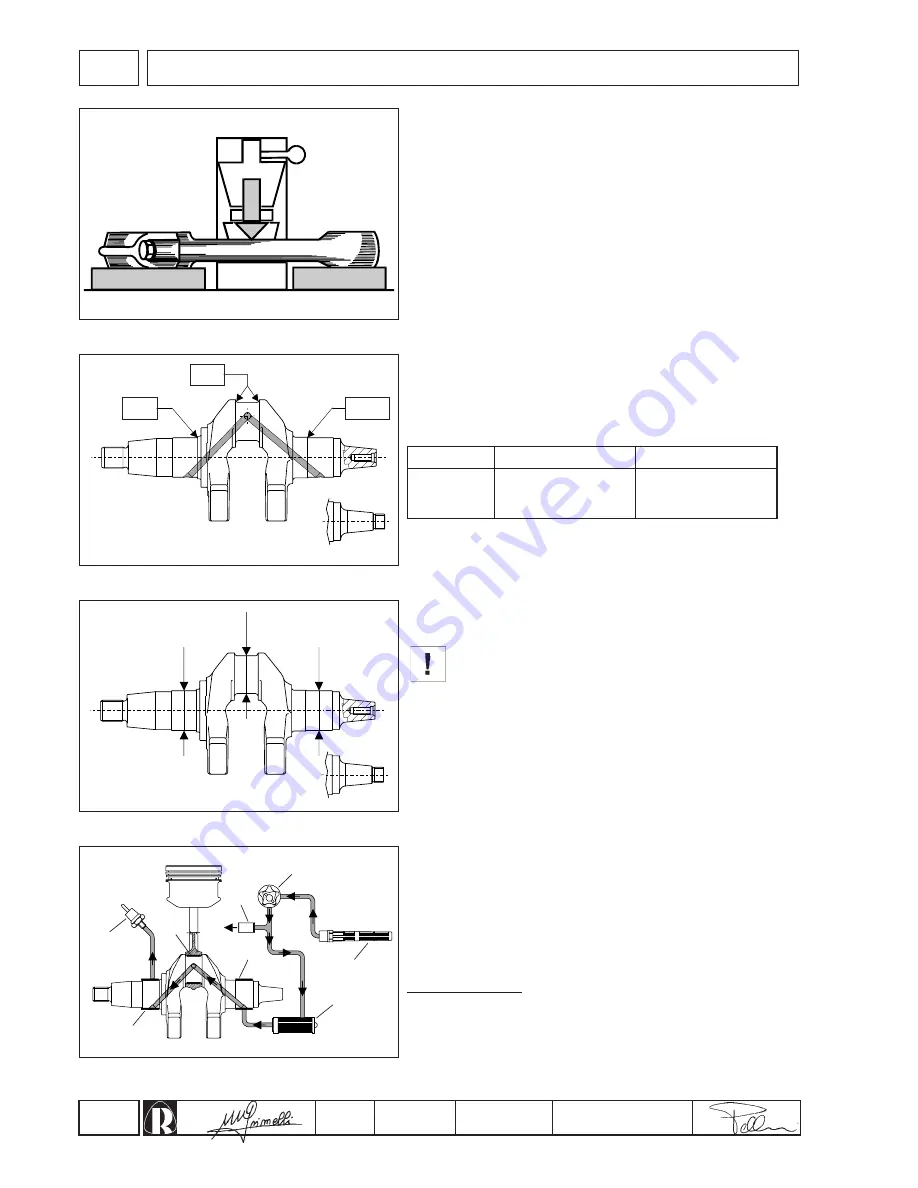
22
COMPILER TECO/ATI
ENDORSED
DATE
29.02.2004
REG. CODE
1-5302-633
MODEL N°
51074
DATE OF ISSUE
02-04
REVISION
00
X
20
21
22
23
5
C
A
B
R 1
R 0,5
R 3
3
2
1
4
7
6
6
A C
B
-0,25 mm
41,72 ÷ 41,74
39,73 ÷ 39,75
STD mm
41,97 ÷ 41,99
39,98 ÷ 40
CHECKS AND OVERHAUL
Dimensions
The operation is carried out by applying a calibrated pressure to the
convex side in the middle of the connecting rod stem set on surface
plates (fig. 20).
Crankshaft
It is advisable to check the condition of the crankshaft whenever the
engine is demounted and particularly when cylinders and pistons
must be replaced following wear due to dust having been intaken.
Thoroughly clean inside the oil ducts using a shaped metal point.
If there are heavily caked incrustations, immerse the crankshaft into
a bath of petroleum or gasoline before proceeding with the scraping
operation (fig. 21).
When the crankshaft is perfectly clean, check with a micrometer to
ascertain wear and main journal ovality in the two perpendicular
positions (fig. 22).
Grind the shaft if the wear exceeds the values in the table by 0.08
mm or more.
Undersized bearings can be mounted without any reaming work
required.
WARNING
: do not remove material from the main journal
shims during the grinding operation as this would alter
crankshaft float. Also make sure that the grinder radii
correspond to those indicated in fig. 21 to prevent fracture
sections from initiating on the shaft.
Oil retention rings
Make sure that the rings have not hardened in the retention lip and
that there is no sign of breakage or wear.
Lubrication circuit
Lubrication of the main bearings and connecting rod big end is the
forced type with a rotor oil pump.
Excessive pressure in the oil circuit is prevented by the by-pass
valve (3, fig. 23).
All the other parts are splash lubricated.
Oil vapours are eliminated from inside the casing by a diaphragm
mounted in the rocker arm cover.
Illustration in fig. 23:
1. Internal intake oil filter in casing - 2. Oil pump - 3. By-pass valve -
4. Engine oil filter - 5. Pressure switch - 6. Main bearing - 7. Big end
bearing.
NOTE: crankshaft grinding operations of more than 0.25 mm
should not be carried out.