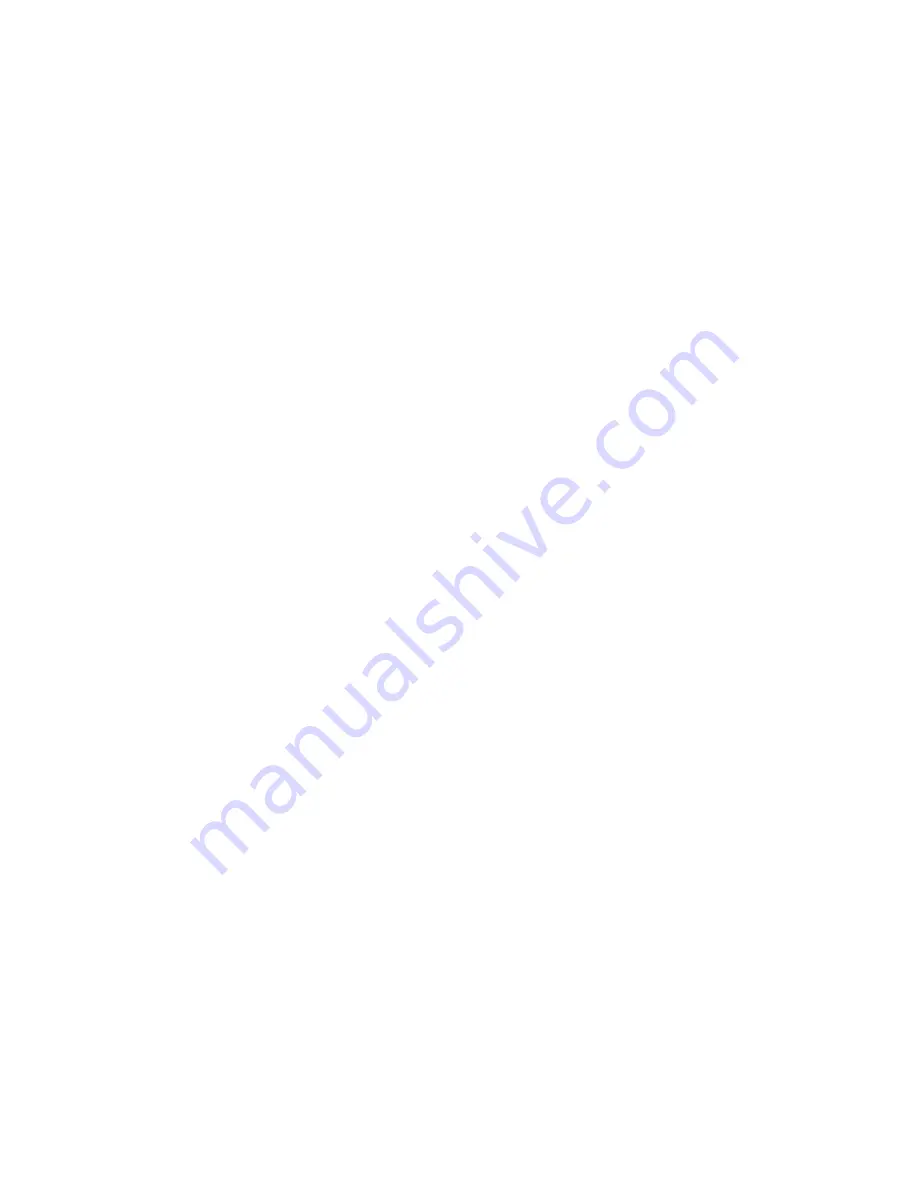
Reinstall the “stick-shift” and drive shaft assembly and reattach the two piece drive shaft linkage and
you’re almost done.
Turn the machine back onto its feet and observe the carriage spring attached to the ¼” diameter grooved pin
driven into the carriage shaft. Take your small hammer and a steel rod or drift and drive the pin back into
the carriage shaft. Stop when the bottom edge of the carriage spring almost touches the carriage shaft.
Test the operation of the carriage and the “feel” of the carriage spring. If the carriage spring seems a bit to
strong – drive the grooved spring pin retaining pin in a little bit further. If the carriage seems a bit too weak
- drive the grooved spring retaining pin up (from the bottom of the machine) a little bit further. Test the
carriage again.
The Carriage Shaft and Bronze Oilite® Bearings
Refer to the first part of The Carriage Spring to disconnect the linkages and remove the “stick-shift” lever
assembly and the carriage spring. Remove the linkages form the carriage shaft using a 1/8” Allen Hex
Wrench to remove the shoulder bolt.
Drive the ¼” diameter carriage shaft pin used to retain the carriage and the carriage pin.
Look down onto the carriage shaft from the top of the carriage and lightly file the ¼” diameter hole where
the grooved pin was - the knurled section of the pin probably raised up small burrs on the edge of the hole
which might damage the carriage when the shaft is pulled out of the carriage. Also turn the carriage shaft
and expose the milled notch in the carriage shaft where the carriage release mechanism locked the carriage
back. The constant locking back and unlocking of the carriage probably raised up a burr on the shaft at the
edge of the milled notch – remove any burr you may find in this area with your file before trying to remove
the carriage shaft.
Pull out the Carriage Shaft.
Use a piece of 1” diameter hard wood dowel purchased from your local hardware store. Cut off a piece
about 6” long and use it to pound out the bearings with a hammer.
Cut off a piece of 1” diameter hard wood dowel about1 foot long and trim one end to ¾” diameter about ½”
long - to fit onto the new bronze Oilite® bearing.
From the right side of the machine push the 1” hardwood dowel through the 1” diameter bearing hole – go
almost all the way through to the left side of the machine where the first bearing will be installed. Slip the
new bronze Oilite® bearing onto the modified end of the dowel and position the bearing onto the 1”
diameter hole. Notice the dowel pin going through the first hole and the bearing sitting at the entrance of
the 1” diameter hole act on their behalf for their own alignment. Use your hammer to pound on the end of
the dowel and drive the bronze Oilite® bearing into its hole. Remove the dowel and insert the new carriage
shaft – leave the end of the carriage shaft extended about ½” out of the right-side bearing hole and place
your second bearing onto this shaft. Notice that the carriage shaft now acts as an alignment guide for the
second bearing. Use your 6” piece of 1” diameter hardwood dowel and your hammer to pound in this
bronze Oilite ® bearing.
Test to see if the new carriage shaft slides between the two bearings. If you were careful and pounded them
in straight you should be able to continue with the rest of the reassembly right away. If the carriage shaft is
just a little stiff you can probably leave it alone and let it work itself in over time. If the carriage shaft
seems to be tight then use a medium size plastic mallet and tap on the shaft in all directions accessible to
“settle” in the bearings. Stop when the carriage shaft gets just loose enough to use.
Reassemble in the reverse order and refer to section in this manual titled HOW DO I REPLACE. .
The Carriage Spring and complete your assembly.
You should recheck the depth, depth overtravel and space adjustments on your machine and readjust as
necessary.
WHY DID WE DO IT THAT WAY . . .
20