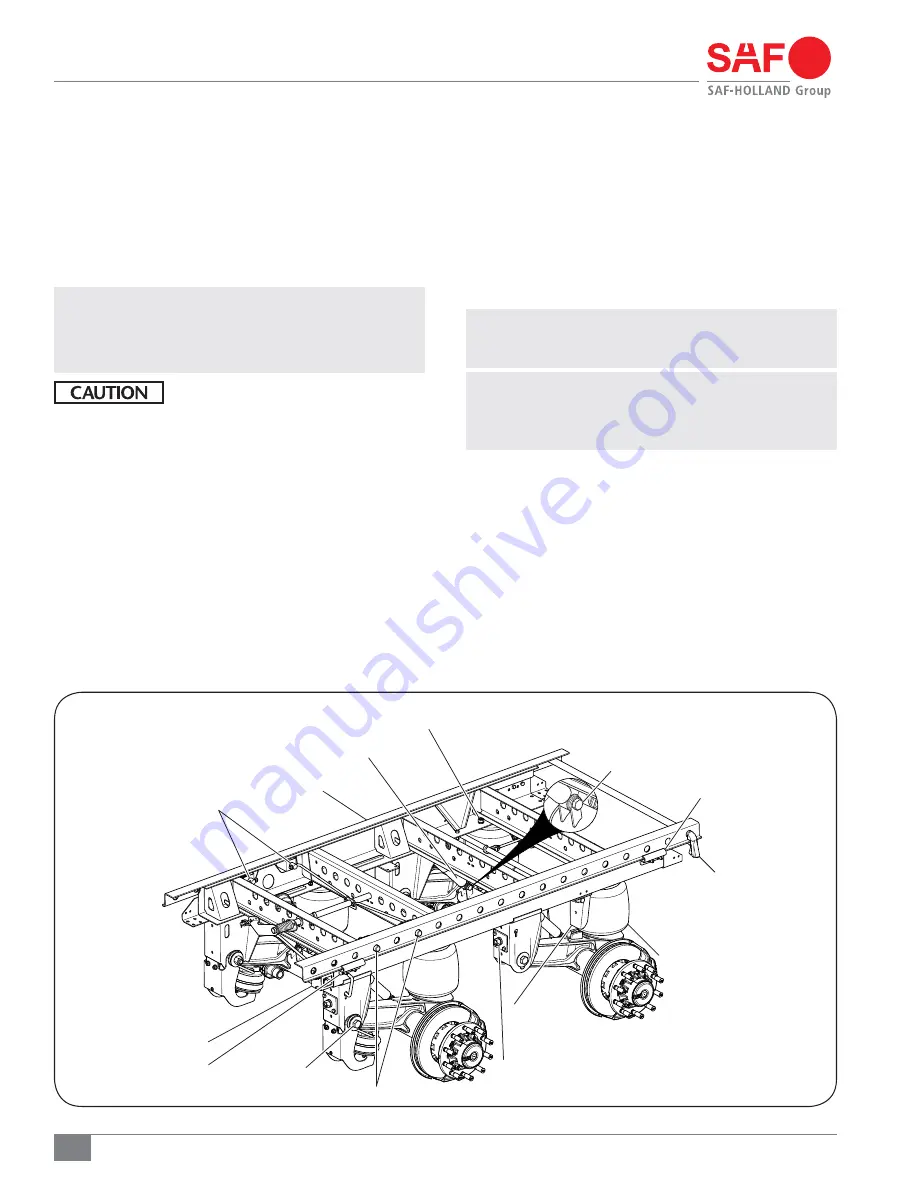
XL-AS20016BM-en-US Rev A · 2015-05-28 · Amendments and Errors Reserved · © SAF-HOLLAND, Inc., SAF-HOLLAND, HOLLAND, SAF,
and logos are trademarks of SAF-HOLLAND S.A., SAF-HOLLAND GmbH, and SAF-HOLLAND, Inc.
Pre-Operation Instructions
12
9. Pre-Operation
1. With the vehicle on a level surface, bring air system to
operating pressure, above 85 psig/5.9 bars.
2. Shut off the vehicle and inspect all air control system
fittings for air leaks by applying a soapy water solution
and checking for bubbles at all connections and fittings.
Examine the air springs
(Figure 19)
for equal firmness.
IMPORTANT:
It is the responsibility of the air system
installer to secure all air lines and check
for any air leaks. If air leaks are detected,
repair is required.
Failure to eliminate air leaks could
compromise suspension’s performance
which, if not avoided, could result in
component or property damage.
3. Exhaust the air from suspension air springs using the
valve that controls the PosiLift
™
. Refer to the plumbing
diagram in Sections 5.
4. Check the shock absorbers for proper installation and make
sure that the upper and lower 3/4" shock absorber nuts
BSFUPSRVFEUPGUMCT /tN
(Figure 19)
.
5. Verify that the 1/2" air spring mounting nuts are torqued to
GUMCT /tNBOEUIFBJSTQSJOHNPVOUJOH
OVUTBSFUPSRVFEUPGUMCT /tN
(Figure 19)
.
6. With the suspension at full capacity, check that there is a
1" (25 mm) minimum clearance around the air springs.
7. The suspension’s ride height should be within ±1/4" (6 mm)
of the recommended design height. For proper height,
refer to Slider Assembly Section 7.
8. Verify that the 1-1/8" pivot nut are torqued to 550-600 ft.-lbs.
/tN
(Figure 19)
.
IMPORTANT:
The
SwingAlign
™
design maintains proper
alignment under correct torque without
welding; DO NOT weld
(Figure 19)
.
NOTE:
SwingAlign
™
pivot connections are on roadside
and fixed alignment pivot connections are on
curbside. For SwingAlign
™
Connection Axle
Alignment procedure, refer to Section 7.
9. The vehicle is equipped with a PosiLok
™
feature, make
sure there is a 1" (25 mm) minimum clearance between
the bottom of the flipper plate and the top of the beam
pad when at ride height
(Figure 19)
.
10. Check that the slider locking pins, slider pull-bar mechanism,
and slider wear pads
(Figure 19)
are operating properly.
For slider repositioning instructions, refer to procedures
described in Section 10 of this manual.
11. Inspect the front and rear hold down clips
(Figure 19)
to make sure that they are correctly secured around the
slider body rails. Torque all 1/2" hold down clip nuts
UPGUMCT /tN
AIR SPRING
MOUNTING NUT
SHOCK ABSORBER NUT
REAR HOLD
DOWN CLIP
MANUAL
STOP BAR
FRONT HOLD
DOWN CLIP
OPTIONAL
AIR RELEASE
SLIDER LOCK PINS
SLIDER LOCK PINS
AIR SPRING
OPTIONAL
POSILOK
™
FLIPPER PLATE
SWINGALIGN
™
ADJUSTMENT NUT
Figure 19
CBX 40 SLIDER SUSPENSION WITH
AUTO-POSILIFT
™
ILLUSTRATED
1- 1/8"
PIVOT NUT
SLIDER
BODY RAILS
SHOCK ABSORBER