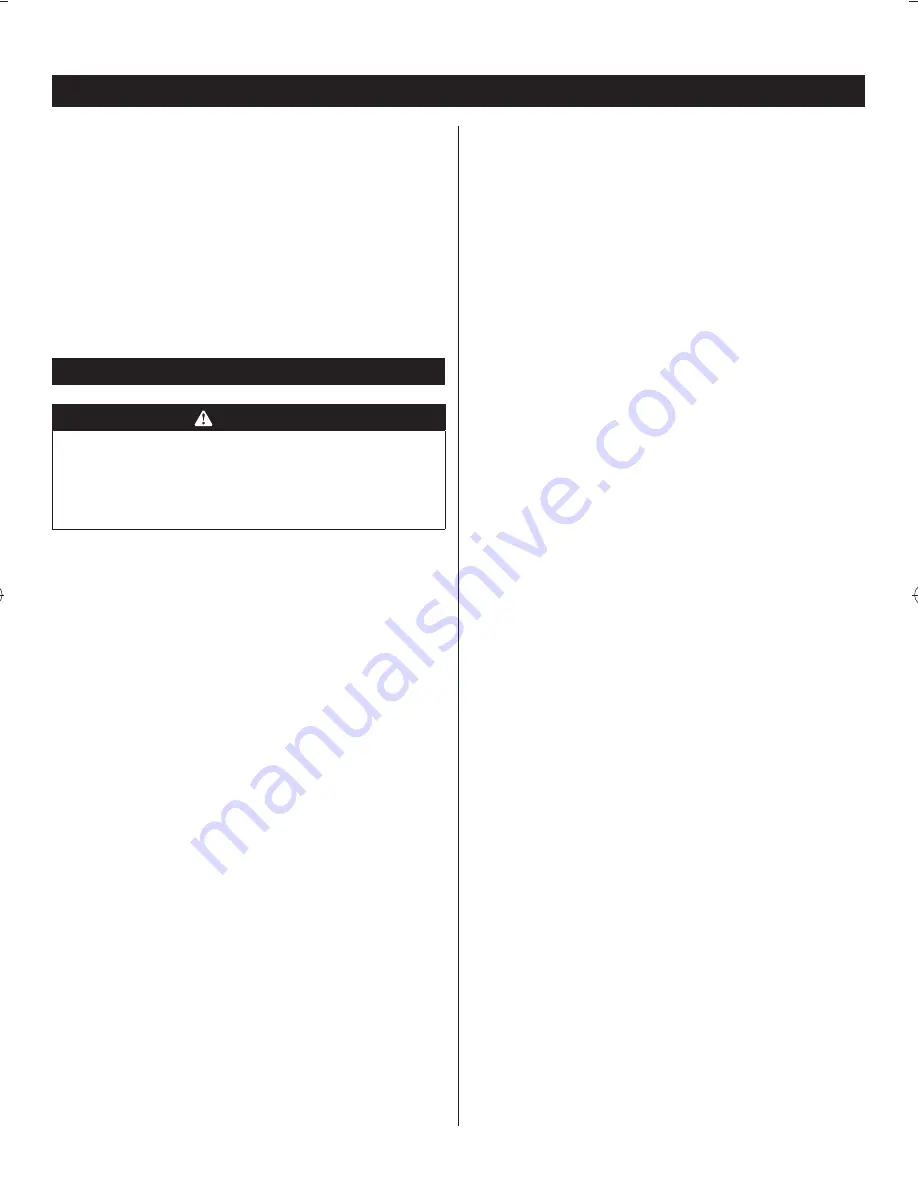
3
English
strainer and clean it.
■
When not in use, disconnect from air supply, clean tool
and store in a safe, dry, childproof location.
■
If the tool cannot be used anymore, make sure to
dispose of it so as not to impose hazards to people
and the environment.
■
Always keep your air tool clean and lubricated. Daily
lubrication is essential to avoid internal corrosion and
possible failure.
■
Only lubricants (air tool white oil) recommended by the
manufacturer should be used.
TROUBLESHOOTING
WARNING
If any of the following symptoms appears during your
operating, stop using the tool immediately, or serious
personal injury could result. Only quali
fi
ed persons or
an authorized service center can perform repairs or
replacement of tool.
Disconnect tool from air supply before attempting repair or
adjustment. When replacing O-rings or cylinder, lubricate
with air tool oil before assembly.
PROBLEM: Tool runs at normal speed but fails under
load.
POSSIBLE CAUSES
■
Motor parts worn.
■
Cam clutch worn or sticking due to lack of lubricant.
REMEDIES
■
Lubricate clutch housing.
■
Check for excess clutch oil. Clutch cases need only
be half full. Overfilling can cause drag on high speed
clutch parts, ie. a typical oiled/lubricated tool requires
14.20 mL (1
⁄
2 ounce) of oil.
Grease lubrication
NOTE:
Heat usually indicates insufficient grease in
chamber. Severe operating conditions may require
more frequent lubrication.
PROBLEM: Tool runs slowly. Air fl ows slightly from
exhaust.
POSSIBLE CAUSES
■
Motor parts jammed with dirt particles.
■
Power regulator in closed position.
■
Air flow blocked by dirt.
REMEDIES
■
Check air inlet filter for blockage.
■
Pour air tool lubricating oil into air inlet as per
instructions.
■
Operate tool in short bursts quickly reversing rotation
back and forth where applicable.
■
Repeat above as needed.
PROBLEM: Tool will not run. Air flows freely from
exhaust.
POSSIBLE CAUSE
One or more motor vanes are stuck due to material
build up.
REMEDIES
■
Pour air tool lubricating oil into air inlet.
■
Operate tool in short bursts of forward and/or reverse
rotation where applicable.
■
Tap motor housing gently with plastic mallet.
■
Disconnect supply. Free motor by rotating drive shank
manually where applicable.
PROBLEM: Tool will not shut off.
POSSIBLE CAUSE
‘O’ rings throttle valve dislodged from seat inlet valve.
REMEDY
Replace ‘O’ ring .
NOTE:
Repairs should be carried out by a quali
fi
ed
person.