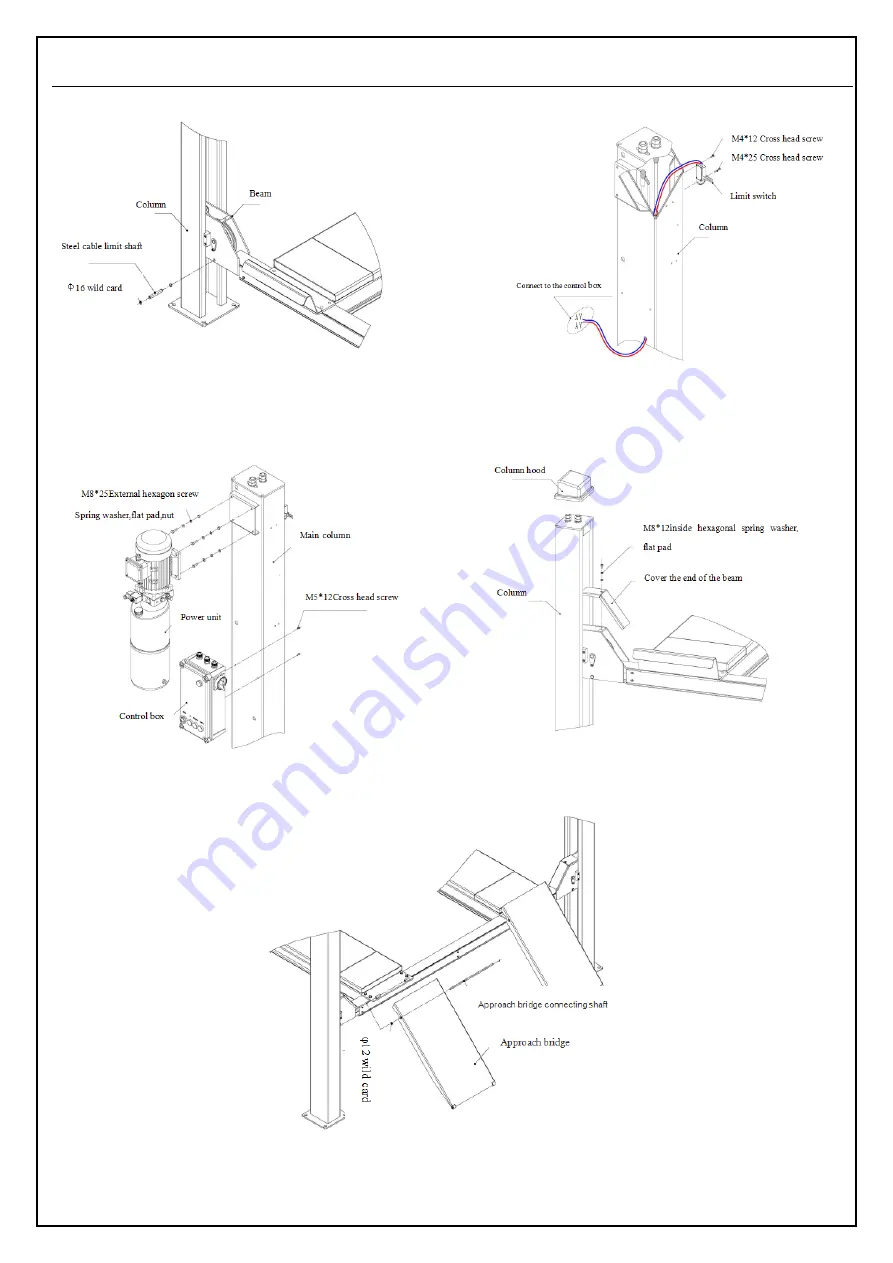
Car lift installation, operation and maintenance manual Type
:
4SF-4000B
12
Step 10
:
Install steel cable limit shaft: Step 11
:
Install top limit switch:
Step 12
:
Install power unit and control box: Step13
:
Install four column caps and beam end cover:
Step 14
:
Install approach bridge:
Step 15
:
Installation of oil pipe joints
: