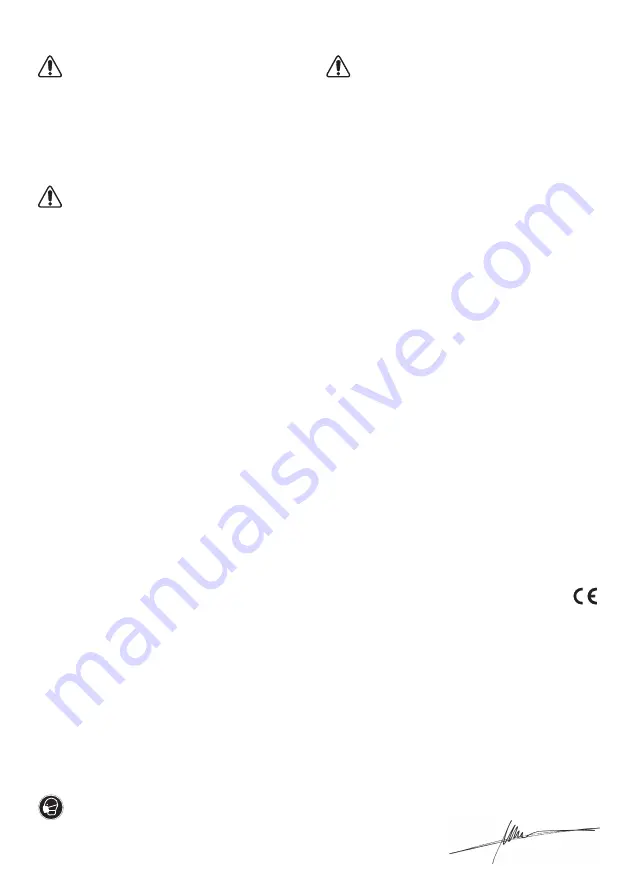
9
SETTINGS
Before carrying out any work on the tool, always disconnect
it from the compressed air supply.
SELECTING THE RPM
The number of revolutions can be adjusted by using the speed
control (3) from OFF to MAX.
The choice of speed depends on the characteristics of the abrasive
paper discs and the material to be worked.
REMOVING AND MOUNTING THE BACKING PAD
Immediately replace a damaged pad. Optimal results can only
be achieved with original accessories.
Mounting a pad of the wrong size can cause excessive vibrations
not acceptable for the machine.
- Use the spanner (12) to unscrew the back-up pad screw (10);
- reverse the procedure when fitting the pad screw.
FITTING / REPLACING THE ABRASIVE PAPER DISCS
The pad surface is made of material suitable for receiving the
abrasive paper discs and provides easy and quick adhesion of
abrasive paper discs.
FITTING:
- Press the abrasive paper disc into the pad ensuring that the holes
in the abrasive paper disc coincide with extraction holes in the pad.
REPLACING:
- Used abrasive paper disc can be removed by simply tearing them off
- New abrasive paper disc is mounted by simply pressing them into
the backing pad, making sure that the holes cut in the disc coincide
with those in the backing pad
Note:
for optimal adhesion it is recommended to remove dust and
dirt from the pad surface.
USABLE DISCS
Ø 125 mm - Ø mm 150 backed abrasive paper discs with dust
extraction holes.
BEFORE STARTING THE TOOL
Ensure that:
- the speed control (3) is in MAX position
- the compressed air feed line and connection are in perfect working
order
- the start lever is working properly. This must be done with the air
supply switched off
- all the components of the tool are mounted correctly and do not
show any signs of damage
- the tool must be connected to a suitable and efficient aspiration
device (SERIES RH..A and RH..T)
TEST RUN
- Start the tool and check that there are no unusual vibration, the
abrasive paper discs are applied correctly (see FITTING / REPLA-
CING THE ABRASIVE PAPER DISCS)
Otherwise switch-off the tool immediately and eliminate the
cause.
- Fix the piece you are working on to avoid any movement during
machining.
Always use a mask for jobs generating dust.
MAINTENANCE
All maintenance operations are carried out with the tool
disconnected from the compressed air supply.
Maintenance and repair operations must be carried out by qualified
personnel.
At the end of each work session, or when required, remove any dust
from the body of the tool using a jet of compressed air.
ORDINARY MAINTENANCE
Lubricate the machine regularly (every 50 hours of operation) by
inserting 2/3 drops of specific oil (11) into the compressed air
connection, keeping the device in a vertical position, with the
connection facing upwards. After this operation, connect the
machine to air compressor and set it in motion for a few seconds.
Lubricate the machine as described above before storing it for long
periods of inactivity.
All damages deriving from incorrect or inadequate lubrication are
excluded from the warranty.
No other maintenance operations must be undertaken by the user
.
Maintenance and cleaning of the inner parts, must be carried out
only by an authorized customer-service workshop.
Use only RUPES original spare parts.
GUARANTEE
All tools manufactured by RUPES Spa are guaranteed for 12 months
from the date of purchase against fabrication and material defects.
All tools must be used only with RUPES original accessories and
spare parts: we refuse all responsibility for damages or accidents
caused by non-observance of this rule which will also cause the
termination of the guarantee.
The guarantee will no longer be valid if the instructions contained in
this booklet are not followed, if the tool is used for purposes other
than that for which it is intended, if it is dismantled, interfered with
in any way or damaged due to neglect.
The guarantee will be made valid by filling-in the form on the inside
back cover of this instruction booklet.
If the tool is found to be defective or malfunctions, it should be
returned carriage free in one piece in its original packing together
with the guarantee certificate to the manufacturer or to one of the
Assistance Centres. The guarantee does not automatically imply
replacement of the tool.
RUPES Spa reserves the right to make any technical or design
modification to its products without prior notice. The manufacturer
is not liable for any print errors. This document voids and replaces
previous ones.
CONFORMITY DECLARATION
We declared on our responsibility that the hand-held non-electric
power tool, which is mentioned in the present operating manual, is
in conformity with the Essential Requirements of Safety of the
following Directive:
2006/42/CE
Machinery
The tests have been carried out in accordance with following
Standards:
UNI EN ISO 11148-8 - UNI EN ISO 15744 - UNI EN ISO 28927
Technical file at:
RUPES S.p.A.
Via Marconi, 3A
20080 VERMEZZO (Mi) - Italy
Vermezzo (MI), 01/03/2014
RUPES S.p.A.
IL PRESIDENTE
G. Valentini