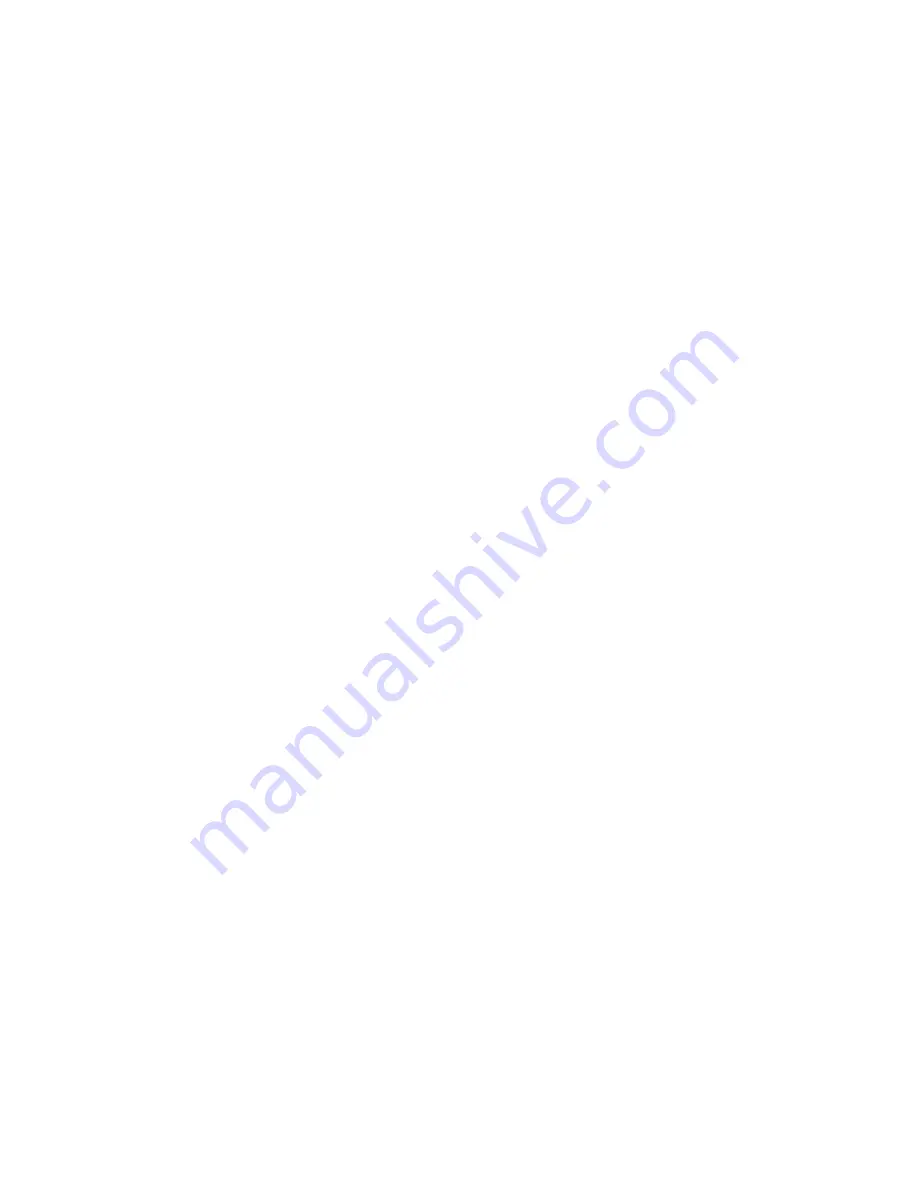
1.
We’ve seen Schlage C key blanks with variations of up to 15 thousandths of an inch (.015”)
between top and bottom shoulder positions – between keys taken from the same box. It happens more
often than you think. The solution? Don’t bottom shoulder gauge your keys anymore.
Cutter Stalls Out
There are six possible causes for this problem.
1.
You are cutting keys from Tip-to-Bow. This one can fool you if you’re not careful. Cutting keys
from tip to bow will work when you cut only shallow keys—sometimes a shop can cut keys all day long
and never hit upon a key with a deep cut. You think everything is O.K. when all of a sudden your cutter
stops dead halfway along the key. The problem? The deep cut put the cutter into the key past the cutter
tooth area on the left side of the cutter—you just reinvented the disk brake!
SOLUTION—ALWAYS
CUT FROM BOW-TO-TIP.
2.
Oil on the belt and pulleys. Clean the pulleys with safety solvent and install a new drive belt.
3.
Left-hand nut securing the cutter wheel isn’t tight.
4.
Belt tension needs to be increase and/or replaced the drive belt.
5.
You’re in your service vehicle. You’re Redi-Line generator needs repair, or your wiring needs
replacing (usually from the battery to the Redi-Line), or your battery is weak. Another possibility is that
you’ve been using a power converter and it is marginal.
6.
Your cutter wheel is really dull.
Stylus Shaves Material Off Key
The situation is caused by the fact that the cutter wheel is made to a sharp point and therefore to cut keys
accurately the stylus must also be made with a sharp edge. A key blank dragged across a sharp edged
stylus has no choice but to scrape material from the key blank. The solution is to lightly “blunt” the sharp
edge of the stylus. This has to be done carefully because if the edge of the stylus is blunted to much you
will narrow the width of the pin seat somewhere in the middle—if the stylus is sharp it will scrape the key
to much, if the stylus is blunted to much it will produce a duplicate key with a slightly narrower pin seat
area.
If you’re going to cut more than 5 or 10 duplicates off one key we recommend that you make “first”
generation keys and then make additional duplicates off of them. For example if you had to make 50
duplicates off the same key you should make 5 or 10 “first” duplicates and make 5 or 10 duplicates off of
each of them. This is a classic example of why your key machine should always be maintained in perfect
depth and space adjustment.
Cutter Leaves Ridges on Cut Key
This situation is related to the example above. The cutter wheel is made with a dead-sharp edge or point.
You will always get ridges on the cut stylus wears—until finally you have to buy a new cutter or get the
old cutter resharpened or replace the stylus. When you put on the new or resharpened cutter or stylus
you’re back to ridges again.
Machine Makes Whirring Sound
There are four possible causes.
1.
The sound is coming from the motor. With the machine turned OFF-grab the motor shaft and try
to get some movement out of tit when trying to move the shaft up and down. If there is up and down
movement the motor ball bearings are worn and the motor will need replacement some time in the future.
Please ignore any motor shaft play when pushing or pulling the shaft along its length in and out of the
motor—this play is in the motor’s spring preloaded ball bearings and is not a sign of bearing wear.
2.
Your drive belt is coming apart or is frayed. Replace it.
Your ball bearing cutter wheel shaft assembly is wearing out. With the machine turned OFF—grab the cutter
wheel’s left-hand nut and try to get some movement out of it. There should be absolutely no movement—if
16