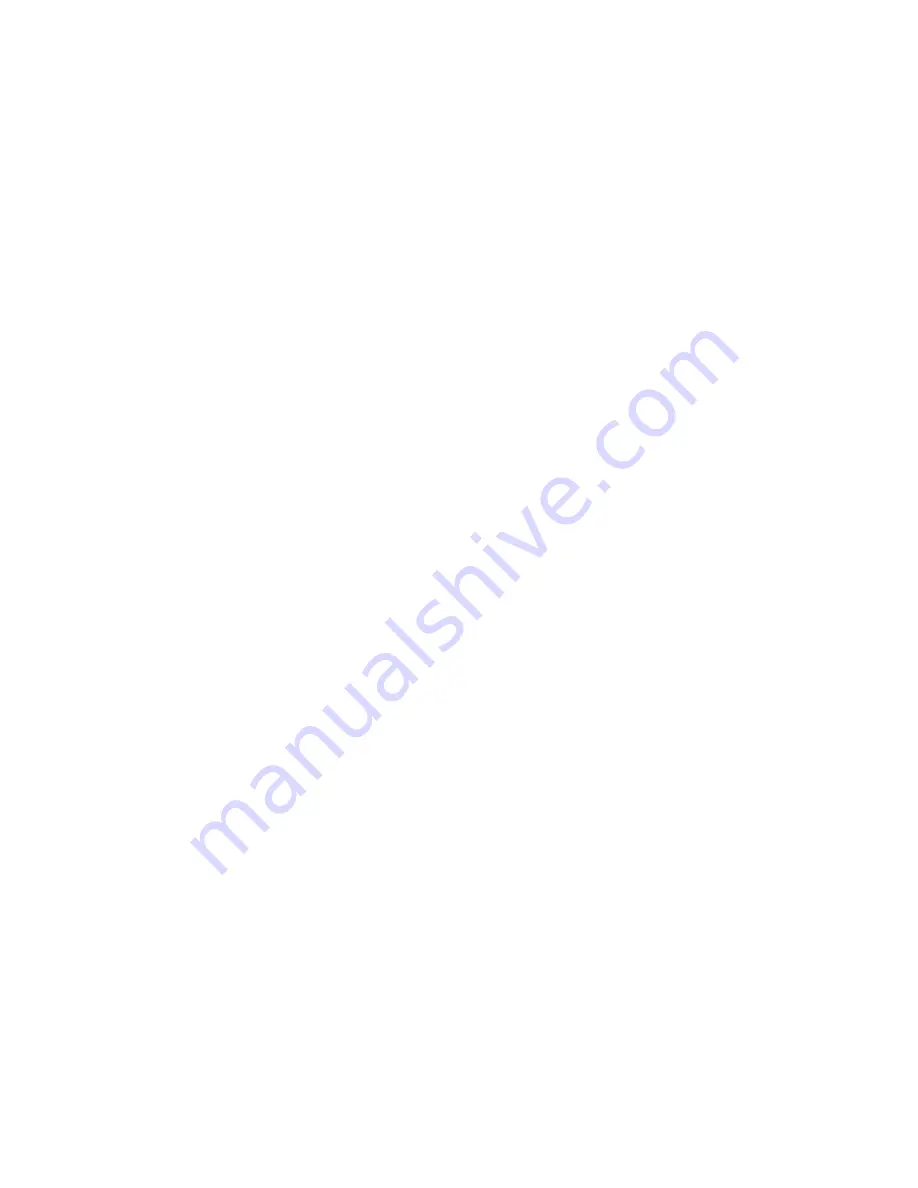
MAINTENANCE
86037580 GLIDE 01/03/07
4-8
5. SCRUB BRUSHES
There are five different types of brushes available to
cover applications from cleaning heavily soiled floors
to polishing. A pad driver is also available to take
advantage of the many cleaning pads on the market
and further add to the flexibility of the machine.
Please refer to the following to assist in selecting the
proper brush or pad for the work at hand.
UNCOATED FLOORS
Aggressive Grit
is a nylon fiber impregnated with
silicone carbide grit. It grinds away stain, soil, and
removes surface material.
Mild Grit
is a less aggressive silicone carbide grit
suitable for cleaning medium soil conditions.
Advantages are faster ground speed than nylon
bristles on light solid applications.
Nylon
is a general-purpose scrub brush with stiff
bristles.
Polypropylene
works well for maintaining concrete,
wood and tile floors.
FINISHED FLOORS
Nylon
bristles are used in a variety of applications
on coated or uncoated surfaces.
Polypropylene
bristles work on a variety of floor
surfaces. Does not soften in water
White Pads
(Polishing) are used for dry polishing to
achieve a high-gloss appearance, or surface
washing on highly polished or burnished floors.
Red Pads
(Buffing) are used for light-duty
scrubbing. When used with a mild detergent they
will provide surface cleaning without removing the
finish.
Blue Pads
(Scrubbing) are used for heavy-duty
scrubbing and light stripping. The blue pads remove
less finish than brown stripping pads yet will remove
black marks, stains and dirt.
Brown Pads
(Stripping) are used for easy and
complete removal of old floor waxes/finishes. They
will quickly remove ground in dirt, black heel marks,
and spills. When used with the proper stripper, this
pad leaves the floor clean and ready for finishing.
REPLACING OR INSTALLING SCRUB
BRUSHES
The scrub brushes should be checked before each
days work for wire, string, wear, or damage. The
scrub brushes should be replaced if brush bristles
are missing or if shorter than 5/8 inch.
NOTE: For uniform scrubbing, scrub brushes must
be replaced as a set.
28 in. & 32 in.
1.
With the scrub deck up, turn off the machine and
set the parking brake.
2.
Loosen side squeegee locking knob, and pivot
side squeegee away from scrub deck.
3.
Locate release lever on top of brush or pad
driver. With finger rotate release lever against
spring pressure counter clockwise. Brush/pad
driver will release and drop down.
4.
To reinstall, center the cut out of the release
lever plate on brush/pad driver to be installed
under the brush drive hub.
5.
Raise brush/pad drive up until assembly
contacts brush hub. Rotate slightly until drive
engages release lever plate.
6.
While holding upward pressure, rotate brush/pad
driver assembly clockwise. When fully engaged,
release lever plate will rotate under spring
pressure to lock assembly.
NOTE: Check that release plate is completely closed
and pad/brush is securely attached. Damage to
driver or brush could occur.
7.
Repeat the procedure for the opposite side of
the machine.
36 in. (Right Side and Center)
1.
With scrub deck up and retracted, turn off the
machine and set the parking brake.
2.
Loosen side squeegee locking knob and
unscrew it until it is near the top of the stud.
Remove the side squeegee assembly.
NOTE: For the best access to the center brush,
remove the right brush.