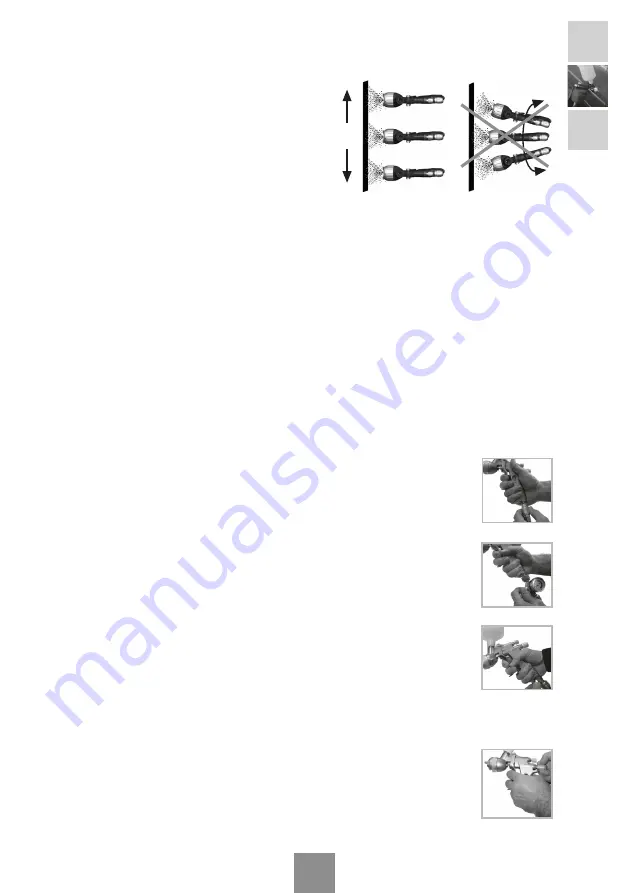
ENGLISH
24/25
OK
Open the product regulator
until the appropriate
amount of product comes out. Now you have the
maximum spraying width (spraying pattern). You can
reduce this according to your needs by closing the
spray width regulator.
Please be sure that you
put the spray gun properly
by keeping its perpendicularity to the piece to be
painted in order to achieve the maximum transfer
of the sprayed product and obtain the best finishing
quality
(Ver Fig.9).
11.1.- Clean Air
The air used for spraying must reach the gun
free of impurities, aerosols, oil, silicone and solid
particles
. To do this you must eliminate these with coalescent filter units.
The use of
air treatment equipment
with built-in pressure regulators is recommended (Models
SAGOLA 5200, 5300 or 5300 Plus).
11.2. Sufficient volume of air
A sufficient volume of air can be supplied to the gun by means of an air compressor of adequate
power
(1HP equals 110 L/min approximately), a good compressed air network and by avoiding
pressure drops through the use of
antistatic
, silicon-free
air hoses
with a minimum inside
diameter of 8 mm. and resistant to the spraying air pressure
(minimum 20 bar) and to the aggres-
sive effects of paint solvents
. Before assembling the air network, you must check on the air
tightness of the hose.
Use antistatic air hoses. Should an antistatic air hose not be available, you must attach the unit
to a ground connection
in order to eliminate any static electricity.
The total derivative resistance
must be <100 million ohms
.
11.3. Adjusting Air Pressure
11.3.1.-
Digital Pressure Gauge Version
The gun leaves the factory ready to work at an input pressure of 2 bar. In
order to change this adjustment, turn the flow regulator
clockwise until the
pressure indicated in the internal pressure gauge coincides with the required
working pressure.
11.3.2.-
Analogue Pressure Gauge Version
The gun leaves the factory ready to work at an input pressure of 2 bar. In
order to change this adjustment, turn the regulator control
, clockwise in
order to reduce the pressure and anticlockwise to increase this, until the
pressure indicated in the pressure gauge coincides with the required working
pressure.
11.3.3.-
Version without Pressure Gauge
The gun leaves the factory with the internal flow regulator fully open. In
order to adjust this to the required pressure
, turn the regulator clockwise to
reduce the inlet pressure and anticlockwise to increase this.
11.4. Amount of Product to be applied
Once the product to be applied has
been adequately diluted
, turn the Product
Regulator clockwise to reduce the amount of product and anticlockwise to
increase this.
During application,
the amount of product applicable
in areas that are small
or difficult to access can be reduced
by reducing the pressure applied with
one's finger
.
Fig.9