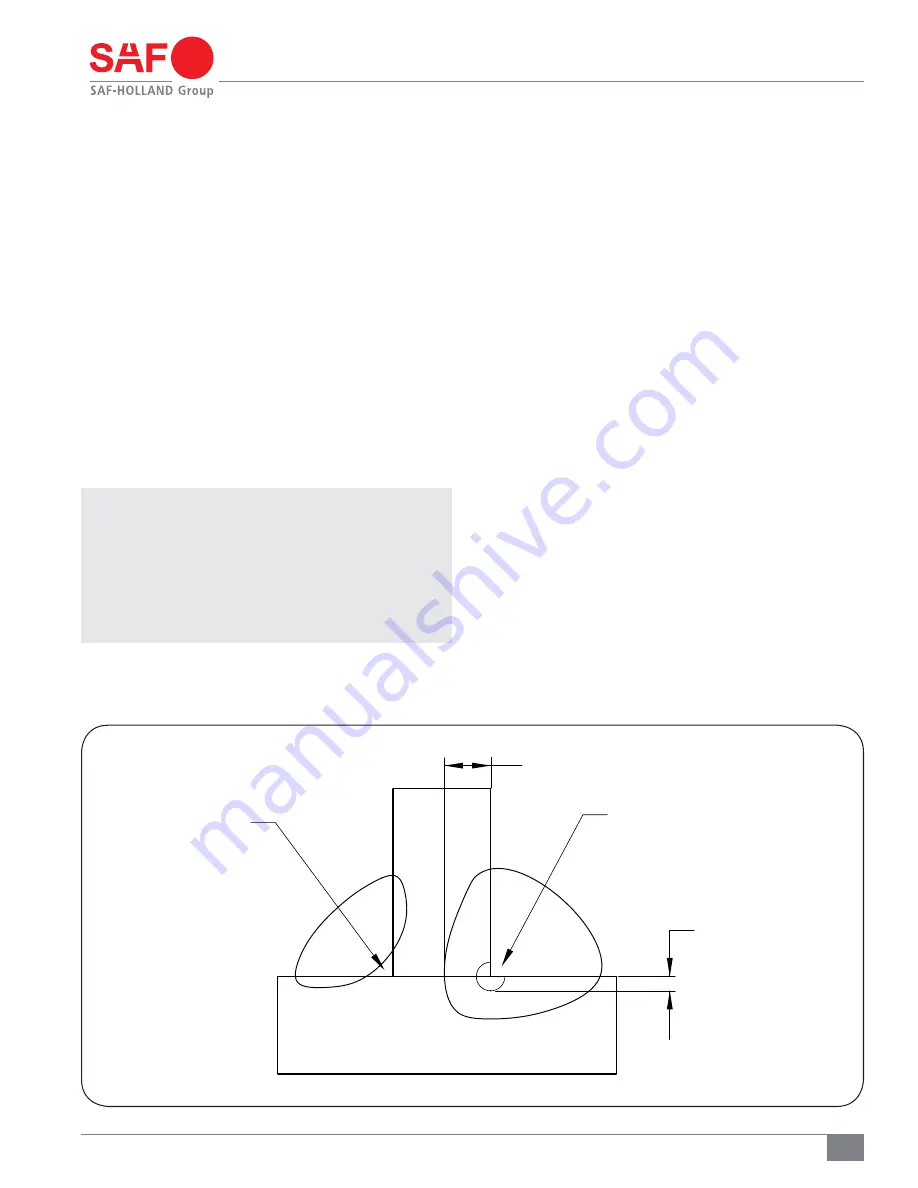
7
XL-AS20016BM-en-US Rev A · 2015-05-28 · Amendments and Errors Reserved · © SAF-HOLLAND, Inc., SAF-HOLLAND, HOLLAND, SAF,
and logos are trademarks of SAF-HOLLAND S.A., SAF-HOLLAND GmbH, and SAF-HOLLAND, Inc.
Welding Standards
4. Welding Standards
4.1 Scope
The SAF
®
suspension has been designed to be installed on a
trailer with no welding required. When welding is required for
suspension repairs, observe the requirements below. Customers
may not weld on an SAF
®
suspension without our prior approval,
including the application of the American Welding Society standards
by SAF-HOLLAND
®
engineering. This specification applies to
all components supplied by SAF-HOLLAND
®
, and its products.
The customer assumes all responsibility for weld integrity if
weld material and procedure differ from those listed below.
4.2 Material
Frame attachment components made from low carbon or
high strength alloy steel are to be welded with AWS filler
metal specification AWS A5.18, filler metal classification
ER-70S-3, ER-70S-6 or equivalent unless specified on the
installation drawing.
NOTE:
Any substitution for filler material from the above
standard MUST comply, as a minimum, with the
following mechanical properties:
Tensile Strength - 72k psi (496 MPa)
Yield Strength - 60k psi (414 MPa)
$IBSQZ7OPUDIGUMCT /tNBU
o
F (-17.7
o
C)
% Elongation - 22%
The recommended welding gas for gas metal arc welding
(GMAW) is 90% Argon/10% CO2. If a different gas is used,
welds MUST comply with penetration requirements as illustrated
below
(Figure 10)
. Where the installation drawing specifies
different than above, the drawing shall prevail.
4.3 Procedures
Tack welds used for positioning components are to be located
in the center of the final weld, where practical. Tack weld should
be completely fused to the finish weld. DO NOT break arc at the
end of the weld. Back up all finish welds at least 1/2" (12 mm)
or a sufficient amount to prevent craters at the end of the weld.
Where weld is shown to go around corners, it is assumed the
corner represents a stress concentration area. DO NOT start
or stop weld within 1" (25 mm) of the corner. Particular care
should be taken to prevent undercutting in this area.
4.4 Workmanship
It is the responsibility of the Customer to provide good workmanship
when attaching components to the frame structure.
4.5 Weld Size
If weld size is not specified, the effective throat of the
weld MUST NOT be smaller than the thinnest material being
welded
(Figure 10)
.
LACK OF FUSION OF
ANY KIND IN THIS AREA
IS NOT ACCEPTABLE AT
ANY TIME
PENETRATION AS MEASURED
THROUGH SEAM
TARGET PENETRATION TO BE
10% OF THINNEST MATERIAL
FROM INTERSECTION OF FILLET
AS ILLUSTRATED
TARGET PENETRATION
Figure 10