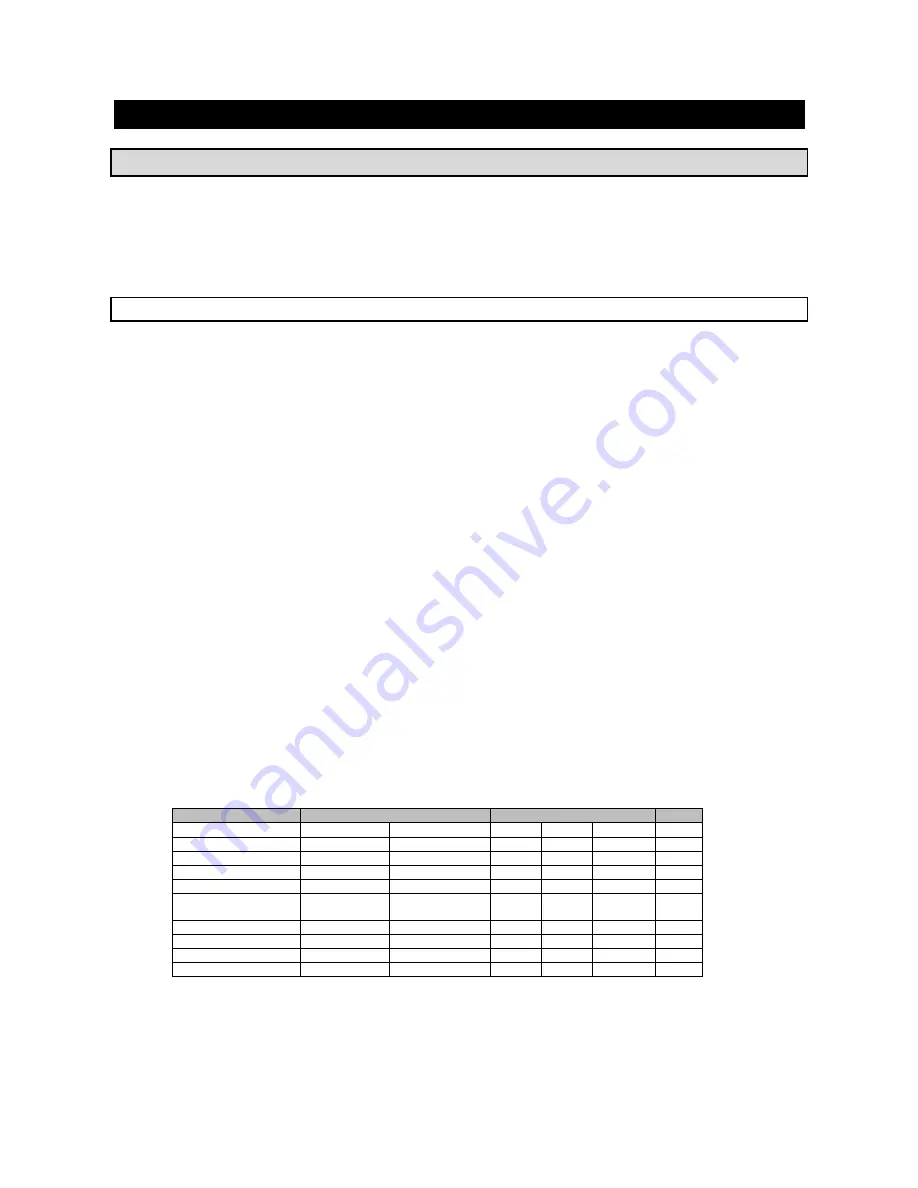
15
3270360_GB
OPERATION
GENERAL DESCRIPTION
The blast chiller is a chilling machine capable of cooling the temperature of a freshly cooked product up to
+3°C (positive chilling) and up to -18°C (negative chilling), in order to conserve it for a long period of time
without altering the organoleptic characteristics.
Machine capacity as to the quantity to be cooled depend on the model purchased.
SETTING UP
Before setting to operation thoroughly clean the cooling cabinet with a suitable detergent or sodium bycarb
dissolved in lukewarm water. Clean the appliance inside to remove any condensate caused by the
Manufacturer's final testing
.
Cooling and freezing speed depends on the following factors:
a) container shape, type and material;
b) whether container lids are used;
c) foodstuff features (density, water contents, fat contents);
d) starting
temperature;
e) thermal conduction inside the foodstuffs.
Positive /Negative quick cooling time depends on type of foodstuffs to be processed.
In general the programmes the machine is equipped with are based on the chamber temperature
management, the fan speed and the chilling time, in any case never exceed 3.6kg of load (for GN1/1, EN1/1
or 60x40 pans) or 7.2kg of load (for GN2/1, EN2/1 or 60x80 pans) and a thickness of 50mm in negative
chilling phase and 80mm in positive chilling phase (
table 2
).
Check that the positive chilling programme, up to +3°C at the product core, does not take more than 90
minutes and that the negative chilling programme, up to -18°C at the product core, does not take more than
4 hours.
We recommend pre-chilling the work chamber before beginning with a chilling programme and not covering the
food during the programme in order not to increase times.
We recommend using the core probe in order to have the exact core temperature reading. Do not stop the
cycle before reaching a temperature of +3°C during positive quick cooling and -18°C during negative
quick cooling.
Tab.2
Modello
Resa max/ciclo
Capienza
h
+70[°C]
+3[°C] +70[°C]
-18[°C]
n° max
GN
EN
DC51 - DC51M
12[kg] -
5
1/1
600x400
40
DF31 - DF31M
10,8[kg] 3,6[kg] 5
1/1
600x400
40
DF351H
10,8[kg] 3,6[kg] 5
1/1
-
-
DF41M
15[kg] 8[kg]
5
1/1
600x400
40
DF51 - DF51M
DFS51M
20[kg] 12[kg]
5
1/1
600x400
40
DF101L - DFS101L
42[kg] 25[kg]
10
1/1
600x400
40
DF141L - DFS171L
70[kg] 35[kg]
14/17
1/1
600x400
40
HP51M
25[kg] 15[kg]
6
-
165x360
120
HP101L
45[kg] 27[kg]
12
-
165x360
120